Технологические и метрологические рекомендации по ведению процессов притирки уплотнительных поверхностей трубопроводной арматуры
Технологические и метрологические рекомендации по ведению процессов притирки уплотнительных поверхностей трубопроводной арматуры
С.В.Сейнов – президент-научный руководитель НПО «ГАКС-АРМСЕРВИС», д.т.н., профессор, член-корр. РАПК
Притирка уплотнительных поверхностей трубопроводной арматуры производится механизированным или ручным способом с помощью притира (метод «притир по детали» или «деталь по притиру») или без него (метод «деталь по детали»), при этом способ крепления деталей при притирке должен исключать влияние упругих деформаций на притираемую поверхность. Процесс ведется с нанесением абразивной пасты на рабочую поверхность притира или детали, выполняющую роль притира, непрерывной или периодической подачей смеси, а также шаржированием (внедрением) абразива в поверхность притира.
Понятие шаржирование может быть «расширено» в случаях использования абразивного полотна различной зернистости с различными методами его закрепления на столе -притире шлифовально-доводочного станка. Закрепление осуществляется или клеевым способом или механическим. При этом должно быть обеспечено полное прилегание полотна к рабочей поверхности стола-притира.
Качество и время притирки зависят от скорости перемещения, давления на обрабатываемую поверхность и состава абразивных паст и порошков. Притирочные смеси изготавливаются по технологическим условиям потребителей. Концентрация абразива в смеси в зависимости от его зернистости и условий притирки (вручную или на станке) колеблется от 1:5 до 1:1 и устанавливается экспериментально для конкретных условий.
В зависимости от материала и требуемой шероховатости поверхности притирку следует проводить в одну или две операции (предварительно и окончательно), а при необходимости применять третью – доводочную операцию. По степени механизации выполнения работ различают притирку: ручную, машинно-ручную и механизированную.
Предварительная притирка уплотнительной поверхности производится до получения шероховатости Ra от 0,63 до 0,4 мкм
.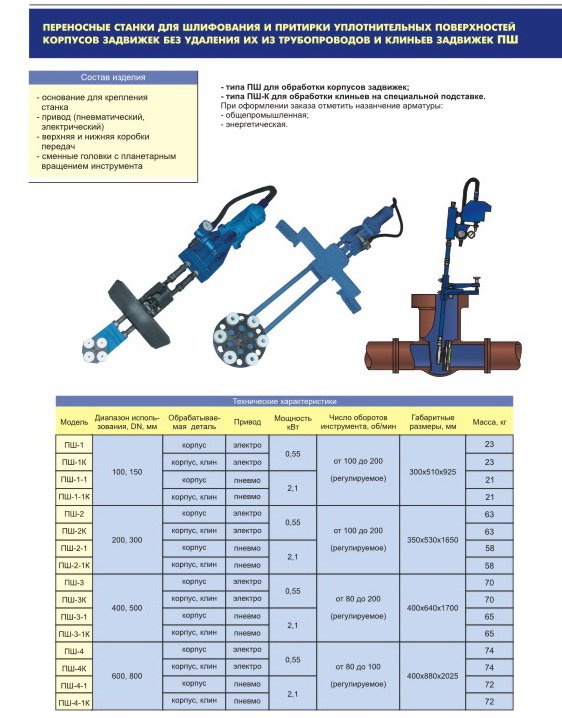
При окончательной притирке плоских поверхностей выравнивание толщины слоя притирочной пасты рекомендуется производить на притирочной плите. Для этого на поверхность притирочной плиты наносят тонким слоем абразивную пасту и растирают притиром. Притирку ведут пастой, оставшейся на рабочей поверхности притира. Оптимальная толщина слоя притирочной пасты, обеспечивающая эффективный процесс снижения отклонений формы поверхностей, колеблется в диапазоне 2-5 размеров абразивного зерна пасты.
Окончательная притирка ведется до получения шероховатости поверхности Ra от 0,32 до 0,04 мкм в зависимости от типа, назначения арматуры и требуемого класса герметичности.
Предварительная притирка производится при больших значениях скорости и давления, окончательная – при меньших.
Давление назначается в пределах от 0,04 до 0,4 МПа (от 0,4 до 4 кгс/см2) для поверхности шириной менее 1 мм.
При механизированной притирке на станках окружную скорость притира, ограничивают значениями 5-12 м/мин. При ручной притирке ограничиваются скоростями до 2 м/мин.
Допускается изменять величины давлений и окружных скоростей при условии достижения качества притираемой поверхности.
Рекомендуемая последовательность операций и припуск на доводку поверхностей деталей на специализированном оборудовании приведены в табл. 1.
Показатели качества доводки на однодисковых серийных вертикально-доводочных станках приведена в табл. 2.
Для получения наилучших результатов притирки необходимо, чтобы притир относительно притираемой поверхности совершал сложное движение (ни одна точка притира не повторяет своей прежней траектории). При притирке плоских поверхностей, в случае отсутствия направляющих у притира, последний должен медленно вращаться вокруг своей оси и быстро перемещаться вокруг оси притираемой детали, что обеспечит получение на уплотнительной поверхности петлеобразных микроштрихов.
Таблица 1
Последовательность операций доводки (притирки) | Вид доводочной операции (притирки) | Припуск на доводку, (мм) | Достигаемая точность формы, (мкм) | Достигаемая шероховатость, (мкм) |
1 | предварительная | 0,1-0,05 | 5,0-3,0 | 0,63-0,16 |
2 | получистовая | 0,05-0,03 | 2,0-1,0 | 0,16-0,04 |
3 | чистовая | 0,03-0,01 | 1,0-0,9 | 0,1-0,04 |
Таблица 2
Модель станка | Диаметр обработки деталей | До обработки | После обработки | ||||
шероховатость Ra, мкм | неплоскостность, мкм | непараллельность, мкм | шероховатость Ra, мкм | неплоскостность, мкм | непараллельность, мкм | ||
3608 | 50 | 0,32-0,63 | 5 | 5 | 0,04-0,08 | 0,9 | 1,5 |
185 | 0,32-0,63 | 9 | 8 | 0,04-0,08 | 3 | 3 | |
495 | 0,63-1,25 | 10 | – | 0,125-0,16 | 10 | – | |
3806 | 250 | 0,32-0,63 | 3 | – | 0,1-0,125 | 2,4 | – |
90 | – | 4 | 0,9 | 2 | |||
3804П | 50 | 0,32 | 6 | – | 0,065 | 0,9 | 1,5 |
150 | 0,63 | 10 | 8 | 0,1-0,125 | 1,5 | – |
При наличии у притира направляющих или при притирке конических поверхностей методом «притир по детали» или «деталь по детали» притир должен совершать возвратно-вращательное движение с углом поворота 60-90 градусов, а смещение относительно детали должно меняться так, чтобы каждая новая дуга делала перебег против предыдущей на 10-20 градусов. При притирке конических поверхностей для обеспечения постоянной смазки и равномерного перемещения притирочной пасты на притираемой поверхности, притир или деталь следует приподнимать через каждые один или два поворота.
Прогрессивным считают в арматуростроении вибрационный метод притирки. Однако он не получил пока распространения вследствие недостаточной изученности качества поверхности, полученной после использования этого метода притирки. По некоторым данным при оптимальных режимах вибрационной притирки обеспечивается шероховатость поверхности по критерию Ra в диапазоне 0,04-0,02 мкм. Данные по погрешностям формы и волнистости отсутствуют.
Допускаются другие виды обработки, обеспечивающие требуемые значения отклонений формы и шероховатости уплотнительной поверхности.
Притирка уплотнительных поверхностей деталей арматуры серийного и крупносерийного производства выполняется, как правило, на специальных станках, а в мелкосерийном, единичном и ремонтном производстве используются радиальные и вертикально-сверлильные станки со специальными приспособлениями.
Для притирки уплотнений арматуры возможно использование притирочных суспензий и паст, которые приготавливаются на машиностроительных предприятиях. Характеристика и назначение суспензий и паст приведена в табл. 3.
Для доводки уплотнительных поверхностей из коррозионных нержавеющих сталей и твердых сплавов наибольшей химической активностью обладает олеиновая кислота. Сравнительные данные съема металла в единицу времени в зависимости от применяемой жидкости для доводки (притирки) приведены в табл. 4.
Индустриальное масло в притирочных материалах необходимо для предотвращения микроцарапин на уплотнительных поверхностях.
Для предохранения притертых поверхностей от повреждений как при обработке, так и после нее, необходимо тщательно удалять с них загрязнения до и после притирки.
После каждого вида притирки, в зависимости от состава притирочного материала, уплотнительную поверхность следует промыть моющими средствами, обеспечивающими необходимую чистоту и обезжиривание поверхности, и просушить.
Таблица 3
Вид абразива | Зернистость | Содержание абразива, % | Компоненты | Содержание компонентов, % | Метод доводки (притирки) | Назначение доводки (притирки) |
Карбид кремния | М20-М40 | 5-10 | керосин | 40-50 | с непрерывной подачей суспензии | получистовая для стальных деталей |
масло веретенное | 24-50 | |||||
стеарин | 3-10 | |||||
Электрокорун | М20-М40 | 30-40 | масло веретенное | 23-40 | пастами или с периодической подачей суспензии | получистовая для мягких сталей, цветных металлов |
масло вазелиновое | 40-60 | |||||
стеарин | 10-20 | |||||
Карбид кремния, Электрокорун | М10-М28 | 5-10 | керосин | 50-60 | с непрерывной подачей суспензии | получистовая и чистовая для закаленных сталей |
масло веретенное | 15-20 | |||||
стеарин | 10-20 | |||||
Алмазы синтетические | М28-М10 | 0,6-2,0 | стеарин | 10 | подача суспензии непрерывная | чистовая для труднообрабатываемых материалов, твердых сплавов |
парафин | ||||||
Карбид бора | М28-М10 | масло индустриальное | 25 | |||
керосин | 55 |
Таблица 4
Доводочная жидкость | Съем металла при равных условиях, мкм |
Масло индустриальное | 7 |
Вода | 12 |
Керосин | 18 |
Кислота олеиновая | 22 |
Очистка деталей производится одним из следующих методов: местной промывкой, струйным обливом, многократным погружением в обезжиривающие и промывающие жидкости, где очищение поверхностей проводится с применением ультразвуковых колебаний или другими способами по технологии предприятия-изготовителя арматуры.
Качество притирки уплотнений в арматуростроении оценивается двумя методами:
а) сравнением действительных значений параметров шероховатости, волнистости и отклонений формы с их предписанными значениями;
б) пневмо-гидравлическими испытаниями подвижных и неподвижных уплотнительных соединений.
При выборе средств контроля качества притирки для оценки действительных значений функциональных параметров следует руководствоваться принципом предпочтительности. Он предполагает приоритет в выборе наиболее прогрессивных методов измерения или контроля. При невозможности его обеспечения или использования обращаются к методам численной оценки. В последнюю очередь можно использовать качественные методы.
Пневмо-гидравлические испытьания как методы контроля качества притирки дают высокую достоверность сиюминутного состояния контактного взаимодействия уплотнения. Однако, не могут быть использованы для прогнозной оценки. Сочетание методов сравнения параметров и испытаний наиболее предпочтительно.
Установление действительных значений параметров шероховатости и волнистости должно осуществляться профилометрами или профилографами-профилометрами различных конструкций. Образцы шероховатости по ГОСТ 9378 могут быть только условно рекомендованы, так как их применение дает очень низкую достоверность оценки.
Отклонения от плоскостности и прямолинейности кольцевых плоских уплотнений проверяют с помощью кругломеров, на основе прямых измерений, а также с помощью профилографов-профилометров, с использованием специальной методики, разработанной в НПО «ГАКС-АРМСЕРВИС»; поверочных плит по ГОСТ 10905 и поверочных линеек по ГОСТ 8026 и специализированных красок; «на просвет».
Отклонение формы конических поверхностей шириной более 2 мм проверяется методом «на краску» по сопрягаемой детали или специальным шаблоном.
При проверке «на краску» на рабочую поверхность контрольной плиты (при проверке плоских поверхностей), образца ( при проверке конических поверхностей) или сопрягаемой детали (при проверке конических деталей «деталь по детали») следует нанести тампоном тонкий слой краски, позволяющий оставить след на сопрягаемой поверхности, установить плиту (образец или сопрягаемую деталь) на проверяемую поверхность и произвести несколько перемещений. Качество поверхности определяется площадью прилегания уплотнительной поверхности, которая должна составлять 80-90% от общей площади уплотнительной поверхности. При проверке (на краску) уплотнительных поверхностей площадь контакта (краска) не должна иметь разрывов по всему периметру.
Краска – углерод технический К-354 ГОСТ 7885 или лазурь железная ГОСТ 21121, применяемая для проверки, должна разводиться индустриальным маслом И-20А или И12А по ГОСТ 20799 до вязкости 25-38 сСт. Количество краски в каждом случае определится конкретно, исходя из контролируемой площади. Краска наносится тампоном или копиллярной стеклянной трубкой и растирается по всей поверхности контрольной плиты (образца, сопрягаемой детали). Толщина слоя наносимой краски определяется экспериментально.
Окончательной оценкой качества притертой поверхности является испытание изделия на герметичность, проводимое в соответствии с требованиями НТД на каждый тип трубопроводной арматуры.
НИОКР – Переносной шлифовальный и притирочный станок для обработки уплотнительных поверхностей запорной арматуры
НИОКР — Переносной шлифовальный и притирочный станок для обработки уплотнительных поверхностей запорной арматуры
Главная > Статьи > НИОКР — Переносной шлифовальный и притирочный станок для обработки уплотнительных поверхностей запорной арматуры
09 сентября, 2021
Основной задачей на старте проекта была реализация современных инновационных идей по повышению уровня качества процесса ремонта трубопроводной арматуры, так как восстановление арматуры в настоящее время является целесообразным и актуальным.
Компанией СКБ ПОБЕДИТ разработан инновационный станок ПОБЕДИТ-СПМ-1 (рис. 1), предназначенный для шлифования и притирки уплотнительных поверхностей корпусов клиновых задвижек без удаления их из трубопровода, а также обработки клиньев. Отличительной особенностью станка является запатентованная система подачи притирочной эмульсии различной консистенции в зону обработки, что значительно сокращает процесс притирки арматуры и обеспечивает восстановление уплотнительной поверхности.
Научно-исследовательская опытно-конструкторская работа состояла из двух этапов: разработка конструкторской документации и сборка осуществлялись на первом этапе, а ресурсные испытания станка проходили на втором этапе НИОКР. Специалистами компании проводился тщательный анализ технических решений ремонта трубопроводной арматуры, на основании чего был выявлен потенциал, который лег в основу разработок инновационного оборудования. Эскиз преобразовался в чертеж, изготовлены все необходимые детали и узлы, затем осуществлена сборка станка.
Для подтверждения производительности внедренных инновационных решений по разработанной программе и методике проведены испытания станка для шлифования и притирки уплотнительных поверхностей клиновых задвижек ПОБЕДИТ-СПМ-1, включающие в себя проведение климатических испытаний, испытаний на электромагнитную совместимость, ресурса станка, а также его работоспособность и функциональность. Испытания проводились в собственной лаборатории и сертифицированных лабораториях КОНЦЕРНА «АВТОМАТИКА» АО «ПО «ЭЛЕКТРОПРИБОР» г. Пенза и Квалифицированной лаборатории Центра контроля машин и оборудования ИЛ 73 г. Ульяновск (Рис. 3).
- Рис. 2
- Рис. 3
В процессе реализации НИОКР зарегистрирован результат интеллектуального труда – получен Патент на полезную модель «ПЕРЕНОСНОЙ СТАНОК ДЛЯ ШЛИФОВКИ И ПРИТИРКИ УПЛОТНИТЕЛЬНОЙ ПОВЕРХНОСТИ ЗАДВИЖКИ БЕЗ ЕЁ ДЕМОНТАЖА С ТРУБОПРОВОДА» (Рис. 4).
Основные преимущества станка.
Применение системы подачи притирочной эмульсии в зону обрабатываемой поверхности значительно сокращает время притирки и восстановления герметичности. Мобильность станка позволяет осуществлять ремонт непосредственно на месте установки арматуры. Широкое применение в конструкции станка высокопрочных алюминиевых сплавов позволяет снизить массу оборудования и облегчить его монтаж на обрабатываемых изделиях. Применение шлифовальных дисков на самоклеящейся основе не требует правки и выверки, их достаточно заменить на новые при износе.
Переносной станок для шлифования и притирки трубопроводной арматуры ПОБЕДИТ-СПМ-1 наиболее востребован предприятиями энергетического комплекса РФ: ТЭС, ТЭЦ, АЭС, химической отрасли: НПЗ, ГПЗ, прочими производствами, а особенно актуально для предприятий, которые используют трубопроводную арматуру с типом присоединения «под приварку». Данное решение значительно уменьшает финансовые издержки компаний путем сокращения времени простоя трубопроводов, за счёт оперативного восстановления герметичности, изношенной уплотнительной поверхности трубопроводной арматуры.
Научно-исследовательская опытно-конструкторская работа (НИОКР) реализована при поддержке Федерального государственного бюджетного учреждения «Фонд содействия развитию малых форм предприятий в научно-технической сфере» (Фонд содействия инновациям).
Читайте ещё:
СТЕНД ДЛЯ ИСПЫТАНИЙ И НАСТРОЙКИ ПРЕДОХРАНИТЕЛЬНЫХ КЛАПАНОВ ПОБЕДИТ-С-1М
ТЕХНОЛОГИЯ СБОРКИ И РАЗБОРКИ ТРУБОПРОВОДНОЙ АРМАТУРЫ
РЕМОНТ ТРУБОПРОВОДНОЙ АРМАТУРЫ
Фиксатор фитингов | Ремонт протекающих фитингов на месте
Rated 5.00 из 5 на основе 5 отзывов покупателей s уплотнительная поверхность фитингов из стали и алюминия 37°.
– Бесплатная доставка заказов на сумму более 99 долларов США в континентальной части США.
– Международные заказы: пожалуйста, , свяжитесь с нами , чтобы разместить заказ.
ПАТЕНТ США 9,943,942 B2
* Размеры соответствуют наружному диаметру трубки. См. таблицу резьбы JIC ниже.
* Малый набор: 3/16″ – 1/2″
* Большой набор: 5/8″ – 1″
Выберите размер для просмотра изображения и номера детали
Артикул: Н/Д Категория: Инструменты для запечатывания жестких линий Теги: примерка, ремонт, шлифовка, инструмент
- Описание
- Отзывы (5)
- Дополнительная информация
Описание
youtube.com/embed/ukk2LRSV_CU?autoplay=0&controls=1&fs=1&modestbranding=0&theme=dark&rel=0&loop=0&showinfo=1″ frameborder=”0″ allowfullscreen=”true”>Описание
Несовершенство уплотнительной поверхности фитинга может привести к утечке. А если это приварная пробка? Раньше вам приходилось заменять фитинг, что было большой головной болью, но теперь вы можете отремонтировать его на месте. Фитинг Fixer использует притирочную головку с перевернутым конусом, покрытую алмазной пылью, для ремонта конической поверхности и восстановления уплотнения с помощью развальцованной трубки.
Использовать этот инструмент просто. Поврежденный фитинг ввинчивается в направляющую, удерживающую его на месте. Затем подсоедините притирочную головку к дрели и прокрутите ее с перерывами примерно полдюжины раз. Осмотрите уплотнительную поверхность, чтобы увидеть, нет ли каких-либо дефектов. Если повреждение все еще видно, повторите процесс притирки, пока не получите чистую поверхность.
Использование фиксатора фитинга
1. Вкрутите фитинг в направляющую соответствующего размера.
2. Подсоедините притирочную головку к сверлу, выдвинув ее не менее чем на 1/4 дюйма от конца патрона.
3. Удерживая притирочную головку вверх, распылите в полость легкую смазку. Это позволяет смазке оставаться внутри.
4. Вставьте притирочную головку в направляющую и над фитингом.
5. Вращайте притирочную головку на фитинге, отпуская каждые 2-3 секунды , чтобы предотвратить засорение остатками абразива.
6. После 5-6 проходов дрелью снимите фитинг. Затем очистите и осмотрите уплотнительную поверхность. При необходимости повторите шаг 5.
Размеры
Притирка и полировка поверхностей механического уплотнения
Распространенные типы поверхностей механического уплотнения:
Углерод, карбид вольфрама, керамика, карбид кремния, оксид хрома, стеллит, нирезист и фосфористая бронза.
Машинная притирка – это производственный метод притирки поверхностей механических уплотнений. Системы притирки Kemet используются как в производственных процессах, так и в процессах восстановления. Следующие методы применимы к стационарным и отдельно стоящим станкам, а также к системам ручной притирки Kemet.
Размер используемой машины обычно определяется наибольшим уплотнением, которое необходимо притереть. Например, машина Kemet 15 может притирать уплотнения диаметром примерно до 125 мм (5 дюймов), тогда как машина Kemet 24 потребуется, если необходимо притирать уплотнения диаметром до 200 мм (8 дюймов). В большинстве случаев, если принять следующие процедуры, можно будет производить высококачественные отражающие поверхности, плоские до менее 2 фунтов (0,0006 мм)
Многие материалы, используемые для изготовления механических уплотнений, в настоящее время слишком тверды, чтобы их можно было использовать. притираются старомодными обычными абразивами, такими как оксид алюминия и карбид кремния. Композитная притирочная пластина Kemet с алмазной суспензией обеспечивает хорошую скорость резания, а поверхность с высокой отражающей способностью означает, что этап вторичной полировки не требуется.
Плоские притирочные системы Kemet подходят для большинства притирочных станков диаметром до 72 дюймов, но для большинства мастерских по ремонту уплотнений подходят 15-дюймовые или 24-дюймовые станки.
Любой обычный притирочный станок можно преобразовать в алмазную систему Kemet, просто заменив существующую пластину подходящей пластиной Kemet и установив соответствующую распылительную систему Kemet. Существующие контрольные кольца все еще используются, но требуют фасок на их внешних краях, чтобы облегчить алмазную пропитку пластины Kemet. После переоборудования станка процесс притирки/полировки полностью автоматизирован.
Поскольку перерабатывающая способность системы Kemet настолько эффективна, алмазный шлам используется очень мало. Высокий расход расходных материалов, характерный для обычной притирки, не возникает, и поэтому утилизация этого ненужного материала больше не является проблемой.
Плоскостность притирочной пластины
Плоские механические уплотнения могут изготавливаться только на плоских притирочных пластинах. Поэтому очень важно регулярно проверять плоскостность листа. Это самый важный навык, которым необходимо овладеть при работе на плоскопритирочном станке.
Типовые настройки дозатора Kemet при притирке механических уплотнений и клапанов
15-дюймовый станок | 24-дюймовый станок | ||
---|---|---|---|
Алмаз | Жидкость | Алмаз | Жидкость |
2 секунды Продолжительность 20 секунд Интервал | 1 секунда Длительность 120 секунд Интервал | 2 секунды Длительность 20 секунд Интервал | 2 секунды Длительность 40 секунд Интервал |
Дозатор должен быть настроен на распыление с указанными выше интервалами, при этом оба регулятора давления воздуха в задней части алмазного дозатора должны быть установлены на 1/2 бара (7,5 фунтов на квадратный дюйм). Притирочную пластину следует сначала зарядить в течение 10 минут, запустив машину и нанеся указанное выше количество распыляемого материала.
При притирке или полировке важно следить за тем, чтобы притирочная пластина не была ни слишком влажной, ни слишком сухой. Если пластина слишком влажная, алмаз заливается смазкой, и съем материала будет очень низким; если пластина слишком сухая, детали могут вступить в непосредственный контакт с притирочной пластиной, а это отрицательно скажется на полученной чистоте поверхности и вызовет нагрев пластины.
Затем уплотнения можно притереть, поместив их внутрь управляющих колец машины и приложив к ним давление. Если несколько деталей должны быть притерты внутри одного кондиционирующего кольца, важно, чтобы они были одинаковой толщины (+/- 0,5 мм). Чтобы удерживать детали на месте во время притирки, следует изготовить либо рабочий держатель (иногда называемый гнездом). Обычно это 3-миллиметровый диск Tufnell с профилем деталей, которые должны быть притерты к нему. В качестве альтернативы сами грузики могут быть облицованы комплектом облицовки Kemet. Этот специальный материал обладает противоскользящими свойствами, которые удерживают детали на месте во время притирки без необходимости использования рабочего держателя.
Одиночные уплотнения могут свободно перемещаться внутри управляющего кольца, но важно приложить вес для оптимального съема материала. Этот вес должен быть сбалансирован. Идеальным грузом является большой стальной шар, который можно просто положить поверх уплотнения. Также рекомендуется поместить резиновую ленту вокруг одиночных уплотнений, поскольку это обеспечивает их движение внутри управляющих колец, что позволяет избежать следов на притирочной пластине. .
Примерные варианты применения под давлением
Углерод 100 г/см² | Карбид вольфрама 300 г/см² | Карбид кремния 90 004 200 г/см² | Керамика 600 г/см² |
Никель Железо 200 г | Стеллит 200 г/см² | Оксид хрома 300 г/см² | Напыление 200 г/см² |
Если необходимо притирать большое уплотнение на относительно небольшом притирочном станке, то можно снять контрольное кольцо и заменить уплотнение, которое затем будет перемещаться в узле бугеля ролика.
Создание выпуклой поверхности на торце механического уплотнения
Во время любой операции притирки притирочные детали будут отражать форму притирочной пластины. Именно по этой причине притирочные пластины обычно поддерживаются в чрезвычайно плоском состоянии (обычно менее 0,004 мм), чтобы притираемые детали отражали эту плоскостность.
Для некоторых применений требуется выпуклая поверхность, поэтому в этих случаях притирочная пластина должна быть вогнутой до того, как вы начнете притирку деталей. Вогнутая притирочная пластина создаст выпуклую часть, потому что эта деталь зеркально отражает пластину.
Величина необходимой вогнутости будет зависеть от требуемой выпуклости, а также от размера и площади поверхности деталей, подлежащих притирке.
- Чтобы создать вогнутую притирочную пластину, расположите все кондиционирующие кольца как можно ближе к центру пластины.
- Используйте Kemox 0400-S или подходящий обычный абразивный раствор для создания вогнутости.
Не используйте не алмаз.
- Не притирайте детали, пока не будет сформирована вогнутость. Начните с кондиционирования пластины, пока она не станет вогнутой на 0,020 мм.
- После создания этой вогнутости очистите пластину и кольца, а затем заполните пластину соответствующей алмазной суспензией Kemet для конкретного применения.
- Притрите деталь как обычно внутри кондиционирующего кольца.
- Проверьте плоскостность детали и при необходимости отрегулируйте форму пластины.
Создание вогнутости может занять много времени, поэтому при производстве мы рекомендуем сохранить пластину специально для этого поколения выпуклых граней. В идеале вместе с пластиной должен храниться специальный набор кондиционирующих колец.
Kemet рассчитает пластину точной формы, необходимую для операций вогнутой/выпуклой притирки. Мы также предлагаем контрактные услуги притирки и бесплатное тестирование
Притирка и полировка углерода
Требования к испытаниям: Найти подходящий процесс притирки для подпружиненных углеродных уплотнений.