Гост и Снип по сварке металлоконструкции
NDT-2014
Свой
- #1
Здравствуйте, уважаемые дефектоскписты.
Нужен Гост и Снип по сварке металлоконструкции (катет шва, выпуклост шва на тавровых сварных соединениях)
Заранее благодарью!
Игорь Антонович
Дефектоскопист всея Руси
- #2
NDT-2014 написал(а):
Здравствуйте, уважаемые дефектоскписты.
Нужен Гост и Снип по сварке металлоконструкции (катет шва, выпуклост шва на тавровых сварных соединениях)
Заранее благодарью!
Нажмите для раскрытия…
Не мешало бы и вид сварки указать.
Singelschucher
Специалист
- #3
Какой металлоконструкции?
Есть строительные металлоконструкции, причём разной поднадзорности; металлоконструкции подъёмных сооружений; корпусные металлоконструкции (вагоны, платформы, корпуса судов). Чего надо-то?
kvn505
Бывалый
- #4
ГОСТ 5264-80 Ручная дуговая сварка. Соединения сварные. Основные типы, конструктивные элементы и размеры.
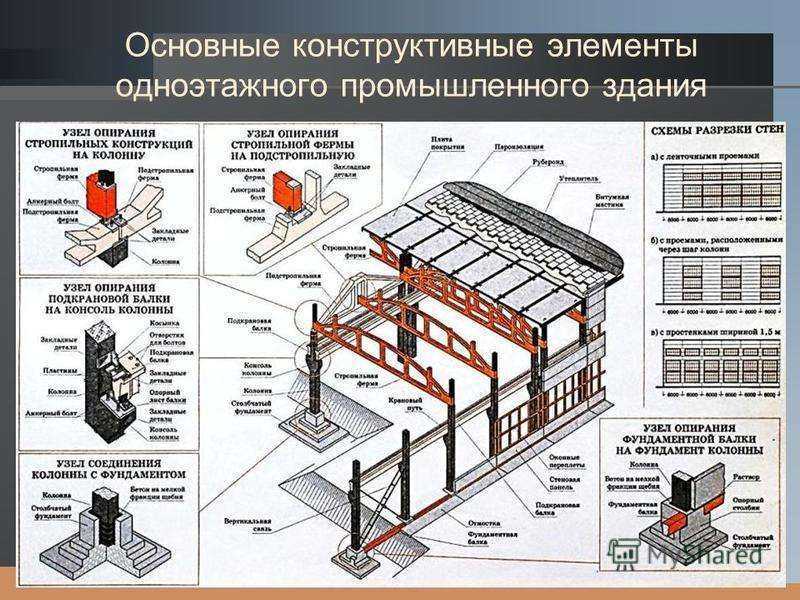
ГОСТ 8713-79 Сварка под флюсом. Соединения сварные. Основные типы, конструктивные элементы и размеры
Тарас
Дефектоскопист всея Руси
- #5
СНиП 3.03.01-87 “Несущие и ограждающие конструкции”
РД 34.15.132-96 “СВАРКА И КОНТРОЛЬ КАЧЕСТВА СВАРНЫХ СОЕДИНЕНИЙ МЕТАЛЛОКОНСТРУКЦИЙ ЗДАНИЙ ПРИ СООРУЖЕНИИ ПРОМЫШЛЕННЫХ ОБЪЕКТОВ”
Тарас
Дефектоскопист всея Руси
- 02.2016″ data-time-string=”07:28″ title=”29.02.2016 в 07:28″ itemprop=”datePublished”>29.02.2016
- #6
СНиП III-18-75 “МЕТАЛЛИЧЕСКИЕ КОНСТРУКЦИИ.”
Singelschucher
Специалист
- #7
Всё не так.
СНиП III-18-75 давно отменён. РД 34.15.132-96 вроде применяется.
Группа объектов СК пп.1, оно же группа объектов контроля п.11:
- СП 16.13330.2011 Стальные конструкции.
Актуализированная редакция СНиП II-23-81* (требования при проектированим м/к)
- СП 70.13330.2012 Несущие и ограждающие конструкции. Актуализированная редакция СНиП 3.03.01-87 (монтаж м/к)
- ГОСТ 23118-99 “Конструкции стальные строительные. Общие технические условия” (изготовление м/к)
- СП 53-101-98 “ИЗГОТОВЛЕНИЕИ КОНТРОЛЬ КАЧЕСТВА СТАЛЬНЫХ СТРОИТЕЛЬНЫХ КОНСТРУКЦИЙ” (изготовление м/к)
Геометрические параметры швов сварных соединений в указанных нормативных документах применяются по требованиям ГОСТов на сварные соединения, номера ГОСТов указаны в сообщении 4 этой темы. Если в нормативных документах на объекты не оговорено иное, применять нормы браковки по ГОСТам на сварные соединения.
astrut
Дефектоскопист всея Руси
- 02.2016″ data-time-string=”23:49″ title=”29.02.2016 в 23:49″ itemprop=”datePublished”>29.02.2016
- #8
Singelschucher написал(а):
п.11
Нажмите для раскрытия…
Точнее, 11.1
Singelschucher написал(а):
Если в нормативных документах на объекты не оговорено иное, применять нормы браковки по ГОСТам на сварные соединения.
Нажмите для раскрытия…
Где в ГОСТах на сварку нормы допустимых несплошностей? Там только геометрия и то не вся.
Singelschucher
Специалист
- 03.2016″ data-time-string=”04:54″ title=”01.03.2016 в 04:54″ itemprop=”datePublished”>01.03.2016
- #9
astrut написал(а):
Точнее, 11.1
Нажмите для раскрытия…
Да, так.
astrut написал(а):
Где в ГОСТах на сварку нормы допустимых несплошностей? Там только геометрия и то не вся.
Нажмите для раскрытия…
Хорошо. Замечание принято. Так сойдет?
Singelschucher написал(а):
Если в нормативных документах на объекты не оговорено иное, применять нормы браковки к основным крнструктивным элементам и размерам швов сварных соединений по ГОСТам на сварные соединения.
Нажмите для раскрытия…
Но и я сделаю замечания к вашему посту. ГОСТ не на сварку (сварка – это технологический процесс), а на сварные соединения для определенного способа сварки.
Сварные соединения металлоконструкций: виды и контроль качества
- Главная >
- Блог >
- Сварные соединения металлоконструкций: виды и контроль качества
27.09.2022
Сварка
Время чтения: 7
Редакция сайта VT-MetallСохранить статью:
Из этого материала вы узнаете:
- Виды сварных соединений металлоконструкций
- Требования и виды качества сварных соединений
- 6 методов контроля качества сварных соединений металлоконструкций
- Оформление документации на сварные соединения металлоконструкций
Сварные соединения металлоконструкций должны отвечать строгим нормам качества, чтобы итоговое изделие было прочным и надежным. В зависимости от назначения и материала конструкции используются различные соединения, к каждому из которых предъявляются свои требования.
Не менее важны способы контроля качества сварных швов. Только после необходимых процедур и заполнения документации изделие можно эксплуатировать. В нашей статье мы расскажем, какие бывают сварные соединения и как проверить их на прочность и соответствие нормам и требованиям.
Виды сварных соединений металлоконструкций
Различается несколько классификаций сварных соединений металлоконструкций:
- По типу примыкания двух заготовок.
- По виду сварного шва.
- В зависимости от технологии сварки.
- С учетом обстоятельств, при которых проводится сварка.
- В зависимости от толщины заготовок.
- С учетом марки стали, из которой сделаны детали.
В зависимости от типа размещения деталей выделяют четыре разновидности стыковых соединений:
- Вплотную, где две заготовки в одной плоскости присоединены друг к другу.
- С наложением, когда детали заходят краями одна на другую.
- Соединение углом. В этом случае две детали находятся под углом друг к другу.
- Соединение в виде буквы Т. Здесь одна заготовка торцом примыкает к другой.
Самыми распространенными сварными соединениями металлоконструкций являются швы вплотную и угловые. Рассмотрим далее, как их получают.
Для стыкового соединения либо применяют выводные планки, либо проваривают шов во всю толщину заготовки. При выполнении работы за пределами цеха можно проводить одностороннюю сварку, в дальнейшем подваривая корень сварного шва. Таким образом, весь зазор заполняется по одной из кромок.
Следующая технология – с выводными прокладками – имеет много отличий от предыдущей. В первую очередь, прокладки расположены со стороны кромок свариваемых частей. Между кромками должно быть расстояние до 7 мм – при ручной сварке, а при механизированной – 16 мм. Толщина подкладки выбирается с учетом недопущения образования прожога во время сварки, а ток выставляется с учетом режима сварки.
В стыковках металлоконструкций часто можно встретить заготовки разной толщины. При этом с помощью фрезеровки или строжки устанавливается угол наклона более толстой кромки, равный уклону 1:8 для растянутых элементов металлоконструкции (таких, как подвески и консоли), и 1:5 – для сжатых элементов (опоры, стойки).
Сварные узлы играют роль основных стыковых соединений, несущих всю металлоконструкцию. Исходя из этого, уже во время проектирования стараются разработать благоприятные условия для сварки стыков. Для этого надо:
- Проводить в сварных узлах стыковочное соединение или угловое.
- Делать сварки в нижнем положении.
- Использовать механизированную или автоматическую сварку, а не ручную.
К множеству видов сварных узлов предъявляют различные требования. Например, при выполнении балочного узла большую роль играет расположение сварочных швов относительно друг друга. Расстояние между ними должно быть не меньше десятикратной толщины самого толстого металлопрофиля, входящего в состав этого узла.
Есть и другой момент, не влияющий на качество сварных соединений металлоконструкций. Существует два понятия: местная прочность и непрочность. Первое – это сварочные участки с приваренными косынками, ребра жесткости, накладки и пр. Ко второй относят все имеющиеся вырезы на элементах металлических конструкций, отверстия, непровары швов, зазоры и щели в стыках.
Когда оба участка есть в конструкции, то ее саму по себе нельзя считать прочной. Так как:
- В местах с большей жесткостью и прочностью соединения возникает большая концентрация сил, оказывающих действие на всю конструкцию в целом.
- Где меньше жесткости, там и меньшее количество действующих сил.
Таким образом, при наличии в металлической конструкции местной непрочности даже самый надежно проваренный стык может представлять опасность. Поэтому надо не допускать местных непрочностей. Плохая сварка даже в самых незначительных участках может привести в негодность всю конструкцию.
Рекомендуем статьи по металлообработке
- Термическая резка металла: оптимальные способы обработки
- Сквозное сверление: технология и правила
- Окраска металлических изделий: технологии и этапы процесса
Правильная сварка является важнейшим фактором обеспечения надежности и безопасности металлоконструкции.
Требования и виды качества сварных соединений
При сварке швов используемый металл должен отвечать ряду требований. Вот главные из них:
- величина относительного удлинения материала – от 16 % и выше;
- ударная вязкость металла – выше 24 Дж/см2, это значение замеряется при среднесуточной температуре воздуха в самый холодный пятидневный период;
- способность металла сварных соединений и швов металлических конструкций к временному сопротивлению разрыву должна быть такой же (или более высокой), как и у главного металла, из которого сделаны свариваемые изделия;
- при сварке металлических изделий на заводе важно, чтобы коэффициент твердости металла шовного соединения был до 350 HV у металлоконструкций 1-й группы и менее 400 HV у изделий иных групп, описанных в СНиП II-23-81;
- при сварке во время монтажа и сборки конструкций коэффициент твердости шовного металла должен быть не выше 400 HV.
Выполнение необходимых правил и осуществление контроля сварных швов металлических конструкций поможет сохранить целостность и сохранность сварных соединений, избежать ранней потери прочности и аварийного разрушения металлоизделий.
По качеству шовные соединения разделяют на три категории:
В первую категорию входят шовные соединения, имеющие самые высокие эксплуатационные характеристики (прочность, долговечность, стойкость к разрывам и т. д.). К ним относятся следующие типы швов:
- поперечные стыковые соединения, подверженные сильным растягивающим напряжениям;
- нахлесточные, тавровые и угловые шовные соединения, работающие на отрыв при растягивающих напряжениях;
- швы в металлоизделиях, отнесенных согласно СНиП II-23-81 к 1-й группе (или ко 2-й группе, если температура воздуха, где возведена металлоконструкция, опускается ниже отметки -45 °С).
Во вторую категорию входят швы среднего качества. К ним относятся:
- продольные стыковые элементы, подверженные напряжению сдвига;
- связующие угловые швы в металлических изделиях 2-й и 3-й группы, на которые действуют растягивающие напряжения;
- швы в углах и стыках, соединяющие фасонки со сжатыми элементами металлических изделий.
В третью категорию входят швы низкого качества, среди которых:
- поперечные швы в стыках, на которые действуют сжимающие напряжения;
- продольные соединения в стыках, а также связующие швы в углах, которые применяются в сжатых частях конструкций;
- соединения в стыках и углах, использующиеся во вспомогательных деталях металлических изделий.
6 методов контроля качества сварных соединений металлоконструкций
- Визуальный контроль.
Этот способ является самым простым и наиболее быстрым, не требует никакой специальной техники, нужна только внимательность.
Посмотрите: шов должен быть одинаковой ширины и высоты на всех участках без видимых трещин и повреждений. Внешний контроль соединений металлоконструкций выявляет, есть или нет непроваров, наплывов, неравномерных складок шва. Наличие этих дефектов указывает на низкое качество соединения.
Разумеется, данный способ не гарантирует полного контроля сварных швов трубопроводов, сварных соединений газопроводов или иных ответственных конструкций, но может стать первой операцией перед применением остальных методов контроля.
- Капиллярный контроль.
Этот метод служит для испытания сварного шва. При его применении используют специальные жидкости, которые могут проникнуть в «капилляры» – поры и трещины шва.
Этот способ хорошо подходит для проверки металла с любой формой и составом. Он помогает раскрыть дефекты, невидимые для глаз, и при этом экономичен, так как не требует дорогого оборудования.
Для капиллярного контроля швов используются жидкости – пенетранты (от англ.«penetrant», означающее «проникающая жидкость»). За счет незначительного поверхностного натяжения такие жидкости беспрепятственно попадают в мелкие капилляры, оставаясь видимыми для глаз. Попадая в полости, пенетранты маркируют дефекты.
- Контроль сварных швов на герметичность.
Очень важно проверить швы на герметичность. У данного способа проверки на герметичность много названий: течеискание, пузырьковый метод контроля, пневмоиспытание, гидроиспытание и др. Однако суть всегда одна и та же: выявление сквозных дефектов, ухудшающих герметичные показатели сварного шва.
Для проверки сварных соединений на герметичность применяются газы (кислород или азот), разные жидкости (например, вода). При всей схожести данного метода с капиллярным газ или жидкость под давлением попадают в дефектные проемы. Этот метод разделяют на пневматический и гидравлический контроль, кроме того, соединения могут быть проверены посредством вакуума или обдувом воздухом – это подкатегории пневматического контроля.
- Магнитный контроль.
В его основе лежат главные принципы электромагнетизма. Контролер со сварщиком, используя специальный прибор, окружают сварное соединение магнитным полем, использующим поток электромагнитных линий. Их искажение указывает на наличие дефектов.
- Ультразвуковой контроль.
Этот очень интересный способ основан на свойствах ультразвука. Края трещин и сколов, имея разные акустические способности, очень хорошо отражают звуковые волны. Проще говоря, если при подаче на шов ультразвука он искажается и отражается в другом направлении, значит, есть дефект. Различные виды изъянов по-разному искажают звуковую волну, что помогает легко их определить.
- Радиационный контроль.
Иначе его называют радиографический контроль и гаммаграфический контроль сварных соединений. Он представляет собой мини-рентген.
Гамма-лучи, проходя сквозь металл, на специальной пленке отображают все выявленные незамеченные дефекты. Данный способ контроля является самым современным и дорогостоящим, требует высокого профессионализма контролера и сварщика. Долгая работа с таким устройством может быть вредна для здоровья.
Оформление документации на сварные соединения металлоконструкций
По результатам испытаний составляется акт дефектов сварных соединений. Фиксируют каждый изъян и дают его краткое описание. Результаты вносят в журнал сварки. Такая документация ведется бригадой на всех объектах. Спецжурнал – это первичный документ, который ведется в соответствии со СНиП по каждому узлу конструкции.
По завершении работ журнал вместе с остальной документацией передается заказчику.
Кроме спецжурнала, во время сварных работ делают схему стыков с полным описанием технологии. Их дополняют сертификатами на используемые материалы (электроды, флюс или присадочную проволоку). Акты исследований сварных швов (контроля качества швов с внешней стороны изделия), время приборной диагностики, ее результаты, заключения контролеров пишут индивидуально под каждого отдельного сварщика.
Эти документы нужны для предоставления в суд в случае аварии. Работа с ответственными конструкциями обременена серьезными требованиями. Объект не примут в готовом виде, если не будет предоставлен акт проверки швов.
В случае обнаружения дефекта соединение переваривается, даже если виноват не сварщик, а некачественный материал. Лишь после прохождения контроля производятся остальные действия по приему металлической конструкции объекта.
Читайте также
20.02.2023
Хонингование: как и для чего выполняется
Подробнее
17.02.2023
Полировка металла: технологии, инструменты, методы
Подробнее
15.02.2023
Для чего нужен гидравлический пресс: виды, сферы применения
Подробнее
14. 02.2023
Чем резать трубу: инструменты, способы, приемы
Подробнее
13.02.2023
Точечная сварка своими руками: как самостоятельно собрать аппарат
Подробнее
10.02.2023
Сталь Ст3: характеристики и виды
Подробнее
08.02.2023
Постоянный ток (DC) для сварочных работ
Подробнее
07.02.2023
Особенности цветной металлургии: добыча и переработка
Подробнее
Металлографическая инспекция сварных швов | Struers.com
Struers – Обеспечение уверенности / Знание / Контроль сварных швов
Междисциплинарная задача
Проверка сварных швов — это междисциплинарная задача, охватывающая множество различных методов и целей. В этом разделе описывается исследование вырезанных срезов на геометрические особенности, твердость или микроструктуру.
Скачать инструкцию по применению сварных швов
- О
- Как
- Контакт
Проверка материалографических участков сварных соединений обычно проводится на двух уровнях контроля:
Макро:
При использовании стереомикроскопов с 50-кратным увеличением
Макроисследование обычно проводится на несмонтированных поперечных сечениях сварных соединений и включает методы резки и грубой/тонкой шлифовки. Полученная поверхность пригодна для травления с последующим изучением макроэлементов сварного соединения. Некоторые из них перечислены ниже:
- Геометрия сварного шва
- Количество и размер проходов
- Глубина проникновения
- Протяженность ЗТВ (зоны термического влияния)
- Поверхностные дефекты, такие как трещины, подрезы, чрезмерная щель, выпуклость и угол сгиба сварного шва
- Внутренние дефекты, такие как трещины, пористость, металлические включения, несплавление, непровар и шлак
- Дефекты геометрии соединения, такие как зазор корня, поверхность корня, угол фаски и несоосность
Микро:
При исследовании с большим увеличением (до 1000 раз) с использованием оптических микроскопов
Для методов микроисследования и определения твердости требуется полированная, оптически плоская поверхность. Микроисследование проводится для изучения дефектов сварных швов и особенностей микроструктуры, таких как:
- Пустоты (пористость, усадочные раковины, микротрещины)
- Специальные фазы (сигма-фаза в нержавеющей стали)
- Размер зерна/структура
- Сварная конструкция
- Сегрегация
- ЗТВ и базовая конструкция
Как проводить контроль сварных швов
В общем, традиционные методы материалографии и проверки твердости также применимы к участкам сварных швов.
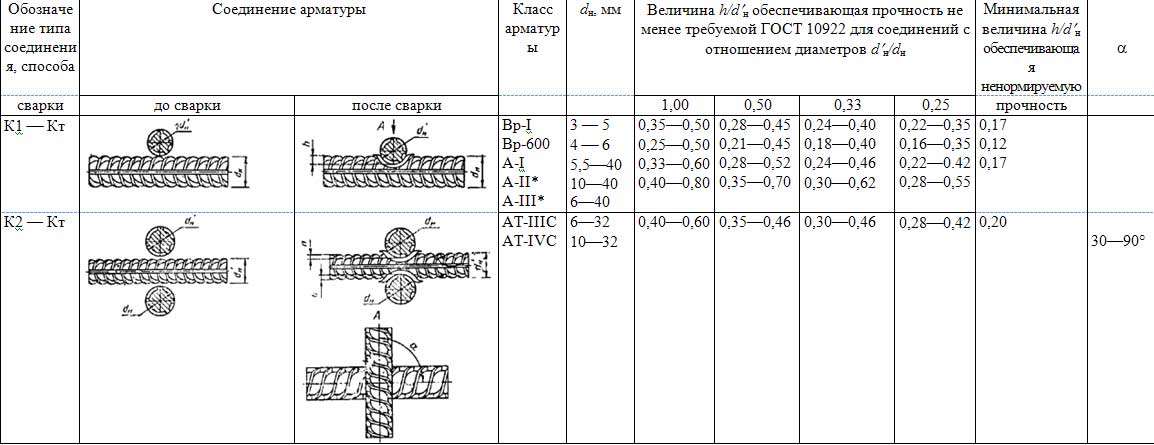
Резка
Часто газопламенная резка используется в качестве основного метода резки для удаления сварной секции, которую легче обрабатывать, из более крупного изделия. В этом случае важно, чтобы макро-/микросрезы были вырезаны с помощью процесса абразивной мокрой резки и чтобы срезы были удалены от влияния любого термического повреждения от первичной операции термической резки.
Чтобы свести к минимуму деформацию при резании и риск термического повреждения поверхности реза, применяются общие рекомендации по выбору отрезного круга и параметров резки.
Монтаж
Обычно макросрезы для процедурных испытаний изготавливают в разобранном виде из-за нехватки времени, а также потому, что для макроисследования обычно достаточно тонкой шлифовки. Если возможна полуавтоматическая подготовка, то имеется ряд держателей образцов, которые подходят для несмонтированных поперечных сечений сварных соединений.
Если требуется монтаж, существует возможность горячего монтажа или холодного монтажа. Однако при контроле сварных швов нередко встречаются относительно большие поперечные сечения. В этом случае можно использовать прямоугольные формы для холодного монтажа.
Механическая подготовка
Традиционно сварные срезы для макроконтроля подготавливаются вручную на последовательно более тонких сортах карбидокремниевой бумаги до зернистости 1200. Для больших образцов или длительного времени шлифования алмазный диск со связкой из смолы может предложить некоторые преимущества с точки зрения срока службы и постоянной скорости съема.
Требования к подготовке для микроконтроля и определения твердости также включают полировку.
Образцы сварных швов могут иметь большие различия в твердости материала по всему образцу либо из-за фазовых переходов во время сварки, либо из-за того, что соединение включает разнородные металлы. Металл сварного шва может содержать твердые выделения или какой-либо собственный дефект сварного шва. Поэтому важно, чтобы метод препарирования обеспечивал минимальную полированность рельефа между элементами микроструктуры и сохранение всех элементов микроструктуры. В этом отношении предпочтительно использовать полуавтоматическое или автоматическое оборудование для подготовки, поскольку оно обеспечивает постоянство и воспроизводимость полировки, что облегчает точный микроструктурный анализ.
Травление
В зависимости от сплава и требуемого анализа можно использовать как химическое, так и электролитическое травление. Наиболее распространенным травителем, используемым для углеродистой и низколегированной стали, является нитал различной концентрации; в качестве альтернативы можно использовать десятипроцентный персульфат аммония. Для сложных сплавов, таких как нержавеющие стали и никелевые сплавы, следует рассмотреть возможность электролитического травления. Электролитическое травление предлагает некоторые преимущества по сравнению с решениями для химического травления, такие как скорость, простота в эксплуатации и повышенная безопасность благодаря сведению к минимуму контакта пользователя с травителями.
Для применений, требующих подробного микроструктурного анализа, образцы для электролитической полировки и травления должны быть отшлифованы до зернистости 1000.
Геометрические элементы
Геометрические элементы сварного шва обычно задаются индивидуально для каждого сварного шва или группы сварных швов. Поэтому анализ отказов, одобрение или контроль сварного шва в большинстве случаев выполняются в соответствии с подробной спецификацией. Тип, количество и размер внутренних или поверхностных дефектов также хорошо определены для качества сварного шва.
Измерение, подсчет, индикация и отчетность по геометрическим характеристикам и дефектам сварных швов обусловлены высокой степенью стандартизации, поскольку задача может быть оптимизирована за счет использования специальных систем визуализации.
Ищете расходные материалы?
Закажите расходные материалы непосредственно в нашем интернет-магазине.
Перейти к расходным материалам в интернет-магазине
Хелле Михаэльсен
Глобальное бизнес-решение и диспетчер приложений
Struers Aps.
Баллеруп, Дания
Контакт
Биргитте Нильсен
Металлограф,
Специалист по применению
Struers Aps.
Баллеруп, Дания
Контакт
Мария Линдегрен
Кандидат наук. в области обработки металлов давлением,
Специалист по применению
Struers Aps.
Баллеруп, Дания
Контакт
Олафур Олафссон
Кандидат технических наук, инженер-механик,
Специалист по применению
Struers Aps.
Баллеруп, Дания
Контакт
Фарук Музафер
Специалист по применению
Struers ApS
Ballerup, Дания
Контакт
Мэтью Кодуэлл
Руководитель лаборатории
Struers Ltd.
Rotherham, UK
Контакт
Хольгер Шнарр
Степень доктора технических наук и степень инженера в области материаловедения,
Специалист по применению
Struers GmbH
Виллих, Германия
Контакт
Ульрих Зетцер
Инженер-материаловед, степень технического ассистента по металлографии и материаловедению,
Специалист по применению
Struers GmbH
Willich, Германия
Контакт
Римский герундий
Степень технического ассистента по металлографии и материаловедению,
Специалист по применению
Struers GmbH
Willich, Германия
Контакт
Кэролайн Муссу
Руководитель лаборатории
Struers SAS
Шампиньи-сюр-Марн, Франция
Контакт
Кристиан Вегерски
Специалист по применению
Struers GmbH
Виллих, Германия
Контакт
Марко Карузо
Металлограф,
Специалист по применению
Struers S. A.S.
Арезе, Италия
Контакт
Генри Удомон
Менеджер приложений
Struers Inc.
Кливленд, Огайо, США
Контакт
Келси Торболи
Инженер по приложениям
Struers Inc.
Кливленд, Огайо, США
Контакт
Брайан Джонс
Инженер по применению
Struers Inc.
Кливленд, Огайо, США
Контакт
Эллис Перри
Инженер по применению
Struers Inc.
Кливленд, Огайо, США
Контакт
Сюпин Цзян
к.т.н., магистр наук. в области материаловедения и инженерии,
Менеджер по применению и лаборатории
Struers Ltd.
Шанхай, Китай
Контакт
Райан Яо
Специалист по применению
Struers Ltd
Шанхай, Китай
Контакт
Киничи Исикава
г-жа К. Кандидат промышленных наук,
Специалист по применению
Struers K. K.
Токио, Япония
Контакт
Юя Хаякава
Магистр наук в области материаловедения и инженерии,
Специалист по применению
Struers K.K
Токио, Япония
Контакт
Кенни Лим
Специалист по применению
Struers Singapore
Сингапур, Сингапур
Контакт
Как удалить сварку
Пьера Янга
Если вы когда-нибудь занимались сваркой, то знаете, что это процесс сплавления металлов с помощью электричества. Сварка применяется практически во всех отраслях промышленности для создания сложных конструкций и каркасов из металлов.
Однако, если вы хотите добиться успеха в своих проектах, вам нужно знать не только сварку, но и ее разъединение.
Это может быть по любой причине. Может ты перепутал. Возможно, вам нужно разобрать ранее сваренную деталь для другого проекта.
Как удалить сварку? Удаление сварки зависит от многих вещей. Поскольку существуют разные типы сварки, существуют разные требования к расшивке сварного шва.
Как правило, сварку можно удалить с помощью плазменной резки, газовой резки, шлифовальной или дисковой пилы, дрели или кислородно-ацетиленовой горелки.
Поскольку сварка создает прочную связь между двумя металлами, эта связь обычно оказывается прочнее, чем сами металлы, а это означает, что вы не можете разорвать сварной шов так же легко, как сломать кусок металла — например, с помощью молоток.
Ошибки естественны и ожидаемы, и если вы только начинаете, то очень высока вероятность того, что вы допустите ошибки в своих проектах. В большинстве случаев, чтобы исправить эти ошибки, нужно уметь разводить сварные швы.
Есть несколько способов сделать это, помимо приложения большой силы к сварному шву. Процесс удаления сварных швов зависит от типа сварного шва, который вы хотите отменить.
И в зависимости от этого вам нужно будет решить, хотите ли вы отменить это механически или термически.
Вот несколько советов, как удалить сварку:
Термические методы
Слово «терм» в переводе с греческого означает тепло, поэтому «термальный» относится ко всему, что связано с теплом.
Таким образом, как следует из названия, термические методы требуют использования высокой температуры для рассоединения сварных швов. Обычно это делается с помощью кислородно-ацетиленовых горелок или плазменных резаков.
Плазменная резка
Плазменная резка — это процесс разрезания электрических проводников с помощью ускоренной струи горячей плазмы. Вот видео о плазменной резке для начинающих:
С помощью постоянного тока можно создать дугу, температура которой может достигать 20 000 градусов Цельсия. Тепло генерируется потоком воздуха под высоким давлением, выходящим из небольшого сопла.
Плазменная резка может быть выгодна с точки зрения скорости резки, поскольку они примерно в пять раз быстрее, чем ручные резаки, и могут резать широкий спектр материалов различной толщины, поэтому любые глубокие сварные швы также могут быть удалены. Они просты в использовании и не используют горючие газы, поэтому они безопаснее и даже экономичнее, чем гидроабразивная и лазерная резка.
Резка горелкой
Ацетиленовые горелки сочетают ацетилен с кислородом для получения пламени при очень высоких температурах (около 3500 градусов Цельсия) для резки или сварки металлов.
Этот метод немного опаснее, особенно для новичков. В факеле используется смесь двух газов, которые смешиваются с помощью резака и создают достаточно горячее пламя, чтобы прорезать очень толстые куски металла.
Все, что вам нужно сделать, это отметить линию, где вы хотите выполнить разрез, зажечь горелку и точно настроить дугу, прежде чем медленно следовать по линии, пока не прорежете ее полностью.
Резка факелом может быть выгодна тем, что она проста в использовании и не занимает слишком много времени. Это оборудование также дешевле, более портативно и может использоваться как для сварки, так и для резки более крупных и различных металлов.
Вот видео о том, как резать горелкой:
Механические методы
В термических процессах вы использовали тепло, чтобы пройти через процесс резки. В механических процессах вы выполняете рез вручную.
Существует несколько методов, которые вы можете использовать в зависимости от типа сварного шва, с которым вы имеете дело. Например, листы, сваренные точечной сваркой, трудно отделить, и вам часто приходится выполнять процесс разделения путем сверления отверстий в самих листах.
Иногда разделение металлов невозможно без повреждения основных металлов. Механические процессы обычно включают резку, шлифовку или сверление.
Удаление сварных швов без использования шлифовальных машин
Если вы хотите разделить сварные швы без использования шлифовальных машин, вы можете либо сверлить, либо использовать плазменную и кислородно-ацетиленовую горелки в качестве термического реверсивного процесса. Вы также можете выйти за рамки обычного и использовать ленточнопильный станок или ножовку.
Необходимые шаги:
- Сначала вы отмечаете металл в том месте, где хотите сделать разрез. Для этого не нужны никакие специальные инструменты, и это можно быстро сделать с помощью обычного карандаша или маркера.
- Затем вы держите металлические детали на месте и закрепляете их, чтобы они не двигались. Обычно это делают струбцинами или тисками.
- При использовании газовой горелки необходимо открыть газовый баллон. Если вы используете плазменный резак, вам придется подключить шнур питания и включить резак. Включите компрессор и убедитесь, что машина подключена. Затем отрегулируйте пламя факела.
- Переместите свой инструмент — фонарик, пилу или что-то еще — вдоль линии, которую вы нарисовали ручкой/маркером на первом этапе. Делайте это медленно, чтобы избежать ошибок и в целях безопасности. Старайтесь не задерживаться слишком долго на одном и том же месте. Продолжайте делать это, пока не сделаете успешный разрез.
- После того, как вы выключили инструменты, оставьте металлы и дайте им остыть, прежде чем прикасаться к ним. Используемые вами станки выделяют много тепла, и обращение с металлами сразу после резки может быть очень опасным.
Удаление сварных швов с помощью шлифовальной машины или циркулярной пилы
После сварки валик сварного шва обычно стачивают с помощью угловой шлифовальной машины. Их можно использовать для создания скошенных кромок или подготовки металлических поверхностей, а также для их резки.
Хотя разрезы, сделанные с помощью шлифовальных станков, не так точны, как плазменная резка, они дешевле, и, поскольку они не производят столько тепла, окружающий основной металл не достигает температуры, достаточно высокой, чтобы изменить его свойства.
Шаги:
- Маркером отметьте место, где вы хотите сделать надрез.
- Закрепите деталь, которую хотите отрезать, с помощью тисков или зажимов.
- Наденьте защитное снаряжение.
- Подключите ваш инструмент — шлифовальную машину или пилу — к электрической розетке.
- Медленно дайте шлифовальному станку начать резать металл. Не прижимайте его слишком сильно к основным металлам. Пусть работает. Если надавить слишком сильно, можно столкнуться с проблемой поломки отрезного диска, что очень опасно.
- Отключите питание и дайте металлу остыть. Это тепло возникает из-за трения, а не из-за шлифовального станка, в отличие от плазменной или газовой резки.
Какой процесс лучше для вас?
Чтобы решить, какой процесс лучше подходит для рассоединения сварного шва, необходимо определить тип используемого основного металла. Если сварные швы очень прочные или если вы хотите разъединить листы, соединенные вместе, вам, возможно, придется просверлить или отшлифовать их.
Часто в результате сварки одна из деталей повреждается. Это может быть из-за присадочных металлов, но это легко исправить болгаркой или напильником по металлу.
После резки сварного шва часто приходится шлифовать валик, чтобы снова сварить детали. Сошлифовка лишнего металла позволяет в следующий раз получить более качественный валик, в отличие от сварки металлов без удаления лишнего.
Смежные вопросы
Что вызывает плохую сварку?
Плохая сварка может быть результатом многих причин. Либо воздух мог проникнуть в сварной шов, что вызвало пористость, либо нагрев может вызвать растрескивание. Иногда проблема может усугубляться неправильными методами сварки.
Можно ли сваривать шов?
Сварка поверх сварных швов очень распространена, хотя есть некоторые опасения.
Различия в процедурах сварки сварных швов внахлестку, такие как тепловложение или скорость охлаждения двух металлов, могут вызвать проблемы. Композиционные вариации также могут привести к проблемам.