Опрессовка и вакуумирование – ООО “ХолодПромСервис”
Опрессовка азотом систем кондиционирования и холодоснабжения. Проверка на герметичность.
Инструмент для опрессовки азотом систем кондиционирования и водоснабжения.
Чтобы убедиться в герметичности смонтированных трубопроводов и аппаратов холодильной системы, проводится процедура испытания избыточным давлением – так называемая опрессовка азотом.
Для опрессовки применяется азот в баллонах емкостью 5, 10 и 40 литров, причем обязательно с минимальным содержанием примесей и влаги: особой чистоты 99,999% 1 сорта. Баллон с азотом находящимся под давлением 150 бар и выше, подключается к сервисному порту холодильного аппарата через понижающий редуктор высокого давления с предохранительным клапаном настроенным на давление срабатывания 70 бар, как правило используется специальный переходник для опрессовки азотом, чтобы опрессовка проходила через обычный кондиционерный шланг с резьбой ¼ дюйма.
Для облегчения процесса опрессовки и поиска утечки на фото ниже представлен азотный набор STDL – 70, который включает в себя азотный редуктор, переходник с резьбой ¼ дюйма, запоминающий манометр со шлангом, переходник на малый баллон, муфта с резьбой ¼ дюйма.
При изменении внешних условий допускается для быстрой оценки применять коэффициент коррекции 0,1 бар на 1°С изменения температуры. Т.е. корректирующее значение давление будет равно: (Т°С во время подачи давления – Т°С во время проверки) х 0,1.
Приближенно 0,1 МПа = 1 Атм = 1 бар
В случае применения цифровой манометрической станции, возможно значительно сократить время опрессовки до приемлемого интервала.
Для учета изменения параметров, необходимо скорректировать полученные значения в соответствии с законом Шарля:
При этом значения температур и давлений должны быть выражены в абсолютных величинах.
Пример.
За время испытаний по показаниям приборов давление в системе понизилось с 39 до 38 бар, при этом температура окружающего воздуха изменилась с 25°С до 19°С.
1. Рссчитаем значения температур в Кельвинах и абс. величины давлений:
T1 = 273 + 25 = 298 °K T2 = 273 + 19 = 292 °K
P1=39+1=40 бар P2=38+1=39 бар
2. Вычислим значение давления в барах в конечный момент времени P2, при котором будет сохраняться тождественность формулы (1):
3. Сравним измеренное значение с расчетным:
P2 изм.= 39 бар Р2 расч.≈ 39,19 бар
Значения примерно равны, различия скорее всего вызваны погрешностью измерительных приборов, но также не исключаются нарушения герметичности, вызванные, например, наличием пористости в паяных соединениях или недостаточной жесткостью трубопроводов.
Вывод: Контур герметичен, но требует контроля.
В случае если обнаружено снижение давление после коррекции по температуре, следует внимательно проверить все потенциально слабые места системы: разъемные и паяные соединения, заглушки, вальцовки и т.п. Самые крупные течи выявляются на слух и на ощупь. Еще один доступный способ поиска утечек – обмыливание, появление пузырей явно указывает на источник негерметичности. Также можно в контур с азотом добавить небольшое количество хладагента, после чего выполнить поиск электронным течеискателем (здесь есть определенные нюансы, связанные с сепарацией разнородных газов). Длинные трассы и большие системы рекомендуется по возможности разбивать на секции для облегчения поиска и устранения негерметичности.
Обязательно учтите, что данный вид работ должен выполняться только квалифицированными специалистами, прошедшими соответствующую подготовку.
После завершения всех процедур азот удаляют из системы и проводят вакуумирование.
Вакуумирование трассы кондиционера
Вакуумирование холодильного контура производится с целью удаления воздуха, неконденсируемых примесей, а также для понижения содержания влаги во фреоновых магистралях.
Для удаления влаги, необходимо чтобы вода перешла из жидкого состояния в газообразное. При нормальном атмосферном давлении 760 мм рс. (прим. 100 кПа) вода закипает при 100°С, соответственно для удаления влаги при таких условиях необходимо было нагреть воду до этой температуры, что не представляется возможным по причине возможного выхода из строя деталей оборудования. В реальных условиях для этих целей понижают давление в контуре до требуемой величины, при которой кипение воды происходит при значительно более низкой температуре. Например, при давлении около 4,6 мм р.с.(прим. 600 Па), вода кипит уже при t=0°С. Отметим, что таким образом можно удалить только относительно небольшое количество влаги, в других случаях обязательно применение фильтров-осушителей, а также проведение дополнительных процедур.
Время вакуумирования системы зависит от внутреннего объема холодильного контура, производительности вакуумного насоса, температуры окружающей среды и количества влаги в контуре. Чем ниже температура на улице, тем более глубокий вакуум необходимо создать. Как правило, при монтаже нового оборудования с использованием качественных комплектующих и соблюдении рекомендаций производителя, время вакуумирования бытовых систем кондиционирования с применением цифровых станций не превышает 30 минут. Тот же процесс для достижения необходимой глубины вакуума полупромышленных и промышленных систем кондиционирования может составлять более двух часов. Прибор для проверки глубины вакуума представлен ниже.
Манометрическая станция Цифровая манометрическая станция с возможностью одновременного измерения двух температур и давления
Вакуумирование является обязательной процедурой, особенно при монтаже оборудования, работающего на новых типах хладагентов, таких как многокомпонентный R410A. Применяемое в таких системах полиэфирное масло чрезвычайно гигроскопично (быстро поглощает влагу из окружающей среды), при взаимодействии с воздухом его компоненты превращаются в кислоту, которая разрушает детали компрессора, что приводит к преждевременному выходу оборудования из строя.
Ниже на схеме представлен вариант подключения вакуумного насоса через манометрический коллектор:
Схема подключения вакуумного насоса к системе
Общий порядок действий таков:
1. Подключаем манометрическую станцию через шланг низкого давления (обычно синего цвета) к сервисному порту кондиционера.
2. Подключаем вакуумный насос через заправочный шланг (обычно желтый) к станции.
3. Включаем вакуумный насос и открываем вентиль низкого давления на станции.
4. После окончания процесса сначала обязательно закрываем вентиль и только после этого выключаем насос.
5. Проверяем величину давления.
Оборудование для проведения вакуумирования кондиционера:
Станция в работе Высокопроизводительный вакуумный насос фирмы CPS США с подключенной цифровой станцией в рабочем режиме.
Вакуумный насос, штуцер вакуумного насоса
Также очень сильно помогает в работе такой, казалось бы на первый взгляд, необязательный элемент как запорный вентиль, помогающий специалисту отсоединить шланги от системы практически без потери давления. Данное уст-во выпускается под различные типоразмеры сервисных портов кондиционера, как для оборудования на R-410A, так и для R-22 и может составлять как единое целое со шлангом, так и отдельную единицу.
holodps.ru
Вакуумирование и проверка кондиционера
В итоге, после всех этапов установки сплит-системы нам остаётся запустить фреон в кондиционер и проверить его работу.
Вакуумирование холодильного контура
Внешний блок кондиционера идёт с завода заправленным, то есть в нём находится фреон в необходимом количестве. Не дают ему выйти наружу закрытые трёхходовые клапаны.
После монтажа у нас получается система состоящая из внутреннего блока и соединительных трубок, заполненных атмосферным воздухом с содержащимися в нём примесями и влагой.
Для нормальной работы нам необходимо удалить воздух и влагу из системы, после чего открыть вентили, запустив фреон.
Процесс вакуумирования
- Подсоединяем манометрический коллектор к вентилю на кондиционере (шланг низкого давления-синий)
- Подсоединяем заправочный шланг к вакуумному насосу (жёлтый)
- Открываем вентиль низкого давления
- Включаем вакуумный насос
- После окончания процесса закрываем вентиль на манометрическом коллекторе
- Запускаем фреон в контур открывая вентили на кондиционере шестигранником (оба)
Время вакуумирования
Для контроля степени разрежённости в системе существует прибор – вакууметр, шкала которого проградуирована в мБар – хорошие вакуумники изначально комплектуются вакууметрами, но можно использовать и отдельные, например электронные.
Некоторые монтажники ориентируются по давлению манометра – как только давление падает ниже нуля, они прекращают вакуумирование, считая что воздух удалился и можно прекращать процесс.
Но это не правильно. В любом воздухе содержится влага – при вакуумировании она испаряется, поэтому для кондиционеров 7 Btu/h время вакуумации не должно быть меньше 15 минут (зависит от производительности самого насоса), для более мощных систем, соответственно больше.
Выбор вакуумного насоса
Для разных целей необходимо выбирать разное оборудовафние, к примеру для монтажа бытовых кондиционеров понадобится насос с небольшой производительностью, которого вполне хватит для небольшой трассы. А при установке промышленных, VRV систем уже необходимы насосы с высокой производительностью и мощностью.
Характеристики на которые необходимо обратить внимание при подборе и покупке вакууматора:
- Производительность, л/ч
- Остаточное давление, Па
- Мощность двигателя, Вт
От производительности зависит скорость откачки из холодильной системы, указывается в литрах в час.
Остаточное давление характеризует “качество вакуумации”, чем меньше это значение, тем лучше, измеряется в Паскалях или мили Барах.
От мощности электродвигателя зависит время непрерывной работы насоса, при длинных трассах в ВРВ системах этот параметр имеет большое значение.
Это самые основные параметры, существует ещё ряд параметров, такие как, количество ступеней, тип насоса – масляный, безмасляный, количество оборотов двигателя и прочие.
“Продувка фреоном”
Многие монтажники практикуют такую процедуру – выгоняют воздух открыв вентиль и открутив одну из гаек, из под неё выходит воздух,после чего её закручивают.
После такого монтажа влага остаётся в системе,последствия этого – окисление медных трубок, повреждение компрессора, забивание ТРВ влагой. А самое главное – значительное сокращение срока службы, таким образом можно загубить любой кондиционер, даже самый дорогой.
Дозаправка фреоном
Кондиционер заправлен на заводе хладагентом в расчёте на длину трассы приблизительно до 5 метров, при большей длине его придётся дозаправлять.
Точное количество указано в инструкции по монтажу и составляет около 5-20 грамм на метр дополнительной трассы, в зависимости от мощности кондиционера.
Необходимо высчитать количество недостающего фреона и заправить его методом “по массе”.
В противном случае будет потеря холодильной мощности.
Проверка кондиционера
После запуска фреона в контур включаем кондиционер на охлаждение и измеряем температуру на выходе – она должна быть не ниже 0 0С.
Если температура ниже нуля, это говорит о недостаче фреона, который необходимо добавить (естественно, это при соблюдении рабочего температурного диапазона на улице конкретно для данного кондиционера).
После можно включить кондиционер в режим обогрева и проверить его работоспособность в этом режиме.
Проверка дренажа
- Открываем крышку внутреннего блока
- Снимаем фильтры
- Аккуратно наливаем воду из бутылки в поддон кондиционера (можно лить прям на испаритель)
- Убеждаемся что вода свободно выливается из дренажного шланга на улицу
Вот и всё, мы завершили установку кондиционера!
Осталось только рассмотреть некоторые нюансы – вальцевание и пайку трубок, удаление конденсата дренажной помпой, установку защитных электрических устройств.
masterxoloda.ru
Вакуумирование кондиционера (инструкция)
Вакуумирование кондиционера – это важный процесс, который обуславливает безотказную и долговечную работу устройства. Как известно, по окончании монтажа в сплит-системе находятся остатки воздуха и влаги, которые требуется удалить.
Подготовка сплит-системы к работе
Во время установки кондиционера его оба блока, внешний и внутренний соединяются между собой двумя медными трубами, которые образуют систему для циркуляции хладагента в холодильном контуре системы.
По окончании монтажа фреоновой трассы, то есть труб, в системе находиться воздух и остаточная влага. При взаимодействии фреона с воздухов в трубах образуются, влияние которых оказывает пагубное воздействие на работу оборудования.
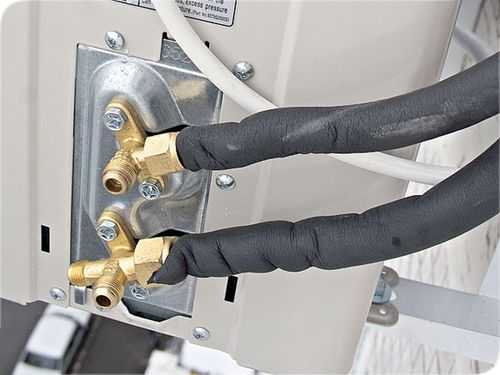
От правильного монтажа и вакуумирования трассы зависит долгий срок службы кондиционера
Осуществление пуско-наладочных работ
Для проведения качественных работ следует запастись специальными инструментами:
- Насосом для кондиционеров (вакуумным).
- Станцией со шлангами и манометрами.
- Баллоном с хладагентом, подходящим для сплит-системы.
- Набором ключей и отверток.
Подготовив все необходимые инструменты, рассмотрим боле подробно сам процесс. Первым делом необходимо осуществить подсоединение вакуумного насоса используя шланги коллектора манометрического к наружному крану кондиционера. Включаем насос для работы на 10-20 минут, в зависимости от мощности подключенного устройства. За это время насос должен выкачать все остатки воздуха и влаги изнутри и образовать глубокий вакуум.
Контроль за процессом вакуумирования осуществляется посредством снятия показаний с манометра. При достижении необходимого показателя в системе насос самостоятельно отключается, и продолжается наблюдение за внутренним состоянием системы.
Если в течении 30 минут внутреннее давление не изменяется, то процесс прошел удачно. В противном случае необходимо искать и ликвидировать утечку.
Причины возникновения утечек:
- Слабая или сильная затяжка гайки.
- Залом одной из медных трубок.
- Вальцевание низкого качества.
Удостоверившись в достижении вакуума можно приступать к следующему этапу – запуску фреона в систему. Для запуска фреона необходимо отсоединить насос и открыть фреоновые краны шестигранным ключом. В результате таких действий появляется шипение, свидетельствующее о заполнение фреоновым контуром оборудования.
По окончанию процесса оборудование можно считать полностью готовым к первому запуску. Во время проведения тестирования оборудования проверке подлежат все возможные режимы на соответствие их работы о заявленных характеристиках.
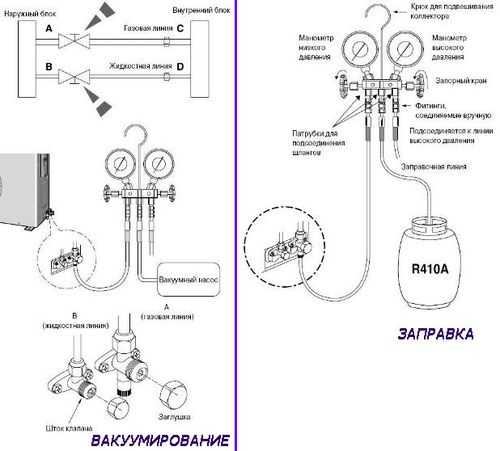
Схема соединений для вакуумирования и заправки кондиционера
Вакуумирование оборудования своими руками
Для того что б вакуумировать кондиционер самостоятельно требуется отсоединить один из шлангов коллектора на выбор с заправочным клапаном, а второй пользуясь вакуумным насосом для кондиционеров. По окончании подсоединений следует привести насос в действие и открыть кран на коллекторе. Таким образом, насос извлечет всю влагу, мелкие частицы и воздух из оборудования.
Проработав 20-30 минут, отключите систему и следите за стрелкой, которая стоит на 0 или 1. Если местоположение стрелки не изменилось, то система полностью герметична, в противном случае необходимо искать поломку.
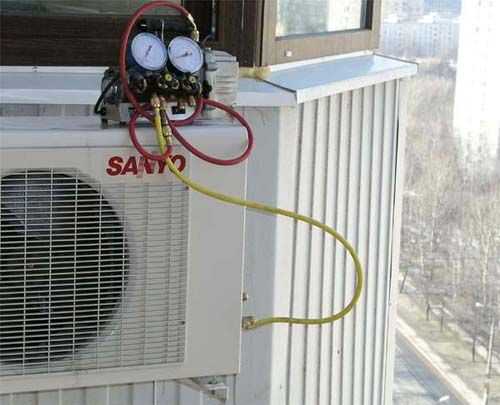
Очень важно соблюдать элементарные правила пользования кондиционером
Для обнаружения поломки в системе первым делом проверяем все соединения, используя мыльный раствор. По окончании проверки и регулировки системы в необходимых местах повторите все действия заново. Если повторная операция привела к тому же результату – необходимо исследовать вальцовку.
Самым больным местом прибора являются гайки (недотянутые или изрядно сорванные). В таком случае необходима заняться обратным процессом – перекачке фреона в кондиционер. Для этого следует подсоединить коллектор к клапану и запустить сплит-систему на холод и закрыть кран на тонкой трубе. Как только возникнет разряжение – закройте кран на толстой трубе.
По окончании работы необходимо провести все действия заново, начиная с устранения воздуха и жидкости в системе.
Если вы добились герметичности системы, то следующим этапом работы будет запуск фреона. Для этого следует открутить 2 клапана, толстой и тонкой трубы, используя шестигранный ключ. После отсоединения коллектора можно осуществить тестирование устройства и насладиться результатом стараний.
Как видим самостоятельное вакуумирование кондиционера — это вполне реальный процесс для простого человека.
Чего стоит остерегаться
Многие малограмотные специалисты, то ли по причине необразованности, толи из-за собственной лени, игнорируют вакуумирование сплит-системы, а вместо этого выгоняют часть фреона для вытеснения воздуха. Такие действия строго запрещены заводом. Так как могут привести к быстрой поломке и выходу из строя дорогостоящей системы.
Если у вас оборудование находиться на гарантии, то хорошо подумайте прежде чем самостоятельно лезть в систему. после постороннего вмешательства, мастера сервисного обслуживания снимают с себя всю ответственность.
klivent.biz
Вакуумирование кондиционера, проверка давления и дозаправка фреоном
Вакуумирование кондиционера (пуско-наладочные работы)
Вакуум-насос (вакууматор) |
При монтаже кондиционера наружный и внутренний блоки сплит-системы соединяются между собой двумя медными трубами. Это специальные холодильные трубки из сплава с высоким содержанием меди. Они предназначены для обеспечения циркуляции хладагента в холодильном контуре кондиционера. Не вдаваясь в подробности устройства холодильного цикла, этот процесс можно проиллюстрировать следующим образом:
Компрессор, находящийся в наружном блоке нагнетает горячий фреон в теплообменник наружного блока, где под высоким давлением хладагент конденсируется, отдавая тепло наружному воздуху. Для ускорения этого процесса теплообменник наружного блока (конденсатор) обдувается вентилятором. Полностью сконденсированный фреон в жидком состоянии по тонкой жидкостной трубе затем устремляется во внутренний блок. Но на пути он проходит через специальное устройство – термо-регулирующий вентиль (ТРВ) или реле протока. ТРВ предназначен для регулирования потока хладагента, который затем попадает во внутренний блок и для снижения давления фреона в жидкой фазе.
Таким образом, охлажденный фреон в жидком состоянии по тонкой медной трубе попадает в теплообменник внутреннего блока кондиционера. Не важно, о каком типе внутреннего блока идет речь (настенный, кассетный, канальный или любой другой) – процессы везде проходят совершенно одинаковые. Во внутреннем блоке жидкий фреон под низким давлением начинает интенсивно испаряться, кипеть. Теплообменник внутреннего блока поглощает тепло. Для того, чтобы сделать этот процесс более эффективным, а также для того, чтобы обеспечить распространение охлажденного воздуха по помещению, теплообменник обдувается вентилятором.
На выходе из внутреннего блока в толстую газовую трубу попадает полностью выкипевший хладагент в газообразном состоянии. По трубке он попадает обратно в наружный блок – в компрессор. Далее процесс повторяется.
Так в очень упрощенном виде работает любая холодильная установка. В том числе и бытовая сплит-система. Кстати обычный холодильник работает точно так же.
Именно эти два трубопровода – толстую и тонкую, и прокладывают монтажники сплит-системы при установке. К этим работам и материалам предъявляются высокие требования. Фреоновые трубопроводы из специализированной “чистой” меди, дороже трубопроводов для водяных систем отопления или ГВС. При работах в фреоновые трубопроводы не должна попадать пыль, песок или медная стружка. Места вальцованных соединений должны обеспечивать плотное и полностью герметичное соединение.
После того, как все трубопроводы в теплоизоляции проложены, закреплены и надежно соединены с кранами наружного блока и штуцерами внутреннего блока, на первый взгляд, систему можно запускать. Но не тут-то было. В соединительных межблочных трубопроводах и в трубках теплообменника внутреннего блока на этом этапе находится воздух. Ни в коем случае нельзя допустить того, чтобы в работающей системе хладагент смешивался с воздухом! Это приведет к существенному изменению характеристик фреона (масла), что в свою очередь приведет к ненормальной работе системы, в том числе снижению холодопроизводительности и обмерзанию отдельных частей контура, включая выход из строя компрессора.
Помимо этого, даже очень небольшое количество водяных паров, растворенных в воздухе, попавшем в контур, очень быстро растворяется в масле, смазывающем компрессор. Это ведет к ухудшению смазывающих свойств и повышенному износу компрессора. А компрессор это самый ответственный и дорогостоящий агрегат в кондиционере. Поэтому перед пуском смонтированной сплит-системы обязательно необходимо удалить весь воздух из соединительных межблочных трубопроводов и теплообменника внутреннего блока.
Для этого к сервисному порту на одном из кранов наружного блока через специальный манометрический коллектор подсоединяется вакуумный насос (вакууматор). Этот прибор в течении десяти-двадцати минут (продолжительность вакуумирования трассы зависит от мощности кондиционера, и протяженности соединительных трубопроводов) откачивает воздух из трассы, создавая в ней глубокий вакуум. Процесс наблюдается по манометрам на коллекторе.
После того, как необходимый вакуум достигнут, насос отключается, и еще в течение пятнадцати-тридцати минут монтажники наблюдают, не изменяется ли давление в системе. Неподвижная стрелка манометра показывает полную герметичность системы и всех произведенных соединений. В случае, если наблюдается падение вакуума, это означает, что где-то есть подсос воздуха. Тогда монтажники обязательно должны найти негерметичное место и устранить неисправность. Во время вакуумирования монтажникам, конечно, не приходится ждать, нервно поглядывая на стрелку манометра. Им есть чем заняться в это время. Это крепление трассы снаружи, подгонка крышек коробов, подвод питания и прочие оставшиеся этапы процедуры установки кондиционера. Только после того, как специалисты убедились, что в трассе нет воздуха и она полностью герметична, производится открытие кранов наружного блока, пуск фреона в систему.
Во время тестового запуска кондиционер включается во всех режимах, а специалисты следят, чтобы производительность сплит-системы соответствовала заявленным характеристикам.
Очень часто процедурой вакуумирования (или вакуумации) трассы пренебрегают и стравливают через систему часть хладагента, чтобы он вытеснил весь воздух из трассы. Потеря несущественной части фреона не сказывается негативно на последующей работе кондиционера, особенно, если длина трассы не превышает пяти-семи метров. Но опасность заключается в другом. Никто не знает, весь-ли воздух и влага вытеснены из трассы и теплообменника внутреннего блока. Влага в вакууме вскипает даже в порах меди и с воздухом удаляется из фреонового контура.
И хоть на первый взгляд при достаточной продувке трассы там не должно ничего остаться, практика показывает, что в основном впоследствии проблемы в работе возникают именно на тех монтажах, где вакуумированием пренебрегли. Самое неудобное в этом моменте заключается в неоднозначности симптомов – порой при диагностике таких неудачных объектов далеко не сразу удается выяснить причину неудовлетворительной работы системы. И исправление ситуации влечет за собой полную эвакуацию фреона из системы и заправку кондиционера новым хладагентом по весам. Эта процедура занимает довольно много времени и стоит недешево, особенно если система рассчитана на фреон марки R-410 (большинство современных кондиционеров).
Помимо прочего, вакуумирование системы и последующая опрессовка под вакуумом позволяет также достоверно убедиться в полной герметичности системы. Это практически полностью исключает вероятность утечки фреона в течение первых дней после монтажа. Кстати именно утечка в первые часы или дни работы системы является признаком некачественного монтажа, в частности вальцованных соединений трубопровода.
Утечка фреона опасна для компрессора
Дело в том, что при работе электродвигатель компрессора охлаждается потоком хладагента. Если кондиционер плохо охлаждает, первое, что обычно делает пользователь, это выставление еще более низкой температуры на пульте управление и попытки включить и выключить кондиционер. Такие попытки весьма вероятно приводят к сгоранию компрессора, что влечет за собой дорогостоящий ремонт. Но даже если компрессор не сгорел, неплотности в трассе приводят иногда к тому, что на стороне низкого давления происходит подсос воздуха в систему. А это уже описанные проблемы с влагой. Если впоследствии не производится полная эвакуация и заправка свежим фреоном, система будет работать нестабильно и скорее всего все равно выйдет из строя. При поломке компрессора производится экспертиза, которая показывает точную причину выхода его из строя. Или это брак, или работа кондиционера в условиях недопустимо низких наружных температур, или частые попытки пуска кондиционера, который потерял существенную часть или весь хладагент.
Все современные кондиционеры умеют сигнализировать о критически низком давлении. Но, к сожалению далеко не все при этом умеют самостоятельно выключаться. Поэтому пользователь должен осознавать свою ответственность при экспериментах. Ведь даже если фреон вышел по вине установщиков, многочисленные попытки запустить неработающий кондиционер приведут к негарантийной поломке. И дорогостоящий ремонт будет производиться за счет владельца. Поэтому очень важно не только выбрать ответственную фирму-установщика, но и впоследствии соблюдать элементарные правила пользования кондиционером, описанные в инструкции по эксплуатации, которая обязательно передается заказчику вместе с остальными документами при сдаче объекта.
Вакуумирование – это удаление неконденсирующихся примесей, воздуха, из труб и внутреннего блока. Влияние солнечных лучей, а так же воздух и влага, попадая в холодильный контур, плохо влияют на систему кондиционирования.
Во-первых, наличие воздуха в фреоновом контуре приведет к повышению давления в нем, увеличит нагрузку на компрессор, что приведёт к снижению холодопроизводительности кондиционера. Во-вторых, влага, всегда содержащаяся в воздухе, может привести к образованию кислоты в фреоновом контуре, снижению сопротивления изоляции электродвигателя компрессора и ее повреждению, химическому разложению хладагента, и как итог – выходу кондиционера из строя.
Вакуумирование выполняют с помощью специального вакуумного насоса, который позволяет убрать из холодильного контура воздух и водяные пары.
Для подключения вакуумного насоса к кондиционеру и контроля над процессом используют манометрический коллектор с набором шлангов. Можно использовать манометрический коллектор с двумя манометрами (высокого и низкого давления), но для вакуумирования лучше иметь коллектор с мановакууметром, который измеряет разрежение в контуре. Цена деления этого прибора 10 милибар, что позволяет проводить более тонкие измерения и следить за процессом вакуумирования. Шланги, манометры и вентили манометрического коллектора обычно имеют цветовую маркировку. Синий цвет – цвет стороны низкого давления, красный – стороны высокого давления, желтый – дополнительных устройств (зарядного цилиндра, вакуумного насоса, баллона с хладагентом и. т. п.), вентиль черного цвета обычно отключает или подключает мановакууметр.
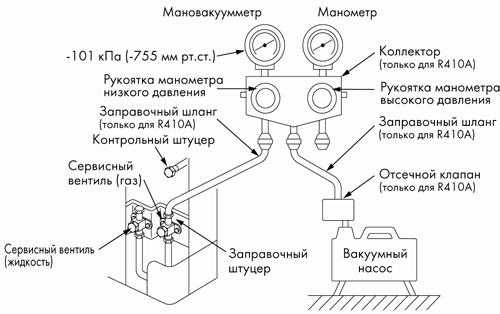
Подключение вакуумного насоса производят так:
Проверяют, закрыты ли все вентили на манометрическом коллекторе. Синий шланг подключают вначале к штуцеру манометрического коллектора, затем к штуцеру сервисного порта кондиционера. Отпирают синий вентиль манометрического коллектора и смотрят на стрелку синего манометра. Если давление равно атмосферному, то желтым шлангом подключают к коллектору вакуумный насос; если давление выше атмосферного, то предварительно стравливают избыточное давление, открыв желтый вентиль. Отпирают вентиль мановакууметра, желтый вентиль и включают вакуумный насос в работу в соответствии с инструкцией эксплуатации на насос.
Во время работы вакуумного насоса наблюдают за поведением стрелки мановакууметра. Она должна последовательно и без остановок приближаться к отметке «0». Когда стрелка достигнет отметки «0», нужно закрыть желтый вентиль, отключить насос и понаблюдать за «поведением» мановакууметра.
Возможные варианты:
- Стрелка отходит от нулевой отметки и движется в сторону отметки 1000 и достигает ее, это значит, что контур, который мы вакуумируем, негерметичный. Необходимо приостановить вакуумирование, найти и устранить место неплотности, после чего работы по вакуумированию можно продолжить.
- Стрелка отходит от нулевой отметки и останавливается, не достигая отметки 1000. Скорее всего, в контуре есть вода в жидком состоянии, пары которой и вызывают повышение давления. Чем быстрее и дальше отклоняется стрелка, тем больше воды в контуре. Предстоит работа по ее удалению.
- Стрелка остается на нулевой отметке в течение времени не менее 10-15 минут. Контур освобожден от воздуха и влаги, герметичен при проверке на вакуум.
Если негерметичность контура при вакуумировании не обнаружена, это вовсе еще не значит, что контур герметичен. Вальцовочные соединения под действием вакуума могут «присасываться» к штуцеру, не проявляя себя при проверке на вакуум, а при действии избыточного давления изнутри возможно возникновение утечки, поэтому после окончания вакуумирования желтый и черный вентили манометрического коллектора запирают и проверяют контур на отсутствие утечки под давлением.
Поиск утечек хладагента в незаправленной установке
Рассмотрим технологию поиска утечек, не очень распространённую и состоящую в том, что холодильный контур вакуумируется, после чего выдерживается некоторое время под вакуумом с контролем темпа роста давления в нем. Если вакуум в установке сохраняется, значит контур герметичен.
Чтобы дать заключение о надёжности такой технологии, сравним, что происходит при наличии негерметичности, например, в паяном соединении для двух счучаев (см. рис. 1).
С одной стороны (поз. 1) контур, находящийся под вакуумом, в котором в случае негерметичности наблюдается подъём давления. С другой стороны (поз. 2) контур, надутый азотом до давления 10 бар, в котором в случае негерметичности наблюдается падение давления.
Рис.1
Поз. 1. Контур находится под вакуумом. Поскольку наружное давление равно атмосферному, перепад давления на паяном соединении незначительный (меньше одного бара).
Следовательно, расход воздуха через негерметичный стык небольшой и поступающий внутрь контура воздух обеспечивает сравнительно медленный подъем давления.
Поз. 2. Контур надут азотом до давления в 10 бар. Перепад давления между контуром и окружающей средой в 10 раз больше, чем в предыдущем случае, и при отсутствии герметичности азот будет выходить из контура наружу. Следовательно, при одних и тех же размерах негерметичности, расход газа через негерметичный стык, во втором случае, будет гораздо быстрее, что позволяет гораздо легче обнаружить это с помощью манометра.
Заметим также, что в первом случае в контур поступает атмосферный воздух, содержащий влагу. Проникая внутрь, он нарушает одну из основных заповедей холодильщика: «Влага – враг холодильщика!», (напомним, что влага способна образовывать в соединениях с хладагентом особо разрушительные кислоты).
Наконец, чтобы покончить с обсуждением технологии поиска утечек путем вакуумирования контура, рассмотрим рис. 2., на котором изображено подключение развальцованной медной трубки к ниппельному наконечнику, представив себе, что гайка плохо закручена и, следовательно , должна приводить к негерметичности.
Рис. 2
Случай 1. Контур находится по вакуумом, наружное давление прижимает развальцовку к нипклю. Проход для воздуха ничтожный, негерметичность не обнаруживается.
Случай 2. Контур находится под давлением, которее отжимает фланец трубки от ниппеля. Утечка становится значительной и легко обнаруживается.
Из этого примера можно сделать окончательный вывод, что вакуумирование контура должно использоваться только для удаления из него влаги и ни в коем случае для испытания на герметичность.
Как же тогда проверить герметичность?
Наиболее надёжный способ заключается в наддуве контура исключительно сухим азотом (как правило, до давления 10 бар), таким образом, чтобы полностью исключить опасность конденсации (азот не конденсируется при нормальных температурах). Кроме того, наддув контура сухим азотом облегчит последующую процедуру осушки контура.
Внимание! Баллон с азотом следует подключить к контуру обязательно через редуктор во избежание серьезной аварии (давление в азотных баллонах свыше 100 бар).
При значительных утечках давление в контуре быстро падает и очень часто утечки можно обнаружить по звуку «на слух» (струя азота «свистит», вытекая из контура), а также проводя ладонью по элементам контура (ощущая вытекающий азот и отмечая изменение характера шума).При небольших утечках давления падает гораздо более медленно и негерметичность обнаруживается при нанесении на подозрительные места контура мыльного раствора («обмыливания») и наблюдении за появлением пузырьков в негерметичных точках.
Однако давление может менятся и при отсутствии утечек, если во время испытания значительно меняется температура.
Действительно, если, например, температура окружающей среды повышается, температура азота также повышается и он расширяется. Это расширение (объем, занимаемый азотом в установке, не меняется) вызывает, естественно, повышение давления в контуре. И наоборот, снижение температуры окружающей среды вызывает снижение давления, обусловленное сжатием азота.
Изменение давления, вызванное изменениям температуры, подчиняется закону Шарля:
После нескольких часов выдержки установки под давлением (например, в течение ночи для установки значительных размеров), если изменения давления не выходят за пределы, обусловленные законом Шарля, можно с уверенностью сделать вывод об отсутствии утечек.
Заправка хладагентом и хладоносителем
Для этого в системе предусматриваются заправочный коллектор, специальный вентиль или ниппель. Заправку производят в линейный ресивер, жидкостный ресивер или в конденсатор.
Чиллеры, сплит-системы и моноблоки обычно заправляются маслом и холодильным агентом на заводе. Для проверки заправки, следует присоединить к ниппелю манометр и, учитывая температуру окружающего воздуха, проверить давление в системе. Установка находится при температуре окружающего воздуха, поэтому холодильный агент внутри находится при температуре окружающего воздуха. Температурная шкала соответствующего хладагента на манометре должна показать температуру окружающего воздуха. Если значения температуры, отличаются, то машина либо не заправлена, либо заправлена инертным газом.
Перед заправкой необходимо проверить, все ли манометры и приборы автоматизации на месте, сняты ли заглушки на сторонах нагнетания и всасывания компрессора. Смесевые неазеатропные и псевдоазеатропные холодильные агенты (R404A) заправлять можно только в жидкой фазе, баллон подключают к жидкостному ресиверу и установку заправляют жидким холодильным агентом.
Холодильные агенты, являющиеся моновоеществами (R134A, R22), и азеатропные смеси (R507) можно заправлять в жидкой и газовой фазах. При этом баллон присоединяют к всасывающей линии работающей холодильной установки, и компрессор отсасывает из баллона пары агента в систему.
Запрещается для ускорения заправки греть баллон газовой горелкой или ставить баллон в горячую воду. Холодильные установки заправляют по массе, для чего используют весы или, что менее предпочтительно, зарядные цилиндры. В документации по оборудованию должна быть указана масса заправки.
Для заправки из баллона, на резьбовой штуцер навинчивают заправочный шланг, второй конец шланга присоединяют к системе, но гайку до конца не завинчивают и ставят баллон на весы. Перед заправкой необходимо продуть шланг от воздуха, для чего открывают на баллоне вентиль, и воздух выдавливается холодильным агентом из шланга, после чего гайку завинчивают. Заправочные вентили или ниппели на холодильной установке открывают, и по шлангу холодильный агент перетекает из баллона в систему, по весам контролируют массу заправленного агента. Более грамотно использовать заправочный коллектор и заправочные весы.
При заправке большого количества хладагента массу заправки контролируют приблизительно. Например, если необходимо заправить 500 кг хладагента, то общую массу заправки делят на массу хладагента в баллоне и получают необходимое количество баллонов. При этом считается, что если заправлены все баллоны, то масса заправки составляет требуемую величину.
Условная схема заправки хладогентом (фреоном):
![]() |
||||||||||||||||||||||||||||||||||
|
Перед заправкой хладагента необходимо поместить баллон на весы для контроля массы заправки хладагента.
При заправке хладагентом удобно пользоваться линейкой для перевода значений давления в температуру насыщения хладагента.
Проверка электрооборудования
После завершения монтажа электрооборудования необходимо проверить правильность подключения согласно технической документации.
Проверка осуществляется методом прозвонки. Как правило, данную проверку осуществляют два человека – один устанавливает временную перемычку в щите управления, второй, находясь непосредственно у компонента, проверяет, замкнуты ли кабели. В случае, если кабели подключены от соответствующего агрегата или прибора в нужные клеммы, временную перемычку снимают и переходят к следующим кабелям.
После проверки правильности подключения, проверяют правильность направления вращения валов трехфазных электродвигателей. У крупных компрессорных агрегатов в щитах предусмотрена защита от неправильного направления вращения, но на этом этапе муфты компрессора и электродвигателя разъединены, электродвигатель запускают отдельно. В документации изготовителя оборудования всегда указано правильное направление вращения электродвигателя, в случае, если при пробном запуске двигатель крутится в обратную сторону, следует перекинуть фазы в щите или в клеммной коробке электродвигателя и внести изменения в монтажную документацию. Направление вращения особенно важно для винтовых и спиральных компрессоров, для поршневых компрессоров направление вращения не имеет значения.
Направление вращения вентиляторов определяется при кратковременном пуске, для определения направления вращения электродвигателя герметичного насоса необходимо снять пластиковую защитную муфту в месте стыковки вала насоса и электродвигателя. Кратковременный пуск без среды не повредит центробежному насосу. Подав напряжение, по вращению вала определяют, крутится ли двигатель в направлении, указанном производителем насоса.
При проверке направления вращения полугерметичного винтового компрессора следует руководствоваться следующей последовательностью действий:
Установить манометры на всасывании и нагнетании.
Замкнуть магнитный пускатель (контактор) компрессора вручную и удерживать не более 2 с. Если после ручного отключения катушки контактора компрессор продолжает работать, немедленно отключить питание установки.
Во время краткого пуска контролировать давление по манометрам. Если давление по манометру всасывания падает, а по манометру нагнетания увеличивается, то компрессор подключен правильно. В противном случае необходимо поменять направление вращения.
Мы рекомендуем Вам всегда заказывать оборудование и его монтаж у одной компании, т.к. в этом случае вы всегда получаете полноценную гарантию и застрахованы от преждевременного ремонта.
На рынке Киева, по нашим предположениям, лишь 10-20% компаний используют вакуумирование, 70% занижают сечение межблочной электропроводки, некоторые используют тонкую и ломкую медную трубу, уголки вместо П-образных кронштейнов. Даже при монтаже чужого кондиционера мы закомплектовываем свои монтажные бригады согласно технических данных и необходимых именно для данного кондиционера комплектующих, учитываем рекомендованный производителем межблочный кабель.
www.vecotech.com.ua
Испытания холодильных установок
Испытания холодильной системы на прочность.
Необходимость испытаний холодильной системы на прочность определяется организацией-разработчиком холодильного оборудования, при этом возможны испытания как отдельных элементов, так и всей холодильной установки.
Ниже приведена последовательность действий при испытании на прочность установки в целом. Отличие испытания всей установки от испытаний отдельных элементов приведены ниже.
Давление для проведения испытаний на прочность указывается в технической документации конкретной холодильной установки и зависит от области её применения и типа хладагента.
При испытаниях холодильной установки на прочность используется следующее оборудование:
- Манометры (2 шт.) класса точности не ниже 1,5 с диаметром корпуса не менее 160 мм и шкалой с максимальным значением, равным 4/3 измеряемого давления;
- баллоны с азотом;
- редуктор с предохранительным клапаном, предназначенный для работы с азотом.
Испытания холодильного контура на прочность проводятся путем заполнения магистралей сухим (точка росы не выше -40 °С) азотом под давлением.
Испытания необходимо проводить в следующей последовательности:
- Установить один манометр после запорного вентиля у источника давления, а второй—в самой удаленной точке системы.
- В холодильном контуре открыть запорные вентили и при необходимости—электромагнитные клапаны—так, чтобы каждый участок контура имел возможность подачи и сброса азота.
- Отключить от контура все приборы КИПиА, а также другие элементы, не рассчитанные на давление испытания.
- Поднять давление в контуре до величины давления испытания. Подъем давления следует осуществлять со скоростью не выше 1 бар в минуту. При достижении давления, равного 0,3 и 0,6 давления испытания, а также при давлении испытания, необходимо прекратить повышение давления и провести промежуточный осмотр и проверку наружной поверхности контура.
- Под давлением испытания система должна находиться не менее 10 мин, после чего давление следует постепенно снизить до расчетного, также указанного в документации. Затем следует осмотреть наружную поверхность сосудов, аппаратов, трубопроводов, арматуры с проверкой герметичности швов и разъемных соединений мыльным раствором.
- Результаты признаются удовлетворительными, если во время испытаний не произошло разрывов, видимых деформаций, падения давления по показаниям манометра.
- При обнаружении утечек, деформаций, разрывов необходимо сбросить давление из контура, выполнить работы по устранению неисправностей и повторить предыдущие операции.
Испытания отдельных элементов холодильного контура проводятся в последовательности, указанной выше, но с учетом следующих мероприятий: - испытываемый элемент холодильного контура (сосуд, аппарат, трубопровод) должен быть отсоединен от других элементов с использованием металлических заглушек с прокладками, имеющими хвостовики, выступающие за пределы фланцев не менее, чем на 20 мм. Толщина заглушки указывается в документации.
- места расположения заглушек на время проведения испытания должны быть отмечены предупредительными знаками, и пребывание около них людей не допускается.
- использование запорной арматуры для отключения испытуемого сосуда (аппарата), трубопровода не допускается.
Контрольные вопросы:
- Кто принимает решение о проведении испытаний на прочность?
- Кто назначает давление для проведения испытаний на прочность?
- В какой последовательности проводятся испытания на прочность?
- Какие особенности существуют при испытании отдельного элемента холодильного контура?
Испытания системы на плотность.
Проверка холодильного контура на плотность (опрессовка) проводится в обязательном порядке для обнаружения мест возможных утечек хладагента, а также после завершения ремонтных работ, связанных с разгерметизацией холодильного контура.
Испытания на плотность проводятся раздельно по сторонам высокого и низкого давления. При равенстве давлений испытания для стороны высокого и низкого давления, например, для установок с воздухоохладителями, допускается проводить испытание на плотность всей системы.
Давление для проведения испытаний на плотность назначается организацией-разработчиком и указывается в технической документации. Оно зависит от области применения установки и типа хладагента.
При испытаниях холодильной установки на плотность используется следующее оборудование:
- Манометры (2 шт.) класса точности не ниже 1,5 с диаметром корпуса не менее 160 мм и шкалой с максимальным давлением, равным 4/3 измеряемого давления;
- баллоны с азотом;
- редуктор с предохранительным клапаном, предназначенный для работы с азотом.
Испытания холодильного контура на плотность проводятся путем заполнения магистралей сухим (точка росы не выше минус 40 °С) азотом под давлением.
При равенстве давлений испытания для стороны высокого и низкого давлений, последовательность испытаний такова:
- Установить один манометр был установлен после запорного вентиля у источника давления, а второй—в самой удаленной точке системы.
- В холодильном контуре открыть запорные вентили и, при необходимости, электромагнитные клапаны так, чтобы каждый участок контура имел возможность подачи и сброса азота.
- Поднять давление в контуре до величины давления испытания. Подъем следует осуществлять со скоростью не выше 1 бар в минуту. При достижении давления, равного 0,3 и 0,6 давления испытания, необходимо прекратить повышение давления и провести промежуточный осмотр и проверку наружной поверхности контура.
- Не производить никаких манипуляций с установкой в течение не менее 3 часов для выравнивания температур внутренней и наружной среды. Зафиксировать давление в контуре и температуру окружающей среды.
- Выдержать установку под давлением не менее 12 часов. По прошествии данного времени проверить давление в контуре. Изменений давления, кроме вызванных колебаниями температуры окружающей среды, быть не должно. Эти изменения определяются следующей зависимостью:
P1/P2=T1/T2,
где P1, P2 – абсолютные значения давления газа в контуре, бар, T1, T2 – термодинамическая температура газа в контуре, К.
- Если во время испытаний не произошло разрывов, видимых деформаций, падения давления по показаниям манометра, их результаты признаются удовлетворительными,.
- При обнаружении утечек, деформаций, разрывов необходимо сбросить давление из контура, выполнить работы по устранению неисправностей и повторить предыдущие операции.
Контрольные вопросы:
- В каких случаях проводят испытания на плотность?
- Кто назначает величину давления для проведения испытаний?
- Какова последовательность действий при проведении испытаний на плотность?
Испытание на вакуум (вакуумирование холодильного контура)
Вакуумирование холодильного контура проводится для удаления воздуха из агрегатов и трубопроводов и осушения холодильного контура после завершения ремонтных работ, а также после проведения испытаний на прочность и/или плотность.
Вакуумирование проводится до восстановления теплоизоляции, нарушенной при проведении ремонтных работ.
Использовать для вакуумирования компрессор холодильной установки категорически запрещено. Подавать напряжение на компрессор и проверять целостность его цепей в процессе выполнения работ по вакуумированию запрещено.
Исходное состояние холодильной установки перед вакуумированием зависит от вида выполненного ремонта и характеризуется изолированностью участка холодильного контура, на котором выполнялись ремонтные работы, от остальной схемы холодильной установки. В этой связи выбор сервисных штуцеров для подключения вакуумного оборудования, используемого в процессе вакуумирования, производится оператором в зависимости от участка, который требуется вакуумировать.
Для проведения вакуумирования применяют следующее оборудование:
- манометрический коллектор*;
- комплект гибких шлангов*;
- вакуумный насос;
- вакуумметр.
Оборудование, помеченное *, должно быть предназначено для работы с применяемыми в установке хладагентом и маслом и иметь соответствующую маркировку.
Порядок действий при ваккумировании:
- Произвести сборку схемы вакуумирования с таким расчетом, чтобы расстояние между вакуумным насосом и холодильной установкой было как можно меньшим, а диаметр соединительных шлангов как можно большим.
- Подключить манометрический коллектор к контуру и убедиться в отсутствии избыточного давления. При наличии избыточного давления, понизить его до атмосферного и проконтролировать его рост.
- Подключить вакуумный насос к сервисным штуцерам вакуумируемого участка холодильного контура.
- Подключить вакуумметр в наиболее отдаленной от места установки вакуумного насоса точке.
- Открыть вентиль перед вакуумным насосом и, при необходимости, электромагнитные клапаны так, чтобы каждый участок подлежащего вакуумированию контура имел возможность подключения вакуумного насоса.
- Включить насос и отвакуумировать холодильный контур до остаточного давления
- Остаточное давление следует принять 1 кПа (8 мм рт.ст.).
Вакуумирование рекомендуется проводить при нормальных температурных условиях в помещениях (20°С), в крайнем случае, при температуре в помещениях с холодильным оборудованием не ниже 5°С.
При низких температурах (ниже 2°С) рекомендуется проводить обогрев помещения, в которых размещен вакуумируемый участок контура.
При протяженных трассах трубопроводов рекомендуется разбить подлежащий вакуумированию участок на несколько подучастков (с помощью запорных вентилей) и проводить вакуумирование по подучасткам.
Запрещается подогревать участки холодильного контура открытым пламенем.
После достижения величины остаточного давления, следует продолжить вакуумирование в течении 18 часов. После этого следует закрыть вентиль и выключить вакуумный насос.
Если при низких температурах не удается достичь необходимой величины остаточного давления, то процесс вакуумирования следует чередовать с процессом наддува сухим азотом (отсоединяя насос) до абсолютного давления 2…3 бар.
При проведении испытаний холодильная установка должна находиться под вакуумом в течении 18 часов, при этом изменение давление в контуре должно фиксироваться не реже, чем через 1 час. Допускается повышение давления до 50% за первые 6 ч. В остальное время давление должно оставаться постоянным.
Если по окончании вакуумирования заправка установки хладагентом не планируется, то установку необходимо заполнить сухим азотом до абсолютного давления 2…3 бар.
Если в первые 3 часа выдержки под вакуумом давление резко повышается до уровня давления насыщенных паров воды, соответствующего температуре окружающей среды в помещении, а затем стабилизируется, то, значит, система герметична, но не достаточно осушена. Необходимо продолжить вакуумирование.
Если за 18 часов рост давления превысил 500 Па (5 мбар), давление не стабилизируется на уровне давления насыщенных паров воды при температуре окружающей среды и продолжает расти, то установка негерметична. Следует произвести поиск и устранить причину негерметичности контура. После этого повторить работы по вакуумированию.
Ниже приведена таблица зависимости давления насыщенных паров воды от температуры окружающей среды.
T,°C | 0 | 4 | 8 | 12 | 16 | 20 | 24 | 28 | 32 |
Р, Па | 610 | 812 | 1072 | 1401 | 1817 | 2337 | 2982 | 3778 | 4753 |
Контрольные вопросы:
- В каких случаях проводят вакуумирование холодильного контура?
- Какова последовательность действий при вакуумировнии?
- Какова величина остаточного давления при вакуумировании?
- Какова допустимая величина остаточного давления после завершения испытаний? В каких случаях оно превышает необходимую величину?
Заправка маслом
![]() |
Слив масла из герметичного компрессора |
Полугерметичные и открытые (сальниковые) компрессоры оснащаются смотровыми окнами на картерах; во время работы уровень масла должен находиться в центре или немного выше центра смотрового окна. Низкий уровень масла может привести к недостаточному смазыванию деталей; а высокий – к масляным пробкам, повреждениям клапанов компрессора или переизбытку масла в системе.
Уровень масла может существенно варьироваться при запуске, когда жидкий хладагент находится в картере, поэтому проверять уровень масла следует во время работы компрессора после выхода холодильной установки на режим.
Некоторые виды хладагентов поглощаются маслом, и, чтобы избежать выделения хладагента, следует установить нагреватель масла или применять устройство для слива хладагента перед сливом масла.
Рекомендуется провести следующие процедуры:
- Закрыть запорные вентили на компрессоре,
- Включить нагреватель масла,
- Откачать газообразный хладагент (с помощью устройства слива хладагентов)
- Слить масло в специальные промаркированные емкости (при необходимости—с помощью азота.)
Заправка масла в герметичный компрессор
Перед заправкой масла компрессор необходимо отключить от системы с помощью запорных вентилей, масло должно быть удалено из отверстия на линии всасывания путем наклона компрессора. Перед процедурой следует точно отмерить необходимое количество масла. Тип и количество заправляемого масла можно узнать из инструкции по эксплуатации. Чтобы избежать чрезмерного поглощения хладагента маслом или выпускания хладагента, следует установить нагреватель для масла.
Заправка масла в полугерметичные и открытые (сальниковые) компрессоры
Метод для открытой системы
Пример масляного насоса |
При наличии хладагента в компрессоре, следует закрыть всасывающий клапан компрессора и снизить давление в картере до уровня немного менее 0 бар. Затем отключить компрессор и закрыть его запорные вентили.
Существуют небольшие насосы для закачки масла в компрессоры. При необходимости закачка в работающий компрессор осуществляется через рабочее отверстие; можно использовать насос для заливки масла напрямую в картер, где не всегда возможна подача самотёком. Во время работы компрессора обратный клапан насоса препятствует утечке хладагента, позволяя создать достаточное давление для преодоления давления всасывания и закачать масло. В ситуации, когда отсутствует масляный насос и невозможно произвести заправку масла в картер, масло можно залить в компрессор с помощью сервисного клапана на линии всасывания.
Необходимо соблюдать максимальную осторожность, чтобы в компрессор не попал воздух.
Метод с применением азота и вакуума
Другим методом замены масла при ремонте, обслуживании или монтаже компрессора является использование азота и вакуумного насоса для заливки масла. Далее следует описание этого метода:
![]() | Замена масла (слив):
|
Замена масла (заправка):
| |
Примечание: Так как масла (особенно полиэфирные) поглощают влагу, необходимо использовать малые емкости с маслом. Запрещается хранить в открытом состоянии канистры с полиэфирными маслами, предназначенными для дальнейшего использования. |
Контрольные вопросы:
- Как заправлять масло в герметичный компрессор?
- Как производится заправка в полугерметичный и открытый (сальниковый) компрессоры?
Заправка хладагентом и хладоносителем
Заправка хладагентом.
В зависимости от установки, заправку холодильным агентом производят из цистерн или баллонов. Для этого в системе предусматриваются заправочный коллектор, специальный вентиль или ниппель. Заправку производят в линейный ресивер, жидкостный ресивер или в конденсатор.
Чиллеры, сплит-системы и моноблоки обычно заправляются маслом и холодильным агентом на заводе. Для проверки заправки, следует присоединить к ниппелю манометр и, учитывая температуру окружающего воздуха, проверить давление в системе. Установка находится при температуре окружающего воздуха, поэтому холодильный агент внутри находится при температуре окружающего воздуха. Температурная шкала соответствующего хладагента на манометре должна показать температуру окружающего воздуха. Если значения температуры, отличаются, то машина либо не заправлена, либо заправлена инертным газом.
Перед заправкой необходимо проверить, все ли манометры и приборы автоматизации на месте, сняты ли заглушки на сторонах нагнетания и всасывания компрессора. Смесевые неазеатропные и псевдоазеатропные холодильные агенты (R404A) заправлять можно только в жидкой фазе, баллон подключают к жидкостному ресиверу и установку заправляют жидким холодильным агентом.
Холодильные агенты, являющиеся моновоеществами (R134A, R22), и азеатропные смеси (R507) можно заправлять в жидкой и газовой фазах. При этом баллон присоединяют к всасывающей линии работающей холодильной установки, и компрессор отсасывает из баллона пары агента в систему.
Запрещается для ускорения заправки греть баллон газовой горелкой или ставить баллон в горячую воду. Холодильные установки заправляют по массе, для чего используют весы или, что менее предпочтительно, зарядные цилиндры. В документации по оборудованию должна быть указана масса заправки.
Для заправки из баллона, на резьбовой штуцер навинчивают заправочный шланг, второй конец шланга присоединяют к системе, но гайку до конца не завинчивают и ставят баллон на весы. Перед заправкой необходимо продуть шланг от воздуха, для чего открывают на баллоне вентиль, и воздух выдавливается холодильным агентом из шланга, после чего гайку завинчивают. Заправочные вентили или ниппели на холодильной установке открывают, и по шлангу холодильный агент перетекает из баллона в систему, по весам контролируют массу заправленного агента. Более грамотно использовать заправочный коллектор и заправочные весы.
При заправке большого количества хладагента массу заправки контролируют приблизительно. Например, если необходимо заправить 500 кг хладагента, то общую массу заправки делят на массу хладагента в баллоне и получают необходимое количество баллонов. При этом считается, что если заправлены все баллоны, то масса заправки составляет требуемую величину.
Примерная схема заправки выглядит следующим образом:
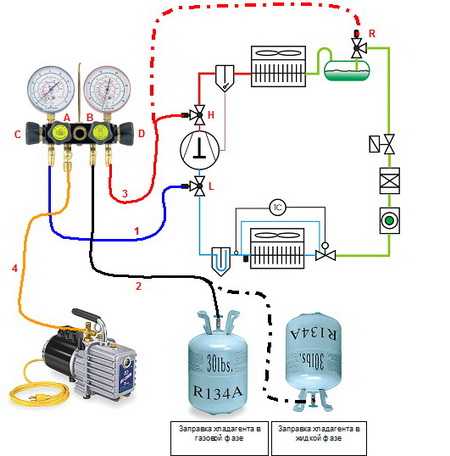
Перед заправкой хладагента необходимо поместить баллон на весы для контроля массы заправки хладагента
Заправка хладагента (жидкого и газообразного) в систему, находящуюся под вакуумом | |
---|---|
A,B,C,D | Закрыты |
1,2,4 | Подключить согласно изображению |
3 | Подключить к H или R |
L, H или R | Открыть (в среднем положении), L для заправки в газообразной фазе, R для заправки в жидкой фазе |
B | Открыт (вентиль баллона открыт) |
D | Открыт для заправки в жидкой фазе |
C | Открыт для заправки в газообразной фазе |
Запустить компрессор системы | |
Прекратить заправку | |
B, C, D | Закрыты (вентиль баллона закрыт) |
Проверить давление в системе | |
H, R | Открытое положение (сервисные порты отключены) |
D, C | Открыты |
Выравнивание давлениия | |
L | Открытое положение (сервисные порты отключены) |
D, C | Закрыты |
При заправке хладагентом удобно пользоваться линейкой для перевода значений давления в температуру насыщения хладагента.
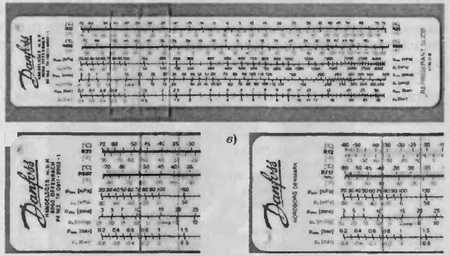
Заправка хладоносителем.
Заправку систем хладоносителем производят через специально предназначенные для этого штуцеры или в бак хладоносителя. В крупных установках предусматривают специальные станции по приготовлению хладоносителя – баки объемом до 5 м3, оборудованные стационарными насосами для перекачивания хладоносителя в систему.
Приходящий в бочках гликоль следует наливать в указанной в технической документации пропорции во временную чистую емкость (бочку, бак). Затем на бочку навинчивают специальный ручной бочковой насос (например «Biltema») или используют обычный бытовой насос типа «Малыш», который применяют для добавки в емкость чистой воды, хорошо размешивают и тем же насосом по шлангам заправляют в систему. При необходимости добавки ингибиторов, их необходимо внести в раствор, строго следуя указаниям технической документации.
При разведении гликолей следует руководствоваться следующими правилами:
- нельзя закачивать в систему гликоль, а потом воду, закачивать можно только готовый раствор;
- необходимо предусмотреть меры по защите площадки от проливов гликолей, не допускать проведения работ вблизи открытого пламени и курения, приготовить средства пожаротушения,
При заправке системы растворами солей, таких как СаС12 , следует соблюдать следующие правила: - Приготовленному раствору необходимо дать отстояться;
- Отбор готового раствора не следует делать из нижней точки во избежание попадания загрязнений, оставшихся после отстаивания.
- Насос для заполнения требуется обеспечить фильтром на всасывании.
- Необходимо применять насос, пригодный для работы с агрессивной средой.
Контур оборотного водоснабжения заполняют из водопровода по подпиточной трубе. Как правило, на трубопроводе подпитки устанавливается система водоподготовки. При заполнении в зимнее время системы оборотного водоснабжения обогреватели поддонов конденсаторов и градирен, встроенных в испарительные конденсаторы насосов, необходимо включить заранее.
Контрольные вопросы:
- Как производится заправка холодильной системы хладагентом?
- Как производить заправку системы хладоносителем?
Литература
- Полевой А. А. Монтаж холодильных установок: Учеб. Пособие для вузов. – СПб.: Политехника, 2005. – 259 с.: ил.
Проверка электрооборудования.
После завершения монтажа электрооборудования необходимо проверить правильность подключения согласно технической документации.
Проверка осуществляется методом прозвонки. Как правило, данную проверку осуществляют два человека – один устанавливает временную перемычку в щите управления, второй, находясь непосредственно у компонента, проверяет, замкнуты ли кабели. В случае, если кабели подключены от соответствующего агрегата или прибора в нужные клеммы, временную перемычку снимают и переходят к следующим кабелям.
После проверки правильности подключения, проверяют правильность направления вращения валов трехфазных электродвигателей. У крупных компрессорных агрегатов в щитах предусмотрена защита от неправильного направления вращения, но на этом этапе муфты компрессора и электродвигателя разъединены, электродвигатель запускают отдельно. В документации изготовителя оборудования всегда указано правильное направление вращения электродвигателя, в случае, если при пробном запуске двигатель крутится в обратную сторону, следует перекинуть фазы в щите или в клеммной коробке электродвигателя и внести изменения в монтажную документацию. Направление вращения особенно важно для винтовых и спиральных компрессоров, для поршневых компрессоров направление вращения не имеет значения.
Направление вращения вентиляторов определяется при кратковременном пуске, для определения направления вращения электродвигателя герметичного насоса необходимо снять пластиковую защитную муфту в месте стыковки вала насоса и электродвигателя. Кратковременный пуск без среды не повредит центробежному насосу. Подав напряжение, по вращению вала определяют, крутится ли двигатель в направлении, указанном производителем насоса.
При проверке направления вращения полугерметичного винтового компрессора следует руководствоваться следующей последовательностью действий:
- Установить манометры на всасывании и нагнетании.
- Замкнуть магнитный пускатель (контактор) компрессора вручную и удерживать не более 2 с. Если после ручного отключения катушки контактора компрессор продолжает работать, немедленно отключить питание установки.
- Во время краткого пуска контролировать давление по манометрам. Если давление по манометру всасывания падает, а по манометру нагнетания увеличивается, то компрессор подключен правильно. В противном случае необходимо поменять направление вращения.
Контрольные вопросы:
- Какие проверки электрооборудования необходимо проводить?
www.prof2.ru
Вакуумирование кондиционера / Техническая информация / Systemsclimate.ru
Установку кондиционера, лучше доверить профессионалам, так как это довольно сложный процесс, который требует наличие определенных навыков и специального оборудования. Поэтому, если вы не знаете что такое вакуумирование кондиционера, не стоит самому заниматься этим делом. При монтаже внутренний и наружный блок кондиционера соединяют с помощью специальных трубок, изготовленных из меди. По этим трубкам, под воздействием компрессора, в холодильном контуре, происходит циркуляция хладагента. Для более продуктивного теплообмена, наружный блок охлаждается установленным вентилятором.
Вакуумирование кондиционера — это создание в контуре герметичности, путем откачивания воздуха. Этот процесс позволяет избавить сплит-систему от различных частиц мусора, масла или воды, которые мешают нормальной работе вашей техники. Медные трубки, которые связывают внутренний и внешний блок, очень важны для работы кондиционера, поэтому при установке данной техники, к их монтажу предъявляются самые высокие требования. В них также не должно находиться частиц пыли, песка или стружки, а места соединения трубок с корпусом — быть полностью герметичными. Чтобы когда будет происходить вакуумирование кондиционера, не было утечки фреона.
После того, как трубки проложены и тщательно, герметично соединены с кранами блока, следует избавиться от воздуха, который остался в контуре теплообменника. При его наличии, даже в небольшом количестве, произойдет перемешивание хладагента, который циркулирует в системе, а это способно вызвать необратимые изменения характеристик фреона. Все это приведет, если не будет произведено вакуумирование кондиционера, к частичному обмерзанию рабочих частей кондиционера, снижению производительности и как результат — к неправильной, в аварийном режиме, работе всей холодильной системы.
Наличие частиц водяного пара, также может оказать негативное влияние на работу вашей техники. Данный пар, который появляется, если не было проведено вакуумирование кондиционера, смешивается с попавшим в контур воздухом, способен раствориться в масле, предназначенном для смазки рабочих частей компрессора. Данная ситуация приводит к снижению качества смазочного материала и, как следствие, к быстрому износу компрессора, который является самой дорогостоящей и важной частью всего кондиционера. Для предотвращения поломок такого рода, делают вакуумирование кондиционера, для чего используют специальный насос.
Вакуумирование кондиционера — происходит следующим образом. На кране наружного блока находиться сервисный порт, к которому через специальный коллектор оснащенный манометром, подсоединяют вакуумный насос. Данный прибор откачивает весь имеющийся воздух из контура, в результате чего создается полный вакуум. Время работы данной техники зависит от длины соединительных трубок и мощности самого насоса. Вакуумирование кондиционера, можно контролировать по подключенному манометру, который располагается на коллекторе.
После того, как в контуре образовался необходимый вакуум, насос прекращает откачку воздуха и выключается. Вакуумирование кондиционера подошло к концу, теперь необходимо в течение получаса контролировать давление в системе, что осуществляется с помощью манометра. Если стрелка манометра изменяет свое положения — это показывает наличие негерметичного соединения. В этом случае, необходимо определить в каком месте происходит подсос воздуха, и устранить данную неисправность. Обеспечив необходимую герметичность, вновь проводят вакуумирование кондиционера, если все сделано правильно, стрелка манометра должна неподвижно стоять на одном значении.
В то время как проводиться вакуумирование кондиционера, можно монтировать крепление трассы, подгонять крышки коробов, подключать питание, чтобы завершить все этапы установки агрегата. После того, как манометр показал отсутствие негерметичных соединений, можно производить запуск фреона в контур системы. Для этого открывают краны наружного блока, которые мешают прохождению хладагента в трубки. Если вакуумирование кондиционера прошло успешно, можно протестировать работоспособность установленного агрегата.
Во время первого запуска, проверяют работу кондиционера в различных режимах, при этом внимательно следят за тем, чтобы производительность системы полностью соответствовала характеристикам, которые представлены в технической документации, приложенной к данному виду техники. Сам процесс работы, после того как было проведено вакуумирование кондиционера, заключается в следующем.
Фреон, находящийся во внутреннем блоке, из-за низкого давления закипает и начинает испаряться. Теплообменник, обдуваемый встроенным вентилятором, поглощает выделенное кипящим фреоном тепло, в результате преобразует его в газообразное состояние. После этого происходит подача газообразного фреона в компрессор, который находится в наружном блоке. Данный процесс полностью цикличен, и повторяется постоянно.
Бывает, что недобросовестные работники, не используют вакуумирование кондиционера, а просто выпускают некоторую часть фреона, чтобы он выдавил имеющийся воздух из системы. Конечно, данная процедура, точнее потеря некоторого количества хладагента, не сказывается отрицательно на работе агрегата, особенно если трасса небольшой длины (до пяти метров). Проблема заключается в другом. Если не было произведено вакуумирование кондиционера, тогда никто не даст гарантию, что в системе не осталось воздуха.
Как бы вас не убеждали, но на глаз определить качество продувки контура, просто невозможно. Практика показывает, что различные проблемы в работе холодильной технике, возникают именно там, где работники пренебрегли правилами, и не сделали вакуумирование кондиционера. Но самое главное, после этого очень сложно определить причину неудовлетворительной работы кондиционера, ведь диагностика не всегда дает однозначный результат о причине поломки.
В связи с этим, теряется много времени, чтобы определить неисправность, причем устранение этого недостатка, обходиться довольно дорого. Ведь необходимо полностью извлечь фреон из контура системы, после чего заправить новой, тщательно отмерянной порцией хладагента, который дорого стоит. После заново провести вакуумирование кондиционера, что тоже не быстрый процесс. Поэтому, для установки кондиционера, следует обращаться в солидные компании, которые пришлют профессиональных работников, имеющих необходимое оборудование, навыки и опыт.
Ведь только вакуумирование кондиционера, которое было произведено специалистом, позволит точно убедиться в отсутствии воздуха и герметичности системы. Это в свою очередь полностью исключит возможность утечки хладагента. Именно наличие, в первые часы работы, утечки фреона, сигнализирует о некачественной работе монтажника, который или не обеспечил герметичность, или не стал делать вакуумирование кондиционера.
Если в процессе работы произошла поломка компрессора, тогда экспертиза поможет определить причину, по которой агрегат вышел из строя. Это может быть потеря значительной части фреона, заводской брак, работа в экстремальных условиях или небрежное вакуумирование кондиционера привело к подсосу воздуха. Современная техника обладает способностью подавать сигналы, которые сообщат о возможной причине неправильной работы, главное не игнорировать данные сигналы, ведь это может привести к серьезным последствиям.
Поэтому стоит не только проконтролировать лично установку техники, чтобы рабочие качественно провели вакуумирование кондиционера, но и самому соблюдать элементарные технические требования при использовании этого агрегата.
systemsclimate.ru
Вакуумирование, проверка и запуск кондиционера
Итак, после основных процедур установки кондиционера, осталось выпустить хладагент в систему и проверить правильность работы агрегата.
Обычно во внешнем блоке сплит-системы фреон есть еще с завода. Количество его оптимально, поэтому нужно только правильно заполнить им остаток контура.
Самопроизвольную утечку хладагента из кондиционера предотвращают особые клапаны.
После того, как система смонтирована, трубопроводы подключены, нам нужно удалить воздух и влагу из холодильного контура, а затем заполнить систему фреоном, открыв клапана.
Вакуумирование делаем таким образом:
-присоединим манометрический коллектор кондиционеру
-присоединим шланг для заправки к вакуумному насосу
-откроем вентиль низкого давления
-включим насос для вакуумирования
-после завершения процедуры закроем вентиль на коллекторе
-после этого можно включить насос
-шестигранником откроем оба вентиля на кондиционере и запустим хладагент в контур
Монтажники определяют время вакуумирования по давлению на манометре – после того, как давление становится отрицательным, они завершают вакуумирование, поскольку считают, что воздуха в системе нет.
Тем не менее, это не верно. Как правило, в воздухе остается влага, которая испаряется во время вакуумирования.
Чтобы остатки влаги полностью улетучились, процедуру нужно проводить не менее 15 минут (для обычного маломощного кондиционера). Для более мощных сплит-систем это время должно быть увеличено.
Влага в системе может погубить даже самый дорогой кондиционер, так как вызывает повреждение компрессора, окисление и т.д. Поэтому удалению влаги следует уделять должное внимание.
Как правило, дозаправка при установке кондиционеру не нужна, так как на заводе систему заправляют фреоном из расчета на 5-метровую трассу. Если вы планируете монтировать трассу длиннее, систему необходимо дозаправить хладагентом.
Обычно достаточно от 5 до 20 граммов хладагента на 1м. дополнительного трубопровода. Точную массу фреона для дозаправки нужно точно высчитать во избежание потери мощности системы.
Проверка сплит-системы после монтажа.
Прежде всего, после включения кондиционера, нужно проверить температуру на выходе, которая не должна быть ниже нуля. Отрицательная температура свидетельствует о недостатке фреона и необходимости дозаправки.
Также стоит проверить работу системы в режиме обогрева.
Для проверки дренажного трубопровода можно налить воды на испарители или в поддон внутреннего блока и проследить за тем, насколько свободно и быстро она уходит.
После того, как мы все проверили, можно порадоваться успешной установке сплит системы.
r410a.ru