гидравлическая, видео-инструкция по монтажу своими руками, балансировочный клапан, фото и цена
Если вы думаете, что установив котел, дополнительное оборудование и трубопроводы, подсоединив к ним радиаторы и заполнив систему теплоносителем можно считать, что работа сделана, это не так. Хотя и основной массив завершен, остается важный этап – настройка системы отопления или ее балансировка. Главная задача процесса – правильное распределение энергии теплоносителя по комнатам.
Сегодня мы расскажем, как это делается в частном доме.
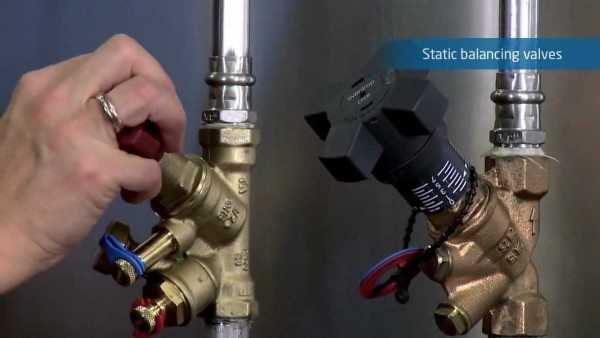
Самостоятельная балансировка отопления с помощью кранов
Все работы можно выполнить своими руками, соблюдая несложные рекомендации. Есть ошибочное мнение, что балансировку нужно делать только в крупных зданиях, однако этот посыл не верен. Она требуется для любых строений, а особенно жилых, в противном случае тепло в одни помещения будет идти с избытком, а в других, наоборот, ощущаться его недостаток.
Наша задача сегодня – рассказать, как можно не допустить такого дисбаланса. В итоге котел, радиаторы и остальные элементы системы будут работать как одно целое, и обогревать равномерное строение.
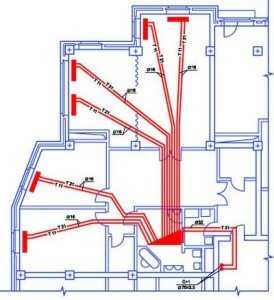
На фото — перед началом работы системы отопления необходимо провести ее настройку и регулировку
Основная цель
Как бы мы ни старались сделать правильно отопительный контур, нередко получается так, что последняя батарея прогревается не просто дольше, но и недостаточно.
Повышать мощность ни системы, ни насоса в данном случае нет резона, так как проблема не в этом.
- Балансировка служит для распределения теплоэнергии, поступающей от теплогенератора по трубопроводам, в зависимости от потребностей каждой комнаты.
- Помогает выполнять данную процедуру, прежде всего, запорно-регулирующая арматура. Она является важным компонентом отопления, который дает возможность увеличивать или уменьшать поток теплоносителя на определенный участок отопительной системы.
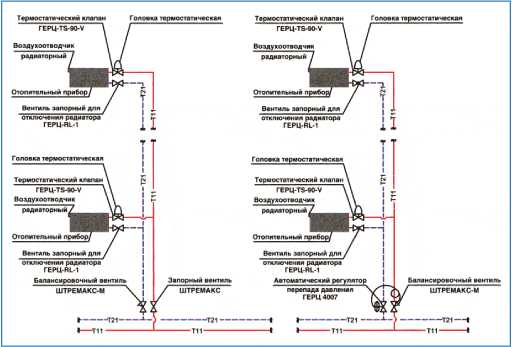
Гидравлическая увязка тупиковой схемы двухтрубного водяного отопления – слева статическая балансировка, справа – динамическая
Совет: установка автоматической аппаратуры регулировки температуры не исключает проведения балансировки батарей.
- В данном случае они являются только дополнительным средством, которое позволяет поддерживать необходимый комфорт в помещениях.
- Настройка радиаторов и отопительного оборудования – первостепенная необходимость. Поэтому рекомендуем сначала провести балансировку и только потом устанавливать автоматические системы, если будет желание.
Совет: учтите, что главным образом последние обладают централизованным характером, отвечая не за регулировку подачи теплоносителя, а за его температуру в отопительном устройстве.
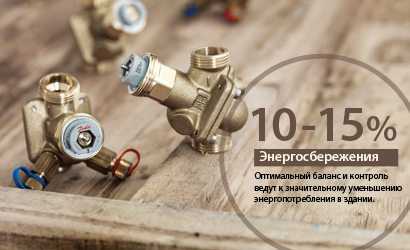
Балансировка систем отопления с помощью специальных вентилей сокращает расходы на топливо
Что для этого нужно
Балансировку выполняют с помощью следующих компонентов:
- регуляторов расхода;
- перепускных клапанов;
- балансировочных клапанов;
- регуляторов давления.
Рекомендуем вам покупать изделия только у проверенных временем производителей, даже когда их цена несколько выше остальных.
Монтаж определенных элементов базируется на устройстве системы отопления:
- в однотрубном контуре инструкция рекомендует только установить ручные краны, которые помогут варьировать интенсивностью подачи нагретой воды на любую комнату;
- в двухтрубных системах, особенно где температура регулируется автоматическими устройствами, не обойтись без монтажа балансировочных клапанов.
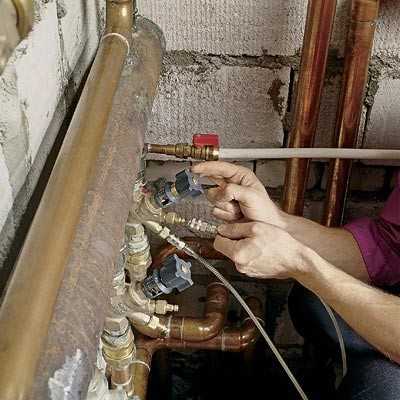
Как производится регулировка и настройка системы обогрева дома
Способы
Для выполнения процедуры есть несколько методов. Рассмотрим их суть на примере:
Простой | Самый трудоемкий вариант, когда периодически следует замерять показания каждого балансировочного клапана во время корректировки их положений. Цель — так подогнать положения клапанов, чтобы результат вас удовлетворил. |
Сложный | Считается более надежным, так как происходит разбивка системы на отдельные модули. В этом случае ее общую мощность принимают за 100%, а данные, которые приходят от отдельных модулей, превращают в соответствующие доли, к примеру, 50 или 20%.Потом проводят регулировку каждого модуля в отдельности, добиваясь интенсивности потока теплоносителя до нужного процентного показателя от общей мощности системы отопления. |
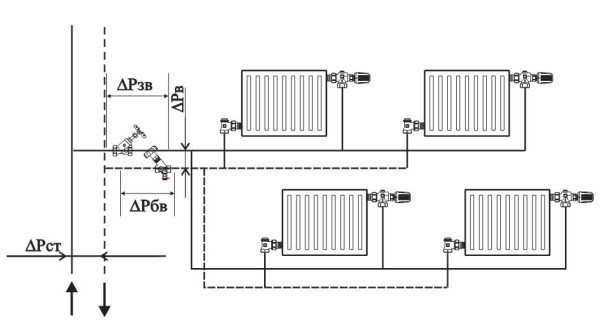
Регулировка баланса в двухтрубной схеме обогрева
Совет: перед началом балансировочных работ отопительной системы необходимо открыть каждый запорный кран и сделать тестовый запуск. Вы должны убедиться в правильности работы циркуляционного насоса для отопления, батарей и других компонентов схемы.
Балансировочный кран
Это вид запорной арматуры, с помощью которой происходит регулирование гидравлического сопротивления изменением диаметра сечения трубы на выбранном участке.
Устанавливать его необходимо, когда:
- отсутствует комфортная температура даже при максимальной нагрузке;
- происходит значительное изменение температуры в помещении при постоянной нагрузке в системе отопления;
- нет возможности выйти на номинальную мощность обогрева.
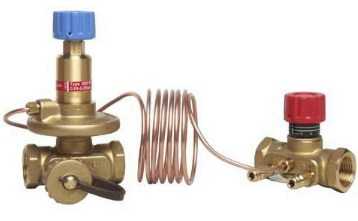
Автоматический балансировочный клапан перепуска Danfoss
Преимущества оборудования
Балансировочный клапан для отопления обладает следующими достоинствами:
- уменьшает общие расходы топлива, что через некоторое время заметят домовладельцы;
- увеличивает комфорт в помещении, так как удается добиться для каждой отдельной комнаты подходящего уровня температуры;
- убирает сложности при запуске системы.
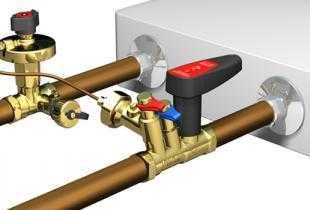
Подключение оборудования в систему обогрева
Установка и регулировка
Обычно монтаж балансировочных кранов для отопления производят для регулирования двухтрубных систем обогрева. Для этого используются специальные фитинги и адаптеры.
Совет: обращайте внимание на стрелку, выштампованную на корпусе устройства, так как есть краны, которые устанавливаются только в определенном направлении движения теплоносителя. В противном случае может произойти поломка оборудования и сбой в системе отопления.
После монтажа необходимо провести замеры, позволяющие определить уровень регулировки.
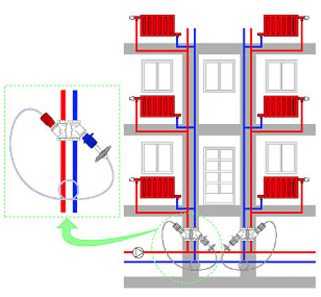
Установка балансировочного крана
Вывод
Для нормальной работы отопительной системы дома обязательно нужно проводить ее балансировку. Только в этом случае удастся равномерно обогреть здание целиком, установив в каждой комнате необходимую температуру. Эту работу помогают сделать специальное оборудование – балансировочные краны, которые позволяют отрегулировать функционирование системы отопления (см.также статью «Отопление бассейна: доступные методы и советы по самостоятельной реализации»).
Видео в статье даст возможность найти дополнительную информацию по вышеуказанной теме.
gidroguru.com
Гидравлическая балансировка системы отопления
Существуют цели и особенности балансировки отопительной системы. Гидравлическая балансировка системы отопления сама по себе является гидравлической увязкой, направленной на осуществление перераспределения тепла по всей замкнутой системе отопления.
Плохая эффективность функционирования работы отопительной системы часто обусловлена неправильным распределением в системе самого теплоносителя. Гидравлическая балансировка системы отопления преследует цель проверить установку балансировочных клапанов и правильность их установки, найти и устранить самые основные неполадки отопительной системы.
Когда расход теплоносителя недостаточный, температура помещения прогревается недостаточно, а когда происходит перерасход теплоносителя, то воздух прогревается избирательно. Современное устройство отопительных систем позволяет удовлетворять требования самых притязательных домовладельцев.
Практика показывает, что системы не всегда работают эффективно и безупречно, по этой причине в помещениях создаются некомфортные климатические условия.
Задачи балансировки
Главной целью балансировки является перераспределение расхода теплоносителя по замкнутым участкам, направляя тепло в места, где ощущается его дефицит. Данная процедура актуальна и уместна в помещениях любой площади, в том числе и частных домах, загородных дачах. Выполнить реконструкцию старой системы отопления сложно и дорого, поэтому в такой ситуации клиенты часто задаются вопросом как отбалансировать систему отопления.
Данная процедура осуществляется согласно государственной программе энергосбережения, в результате проведения отбалансировки значительно снижается потребление теплоносителей, уменьшаются денежные расходы за отопление.
Проблемы с работой системы отопления
Существует множество неполадок, возникающих в процессе эксплуатации отопительной системы:
- Присутствие воздуха, которое мешает или блокирует циркуляцию теплоносителя по системе. Иногда заказчики производят замену циркуляционных насосов на образцы, имеющие большую мощность.
- Поломки составляющих оборудования.
- Засорение фильтров.
Современные здания и сооружения требуют реконструкции отопительных систем, поскольку гидравлическая балансировка систем отопления обычно нарушена, что влечет увеличение расходов за отопление.
Чем раньше будет проведена балансировка отопительной системы, тем быстрей нормализуется отопительный процесс здания или помещения.
Проблемы работы системы обогрева устранимы только с привлечением специалистов, поскольку именно профессионалы смогут создать правильное распределение теплоотдачи теплового носителя.
Как выполняется гидравлическая балансировка системы отопления
Если система состоит из одной трубы, то данная процедура проходит просто и оперативно. В таком случае используется специальное приспособление, именно балансировочный кран в системе отопления позволяет равномерно и максимально рационально распределить тепло.
Балансировка двухтрубной системы отопления предусматривает дополнительный монтаж балансировочных клапанов, которые нужно установить в месте, где с двух сторон от них будет по 5 метров трубы. Когда клапан устанавливается после циркуляционного насоса, то расстояние до и после клапана должно составлять > 10 м.
Если данное условие будет нарушено, то выполнить точную регулировку будет невозможно по причине интенсивности вихревых потоков.
Диаметр трубопровода также должен соответствовать размеру балансировочного клапана.
Чтобы эффективность балансировки была максимальной, рекомендуется сделать ее разделение на отдельные составляющие, которыми могут быть автономные приборы или их группа. На входе отдельных модулей устанавливают балансировочный клапан, позволяющий настраивать работу каждого модуля. Такой подход будет уместен при необходимости получить разный уровень теплоотдачи приборов обогрева в различных помещениях.
Осуществление процедуры балансировки позволяет потреблять минимум энергии и достигать при этом максимум полезности. Данные работы должны осуществляться только силами высококвалифицированных специалистов.
Гидравлическая система, которая подлежала балансировке, экономит энергию до 6 %, защищает окружающую среду от больших объемов выбросов в атмосферу углекислого газа, защищает помещение от шумов и перегревов.
В условиях тотальной экономии коммунальных услуг гидравлическая балансировка актуальна, востребована и необходима.
dompraktika.ru
Основы балансировки роторов, неуровновешенность, дисбаланс
ДИНАМИЧЕСКАЯ БАЛАНСИРОВКА РОТОРОВ НА СТАНКЕ С КАЧАЮЩЕЙСЯ РАМОЙ
Балансировка роторов – это процедура, необходимая, если вращающаяся часть машины не уравновешена. В этом случае, при вращении появляется сотрясение (вибрация) всей машины. В свою очередь, это может привести к разрушению подшипников, фундамента и, впоследствии, самой машины. Чтобы избежать этого, все вращающиеся части должны быть отбалансированы.
Сам по себе ротор — это вращающаяся деталь, удерживающаяся при вращении с помощью несущих поверхностей в опорах (цапфы и др.). Осью ротора является прямая, соединяющая центры тяжести контуров на поперечных сечениях центра несущих поверхностей. Различают детали нескольких видов:
• двухопорные;
• многоопорные;
• межопорные;
• консольные;
• двухконсольные.
Различают балансировку роторов статическую и динамическую. Первая выполняется на призмах, вторая при вращении балансируемой детали.
Специалисты компании «КарданБаланс» предлагают услуги по качественной балансировке ротора. Наши центры оснащены современным оборудованием, гарантирующем точность балансировки. Этого добиться достаточно сложно, ведь она должна полностью совпадать с точностью изготовления ротора. Все работы осуществляются на стендах собственной разработки, которые дают точность балансировки, впятеро превышающую заводские требования!
В данном разделе вы сможете ознакомиться с основной технической информацией относительно способов динамической балансировки ротора (способ исключений, метод Б.В.Шитикова). Полезный практический материал, который даст основное представление о проблеме. Что такое гидравлическая балансировка, что из себя представляет станок для балансировки колес и другая информация понятно изложена на нашем ресурсе. Также Вы сможете воспользоваться нашими услугами, которые включают ремонт карданов, балансировку грузовых колес, коленчатого вала и пр. Сколько стоит балансировка и другие работы описано в разделе «Услуги и цены».
Содержание
- Введение. Основные понятия.
- Неуравновешенность ротора и ее проявление
- Балансировка ротора способом исключений
- Балансировка ротора способом Б.В. Шитикова
- Заключение
- Список литературы
1. ВВЕДЕНИЕ. ОСНОВНЫЕ ПОНЯТИЯ
При вращении m (массы) вокруг точки (неподвижной) с w (угловая скорость) F (центробежная сила инерции) этой массы:
(1.1)
где аn – нормальное ускорение массы;
– расстояние от оси вращения до центра массы.
При перемещении массы F будет изменять направление и оказывать воздействие (вибрационное) на опоры и через них на конструкции, прикрепленные к стойке. D (дисбаланс) – векторная величина, которая равна произведению неуравновешенной массы на эксцентриситет (радиус-вектор центра массы). Величина измеряется в гр/мм.
Причем векторы «D» и «е» коллинеарные величины.
В векторном виде формула имеет следующий вид:
Пропорциональными друг другу оказываются векторы F и D.
2. НЕУРАВНОВЕШЕННОСТЬ РОТОРА И ЕЕ ПРОЯВЛЕНИЕ
По ГОСТ 19534-74, ротор – тело, при вращении удерживаемое в опорах своими несущими поверхностями. В автомобилях это может быть зубчатое колесо, шкив, ротор электродвигателя, барабан, коленчатый вал и т.д.Если массы распределены в роторе так, что во время вращения они вызывают нагрузки в опорах, то его называют неуравновешенным. Причем различают 3 типа неуравновешенности ротора:
- Статическую. При которой ось вращения и главная ось инерции параллельны. При этом переменные давления равны 0
- Динамическую. При которой главная ось и ось вращения перекрещиваются или пересекаются, но не в центре масс, из-за этого и возникает разбалансированность чаще всего.
- Моментную
Во всех случаях неуравновешенности ротора, силы инерции его масс создают динамические нагрузки. Устраняются они перераспределением масс (установкой противовесов).
Динамическая балансировка осуществляется с помощью специального станка, оснащенного качающейся рамой
3. Балансировка ротора способом исключений
Для того, чтобы определить параметры массы (корректирующей) в плоскости П, ротор устанавливают на станке и назначают эксцентриситет массы. В плоскости намечается окружность, причем ее центр должен совпадать с геометрической осью вращения. Радиус принимают равным выбранному эксцентриситету. Окружность делится на 4 части. Мастику (пластилин) прикрепляем так, чтобы центр кусочка совпал с точкой 1. Приведем ротор во вращение и измерим амплитуда колебаний. Показатель записываем возле точки 1.
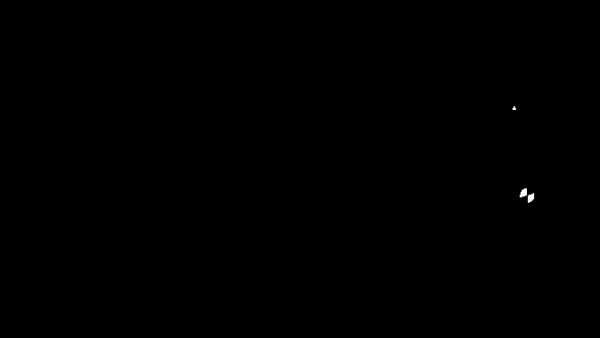
Переносим мастику в точку 2, разгоняем ротор и опять фиксируем его амплитуду. Записываем ее. Фиксируем остальные 2 точки.
Сравниваем амплитуды до тех пор, пока они не окажутся наименьшими. Точка К, найденная нами, определяет конечное положение массы корректирующей. Противоположная точка H – неуравновешенная масса.
Теперь начинаем менять массу мастики на точки K и измерять колебания ротора. Так мы найдем величину корректирующей массы.
4. БАЛАНСИРОВКА РОТОРА СПОСОБОМ Б.В. ШИТИКОВА
Установим ротор на раму и разгоним его. После это зафиксируем амплитуду A1.
В точку П1 установим дополнительную массу mg с эксцентриситетом eg. При резонансе фиксируем амплитуду AS.
Переставляем массу в противоположную точку и фиксируем вторую амплитуду. Обозначаем точки на плоскости в соответствии с неравенством, при котором первая амплитуда больше второй.
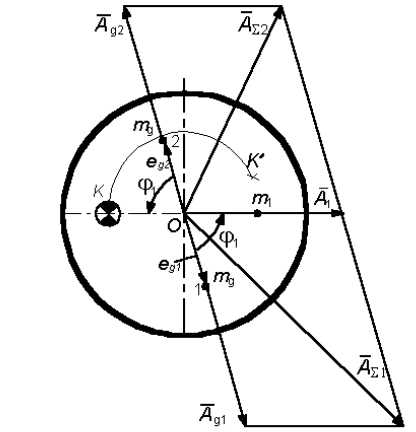
По 3-м амплитудам строим параллелограмм и находим четвертую амплитуду и угол
1Используя формулу, определяем коэффициент пропорциональности массы
m = Аg /Dg=Аg/(mgeg),Определяем дисбаланс масс
Dк=D1 ек=D1/mк.
Осталось определить точки установки грузов и пробными пусками определить остаточную амплитуду, а также оценить качество уравновешивания в плоскости.
Doct=Aoct/m
В компании «КарданБаланс» вы можете купить карданный вал Шевроле Нива, карданный вал УАЗ, карданный вал Мерседес Вито, а также комплектующие для других автомобилей. Мы осуществляем не только продажу запчастей, но и их последующую установку.
www.kardanbalans.ru
ГИДРАВЛИЧЕСКАЯ БАЛАНСИРОВКА СИСТЕМ
Гидравлика систем отопления и охлаждения
10.1. Обшие сведения
Основной целью проектирования систем обеспечения микроклимата является создание теплового комфорта в помещении при минимуме потребления энергоресурсов. Теоретически данная задача является достижимой. Практически сегодня делается все возможное для ее реализации. Современное оборудование приближается к идеальным характеристикам, позволяющим добиться эффективного результата. Однако в действительности даже самые современные системы не всегда справляются с этой задачей. У 80 % систем причиной является несоответствие распределения потоков воды [42].
Несоответствию способствуют многие факторы, содержащиеся в допущениях методик расчета, погрешностях монтажа систем, несоблюдении эксплуатационных требований. В результате происходит перераспределение потоков по реальным гидравлическим сопротивлениям циркуляционных колец, что приводит к необеспеченности теплового комфорта в помещениях из-за недостатка потока в одних циркуляционных контурах и его избытка в других, возникновению шума, перерасходу энергоресурсов, поэтому перед сдачей объекта в эксплуатацию необходимо вывести систему в рабочий режим с помощью балансировки клапанов.
Одним из допущений методик гидравлического расчета является то, что системы с переменным гидравлическим режимом рассматривают аналогично системам с постоянным гидравлическим режимом. При этом гидравлическое сопротивление элементов системы принимают постоянным, в то время как оно изменяется в широких пределах. В системах с переменным гидравлическим режимом дополнительным требованием, которое должно войти в практику проектирования, является создание условий для эффективной работы всех элементов системы. Для клапанов — распределение потоков, для системы обеспечения микроклимата в целом — линейность регулирования тепловым потоком теплообменных приборов.
До осуществления наладки системы необходимо провести подготовительные работы: ознакомиться с проектной документацией, техническими инструкциями на клапаны, приборы и пр. Далее проверяют исправность элементов системы, их работоспособность и функционирование, правильность монтажа. Затем производят балансировку системы.
Гораздо сложнее производить подготовительные работы в модернизируемых системах. В этом случае, как правило, заново определяют теплопотери помещений и осуществляют гидравлический расчет на ос – новании собранных исходных данных. Их точность и старательность выполнения расчетов значительно облегчают последующую балансировку системы.
Перед балансировкой системы производят испытание на герметичность, промывают, прочищают фильтры, деаэрируют, выводят в рабочий гидростатический режим. Все термостатические клапаны устанавливают в максимально открытое положение (только так можно определить перегревы и недогревы помещений). Для этого колпачок термостатического клапана не должен упираться в шток. Колпачками защищают шток от царапин, попадания пыли, деформации. Замену колпачков на термостатические регуляторы осуществляют по окончании балансировки системы.
Перед балансировкой системы следует проанализировать ее работоспособность и определить частные признаки и общие закономерности несоответствия требуемым температурным условиям в помещениях. К частным признакам относят перегрев или недогрев отдельных помещений. К общим закономерностям — перегрев или недогрев этажей, помещений, расположенных по различным фасадам здания, стояков и т. д.
Если рассматривать систему отопления, то при недогреве отдельных помещений вначале следует определить, не является ли это следствием засорения или некачественного монтажа, например, образования внутреннего грата (наплыв, уменьшающий проходное сечение трубопровода) при термическом соединении труб с фитингами. Как правило, закупорка образовывается в местных сопротивлениях: фитингах, клапанах и т. д. Выявляют ее на ощупь или термометром прибора PFM 3000 до и после местного сопротивления по изменению температуры трубопровода. Если температура не изменяется, значит необходимо производить балансировку.
Перегрев отдельных помещений может быть вызван только гидравлической разбалансировкой, причем в перегретых помещениях она значительно больше, чем в недогретых (см. рис. 6.7).
Общие закономерности несоответствия температурным условиям в помещении разделяют на эксплуатационные и предэксплуатационные.
Эксплуатационная разбалансировка вызвана качественным регулированием системы отопления на протяжении отопительного периода. Если недостаточен авторитет теплоты помещения, то изменение гравитационного давления теплоносителя приводит к недогреву нижних этажей во время морозов. Во время оттепелей происходит недогрев верхних этажей. Перегревы соответственно верхних и нижних этажей устраняются терморегуляторами. Не следует допускать эксплуатационную разбалансировку при выборе и обосновании проектных решений системы обеспечения микроклимата. Для этого уменьшают расчетный перепад температур теплоносителя с увеличением этажности здания; рассматривают работоспособность системы при минимальном и максимальном перепадах температур теплоносителя; устанавливают регуляторы перепада давления в горизонтальных системах на поэтажных (поквартирных) приборных ветках; устанавливают на каждом теплообменном приборе стабилизаторы расхода или регуляторы перепада давления в вертикальных системах.
Предэксплуатационные общие закономерности следует, прежде всего, попытаться устранить регулированием производительности насоса и температуры теплоносителя. Общие рекомендации приведены в табл. 10.1 [43]. ‘
Таблица 10.1. Устранение поэтажной разбалансировки системы
|
В горизонтальных системах устраняют поэтажную разбалансировку также настройкой регулирующих клапанов на приборных ветках.
Если во всех помещениях нет общей закономерности несоответствия тепловым условиям, то следует производить балансировку системы. Для ее реализации выбирают способ, который зависит от типа применяемых регуляторов: прямого или непрямого действия. При этом процесс балансировки должен быть дешевым, быстрым и отвечать техническим требованиям.
В основе методов балансировки систем с терморегуляторами прямого действия применяют два подхода. Первый осуществляют в несколько этапов. Он заключается в последовательном устранении дисбаланса по отдельным циркуляционным кольцам, начиная с основного (наиболее удаленного и нагруженного) кольца. Пройдя первый этап, его повторяют до достижения проектного потокораспределения во всех циркуляционных кольцах. Второй осуществляют в один этап. Его реализуют при компенсационном методе балансировки [20]. В системах с терморегуляторами прямого действия широкое распространение получили методы:
• температурного перепада;
• предварительной настройки клапанов;
• пропорциональный;
• компенсационный;
• компьютерный.
Настройку автоматических терморегуляторов непрямого действия (электронных) осуществляют:
• статически;
• динамически.
Указанные способы и методы настройки клапанов достаточно подробно рассмотрены в литературе [20; 44; 45; 55]. Остановимся лишь на особенностях и возможностях, которые возникли в последнее время благодаря применению современного оборудования и новых подходов в подборе клапанов и теплообменных приборов.
Наладка системы обеспечения микроклимата ручными балансировочными клапанами является длительной и дорогостоящей процедурой. Этот процесс значительно упрощается и удешевляется при применении в системе автоматических балансировочных клапанов (регуляторов перепада давления, регуляторов расхода, стабилизаторов расхода и т. п.) вместо ручных балансировочных клапанов.
10.2. Метод температурного перепада
Метод основан на уравнении (2.2), смысл которого заключается в том, что в сбалансированной системе разность температур теплоносителя At на входе и выходе всех теплообменных приборов должна быть одинаковой. При несоответствующих потоках теплоносителя она
изменяется. Принято считать, что отопительные приборы достигают проектного режима лишь при номинальном потоке. Недостаточный поток теплоносителя уменьшает теплоотдачу прибора, а чрезмерный поток не приводит к ее существенному увеличению (см. рис. 6.7), при этом разницу температур теплоносителя принимают по расчетному значению (уравнение (2.2)). В то же время не учитывают, что тепловой прибор выбирают по завышенным в 1,15(1,1) раза теплопотерям помещения (см. п. р. 6.3). Разница температур At’ теплоносителя при этом будет выше At, т. к. расход теплоносителя уменьшится, поэтому разницу температур следует определять с учетом завышенного типоразмера теплообменного прибора.
Рис. 10.1. Определение требуемого перепада температур теплоносителя в отопительном приборе |
Находят разницу температур геометрическим построением, показанным на рис. 10.1. Сплошная линия характеризует изменение температуры подаваемого в отопительный прибор теплоносителя. Пунктирная — расчетную температуру теплоносителя на выходе прибора. Штрих – пунктирная — требуемую температуру теплоносителя на выходе прибора с завышенной поверхностью теплообмена. На оси абсцисс дан диапазон изменения температуры наружного воздуха С
iext. Он начинается с расчетной наружной температуры воздуха для системы отопления (например, минус 20 °С) и заканчивается температурой, совпадающей с нормативной температурой воздуха в помещении (например, 20 °С). На оси ординат дан диапазон изменения температуры теплоносителя на входе в отопительный прибор и выходе из него. Температуру теплоносителя на входе в отопительный прибор принимают, как правило, равной температуре на выходе из источника теплоты, например, 90 °С (из котла). Для более точного расчета следует учитывать остывание теплоносителя в трубопроводах. Температуру в обратном трубопроводе, например, 68 °С, определяют из среднего перепада температур между прибором (с учетом завышенного типоразмера) и воздухом в уравнении (6.1).
При расчетной температуре наружного воздуха перепад температур теплоносителя примерно равен At’ = 22 °С. Когда совпадает температура
воздуха снаружи и внутри помещения, т. е. равна 20 °С, перепад температур At’ = 0. Промежуточные значения At’ определяют по пропорции. Например, при text= 0 °С, соответствующей 50 % рассматриваемого диапазона изменения внешних температур, At’ = 11 °С и также составляет 50 % от максимального перепада температур теплоносителя.
Балансировку осуществляют до требуемого перепада температур теплоносителя настройкой дросселя терморегулятора либо регулирующего клапана в узле обвязки теплообменного прибора. Термостатический клапан в это время должен быть полностью открыт (со свободно накрученным колпачком). Следовательно, влияние завышенного теплового потока теплообменного прибора устраняется уменьшением расхода теплоносителя посредством увеличения сопротивления дросселя терморегулятора либо регулирующего клапана. В том и в другом случае ухудшается потокораспределение терморегулятора и, следовательно, авторитет теплоты помещения. Процедура достижения равенства температур на всех теплообменных приборах может повторяться несколько раз до достижения сбалансированности системы, т. к. настройка каждого прибора отражается на характеристиках всех остальных, даже отрегулированных приборов.
Данный метод балансировки очень не точен, особенно в системах с низкими перепадами температур, каковыми являются системы охлаждения с фенкойлами либо потолочными панелями, системы отопления в полу… Из-за тепловой инерции системы и здания процедура балансировки требует значительного времени. Кроме того, необходимо обеспечить стационарные температурные условия как внутри помещения, так и снаружи, поэтому метод температурного перепада применяют для балансировки небольших систем отопления при безветренной и несолнечной погоде. Чем ниже температура наружного воздуха, тем точнее результат.
Несмотря на все недостатки, данный метод является единственно возможным для балансировки теплообменных приборов в пределах стояка либо приборной ветки, если в узлах обвязки этих приборов отсутствуют регулирующие клапаны со штуцерами для отбора импульсов давления теплоносителя. Задача значительно упрощается при наличии таких клапанов. Тогда применяют пропорциональный либо компенсационный метод балансировки. С автоматическим регулятором перепада давления на стояке либо приборной ветке настройку теплообменных приборов осуществляют также упрощенным методом предварительной настройки клапанов. В этом случае предполагают, что все автоматически поддерживаемое давление теряется в терморегуляторе, т. е. пренебрегают потерями давления в трубопроводах и теплообменном приборе. Положение настройки дросселя подбирают по пропускной способности терморегулятора, определяемой уравнением в табл. 3.1, где перепад давления принимают равным автоматически поддерживаемому регулятором перепаду.
B методе температурного перепада следует учитывать влияние завышенного типоразмера теплообменного прибора на изменение температуры в обратном трубопроводе.
Технология отопления помещений «теплый пол» известна миру еще со времен Древнего Рима. Некоторое время ее даже пытались внедрить при СССР, однако тогда на просторах нашей страны она не прижилась. Сегодня …
Теплые полы Тепло и уют в доме – это залог здоровья и благополучия всех его жителей. На сегодня далеко не все центральные системы обогрева способны обеспечить в помещениях различного типа …
Экономический эффект от применения автоматизированных систем обеспечения микроклимата определяют технико-экономическим сопоставлением различных проектных решений [10; 46; 47]. При этом сравнивают капитальные и эксплуатационные расходы, сроки монтажа и эксплуатации систем. Рассчитывают …
msd.com.ua
4. Методика статической и динамической балансировки деталей машин.
Неуравновешенность любой вращающейся детали тепловоза может возникнуть как в процессе эксплуатации вследствие неравномерного износа, изгиба, скопления загрязнений в каком-либо одном месте, при утере балансировочного груза, так и в процессе ремонта из-за неправильной обработки детали (смещения оси вращения) или неточной центровки валов. Для уравновешивания деталей их подвергают балансировке. Существуют два вида балансировки: статическая и динамическая.
Рис. 5.1. Схема статического уравновешивания деталей: тх — масса неуравновешенной детали; т2 — масса уравновешивающего груза; г,, г2 — их расстояния от оси вращения
Статическая балансировка. У неуравновешенной детали ее масса располагается несимметрично относительно оси вращения. Поэтому при статическом положении такой детали, т. е. когда она находится в покое, центр тяжести будет стремиться занять нижнее положение (рис. 5.1). Для уравновешивания детали добавляют с диаметрально противоположной стороны груз массой т2 с таким расчетом, чтобы его момент т2г2 был равен моменту неуравновешенной массы т^. При этом условии деталь будет находиться в равновесии при любом положении, так как центр тяжести ее будет лежать на оси вращения. Равновесие может быть достигнуто также путем удаления части металла детали высверловкой, спиливанием или фрезерованием со стороны неуравновешенной массы тх. На чертежах деталей и в Правилах ремонта на балансировку деталей дается допуск, который называют дисбалансом (г/см).
Статической балансировке подвергают плоские детали, имеющие небольшое отношение длины к диаметру: зубчатое колесо тягового редуктора, крыльчатку вентилятора холодильника и т.п. Статическая балансировка ведется на горизонтально-параллельных призмах, цилиндрических стержнях или на роликовых опорах. Поверхности призм, стержней и роликов должны быть тщательно обработаны. Точность статической балансировки во многом зависит от состояния поверхностей этих деталей.
Рис. 5.2. Схема динамического уравновешивания деталей:
т — масса ротора; ти т2 — неуравновешенные, приведенные к плоскостям массы ротора; М — масса уравновешивающего груза; Рг — неуравновешенные центробежные силы; Ри Р2 — уравновешивающие центробежные силы; /,, /2 — плечи указанных сил
Рис. 5.3. Схема балансировочного станка консольного типа:
1 — пружина; 2 — индикатор; 3 якорь; 4 — рама; 5 — опора станка; 6 — опора станины; /, II— плоскости
Динамическая балансировка. Динамической балансировке обычно подвергают детали, длина которых равна или больше их диаметра. На рис. 5.2 показан статически отбалансированный ротор, у которого масса т уравновешена грузом массой М. Этот ротор при медленном вращении будет находить ся в равновесии в любом положении. Однако при быстром его вращении возникнут две равные, но противоположно направленные центробежные силы Fx и F2. При этом образуется момент FJU который стремится повернуть ось ротора на некоторый угол вокруг его центра тяжести, т.е. наблюдается динамическое неравновесие ротора со всеми вытекающими отсюда последствиями (вибрация, неравномерный износ и т. п.). Момент этой пары сил может быть уравновешен только другой парой сил, действующей в той же плоскости и создающей равный противодействующий момент. Для этого в нашем примере нужно приложить к ротору в той же плоскости (вертикальной) два груза массами Шх = т2 на равном расстоянии от оси вращения. Грузы и их расстояния от оси вращения подбирают так, чтобы центробежные силы от этих грузов создавали момент /уь противодействующий моменту FJi и уравновешивающий его. Чаще всего уравновешивающие грузы прикрепляют к торцовым плоскостям деталей или с этих плоскостей удаляют часть металла.
При ремонте тепловозов динамической балансировке подвергают такие быстровращающиеся детали, как ротор турбокомпрессора, якорь тягового электродвигателя или другой электрической машины, рабочее колесо воздуходувки в сборе с приводной шестерней, вал водяного насоса в сборе с крыльчаткой и зубчатым колесом, карданные валы привода силовых механизмов.
Динамическое уравновешивание ведется на балансировочных станках. Принципиальная схема такого станка консольного типа показана на рис. 5.3. Балансировка, например, якоря тягового электродвигателя ведется в таком порядке. Якорь J укладывают на опоры качающейся рамы 4. Рама одной точкой упирается на опору станка 5, а другой на пружину 1. При вращении якоря неуравновешенная масса любого его участка (кроме масс, лежащих в плоскости II — II) вызывает качание рамы. Амплитуда колебания рамы фиксируется индикатором 2. Чтобы уравновесить якорь в плоскости / — I, к его торцу со стороны коллектора (к нажимному конусу) прикрепляют поочередно различные по массе пробные грузы и добиваются прекращения колебания рамы или его уменьшения до допускаемой величины. Затем якорь переворачивают так, чтобы плоскость /— /проходила через неподвижную опору станины 6, и повторяют те же операции для плоскости II— II. В этом случае балансировочный груз прикрепляют к задней нажимной шайбе якоря.
5. Междисциплинарное задание № 18.
Утверждены на заседании КМСХ « 18 » ноября 2013 г.
Директор ИСХПР А. М. Козина
Зав. КМСХ С. В. Карташов
studfiles.net
Способ балансировки рабочего колеса гидравлической турбины
Изобретение относится к измерительной технике и может быть использовано для определения координат центра масс и балансировки изделий сложной формы. Способ включает центрирование колеса с установлением точек отсчета координат местонахождения силоизмерительных датчиков, размещенных на поверхности платформ, используемых для взвешивания рабочего колеса. При этом обеспечивают приложение нагрузки к центру каждой платформы с помощью силовводящего узла для каждого диапазона веса рабочего колеса. После этого выбирают по методу суперпозиции на поверхности колеса характеристические точки, соответствующие проекциям центров весоизмерительных платформ и осуществляют поворот рабочего колеса по часовой стрелке относительно упомянутых платформ на заданный угол. Затем выполняют после каждого поворота колеса измерение веса на каждой платформе с каждой выбранной одноименной характеристической точкой с последующим арифметическим усреднением результатов измерений по всем платформам в каждой одноименной характеристической точке. Затем определяют известным образом расчетным путем с использованием системы измерений и обработки результатов дисбаланс и точно устанавливают балансировочные грузы. Технический результат заключается в повышении точности балансировки рабочего колеса гидравлической турбины с одновременным упрощением расчета процесса ее балансировки. 6 з.п. ф-лы, 11 ил.
Изобретение относится к гидромашиностроению, точной механике, измерительной технике и может быть использовано для определения координат центра масс и балансировки изделий сложной формы.
Для устранения неуравновешенности рабочего колеса гидравлической турбины во всех случаях применяют различные методы технологической балансировки, которые, однако, не обеспечивают должного уровня точности из-за наличия имеющихся погрешностей, как при выполнении измерений, так и обусловленных точностью изготовления оборудования, с помощью которого осуществляют эти измерения.
Так известен способ балансировки гидроагрегата, который выполняют следующим образом. Гидроагрегат центрируют в направляющих сегментных подшипниках, устанавливают под его ободом динамометры, разводят сегменты подшипников, опускают обод на динамометры и по их показаниям определяют величину дисбаланса из следующих соотношений:
S=(∑i=1nPi⋅Xi)2+(∑i=1nPi⋅Yi)2; ϕ=arctg∑i=1nPi⋅Xi∑i=1nPi⋅Yi;
где S – статический момент неуравновешанной массы;
Pi – усилие, действующее на i-динамометр;
n – число динамометров;
Xi и Yi – координаты установки динамометров;
φ – угол, показывающий направление смещения центра масс.
После этого устраняют дисбаланс путем установки балансировочного груза, статический момент которого равен S, а угол установки составляет
ϕ2=ϕ+π (см. Авторское свидетельство СССР №1150391, F03B 11/04, опубл. 15.04.85, бюл. №14).
Основными недостатками данного технического решения являются низкая производительность и большая погрешность измерений, вызванная наличием субъективизма в оценке вектора и величины дисбаланса колеса, обусловленная отсутствием автоматизации установки, расчета параметров и контроля за ходом балансировки.
Известен также и способ балансировки рабочего колеса гидравлической турбины, который характеризуется тем, что центрирование колеса осуществляют по боковой поверхности внешней стенки обода с помощью подпружиненного визирного керна и упоров в виде призм, жестко установленных на рабочей поверхности платформы с силоизмерительными датчиками и образующих в точках касания боковой поверхности колеса реперные точки отсчета координат местоположения силоизмерительных датчиков. При этом все силоизмерительные датчики, а соответственно и рабочие поверхности платформ выставляют в один уровень горизонта. После этого производят нагружение платформ балансируемым колесом, фиксируют его положение видеокамерой верхнего обзора, вводят полученное изображение в компьютер системы измерения и обработки результатов и с использованием этой системы, включающей преобразователи сигналов и контроллер, определяют координаты и значение нагрузки, приходящейся на каждую платформу. На основе этих полученных результатов определяют аналогично центр масс всего колеса, а полученные координаты центра масс накладывают на компьютерное изображение контура рабочего колеса, определяют дисбаланс и точно устанавливают балансировочные грузы. Способ характеризуется и тем, что систему измерений и обработки их результатов образуют из преобразователей сигналов по количеству силоизмерительных датчиков, подключенных к контроллеру, соединенному с компьютером. В качестве силоизмерительных датчиков используют тензометрические датчики, а все силоизмерительные датчики координатно группируют на поверхности платформы по диапазону измерения массы рабочего колеса, располагая их по номиналу измерения в вершинах квадратов, смещенных относительно друг друга (см. Патент РФ №2456566, G01M 1/12, опубл. 20.07.2012 г., бюл. №20).
Указанное изобретение по решаемой задаче и достигаемому техническому результату является наиболее близким аналогом к заявляемому способу и принято в качестве прототипа.
Однако всем аналогичным способам балансировки крупногабаритных и большегрузных изделий с использованием платформ с датчиками, в том числе и ближайшему аналогу, свойственны следующие недостатки, приобретаемые и установленные в процессе производственной эксплуатации.
Прежде всего имеет место перегрузка отдельных датчиков по весовым платформам из-за неравномерного выставления верхних опор датчиков всех платформ; влияние разновысотности платформ, а также влияние наклона или прогиба поверхности рабочего стола на результаты балансировки. На результаты балансировки при определенных условиях может оказать влияние и отсутствие учета несплошностей рабочих колес при количестве лопастей, некратном количеству весоизмерительных платформ и вследствие этого – появление дополнительной «мнимой» несбалансированной массы.
Решить задачу по устранению недостатков аналога стало возможным за счет изменения схемы нагружения весоизмерительных платформ и применения метода суперпозиции с обеспечением инвариантности системы относительно неравномерности установки стола, платформ и наличия несплошностей рабочих колес гидротурбин.
Технический результат – повышение точности балансировки достигается за счет того, что производят первоначально центрирование колеса с установлением точек отсчета координат местонахождения силоизмерительных датчиков, размещенных на поверхности платформ, используемых для взвешивания рабочего колеса. При этом обеспечивают приложение нагрузки к центру каждой платформы с помощью силовводящего узла для каждого диапазона веса рабочего колеса. После этого выбирают по методу суперпозиции на поверхности колеса характеристические точки, соответствующие проекциям центров весоизмерительных платформ и осуществляют поворот рабочего колеса по часовой стрелке относительно упомянутых платформ на заданный угол. Затем после каждого его поворота выполняют измерение веса на каждой платформе с каждой выбранной одноименной характеристической точкой с последующим арифметическим усреднением результатов измерений по всем платформам в каждой одноименной характеристической точке и общего веса рабочего колеса также в каждой одноименной характеристической точке, после чего определяют известным образом расчетным путем с использованием системы измерений и обработки результатов дисбаланс и точно устанавливают балансировочные грузы.
Способ также характеризуется и тем, что центрирование рабочего колеса гидравлической турбины проводят по боковой поверхности внешней стенки обода с помощью подпружиненного визирного керна и упоров в виде призм, жестко установленных на рабочей поверхности платформ с силоизмерительными датчиками. На точность балансировки оказывает влияние и то, что силовводящий узел выполняют в виде полусферической формы упора, установленного точно в центр платформы. Также способствует повышению точности балансировки рабочего колеса и система измерений и обработки их результатов, которую образуют из контроллера, преобразователей сигналов, связанных каждый своим входом с выходом силоизмерительных датчиков и подключенных к контроллеру, соединенному с компьютером, а в качестве силоизмерительных датчиков используют тензометрические датчики.
Способ балансировки рабочего колеса характеризуется еще и тем, что отцентрированное рабочее колесо гидротурбины фиксируют видеокамерой и вводят его изображение в компьютер системы измерения и обработки результатов и после определения вектора и центра масс всего колеса накладывают их на компьютерное изображение. Важным требованием для реализации способа балансировки является и то, что угол установки весоизмерительных платформ и угол поворота характеристических точек, выбранных на рабочем колесе, принимают равным 120°, а количество платформ равно трем.
Способ балансировки рабочего колеса гидравлической турбины является новым, поскольку в источниках информации совокупность предложенных признаков, отраженных в формуле изобретения, в том числе и в дополнительных пунктах, не обнаружена.
Предложенный способ как техническое решение обладает изобретательским уровнем, т.к. совокупность и последовательность его действий, выполняемых с использованием метода суперпозиции с обеспечением инвариантности системы относительно неровности установки стола, платформы и наличия несплошностей рабочих колес гидротурбин, в области гидромашиностроения не являются очевидными.
Изобретение проиллюстрировано чертежами, где на фиг.1 изображена схема установки рабочего колеса в сборе на позиции его балансировки, на фиг.2 показана платформа в сборе с силоизмерительным датчиками, упорами и визирным керном (вид сверху), на фиг.3 показан разрез по А-А на фиг.2. На фиг.4 проиллюстрирован вид платформы сверху с силоизмерительными датчиками, разнесенными по квадратам и силовводящим устройством, на фиг.5 показан вид платформы сбоку с вырывом, где установлен силовводящий узел, на фиг.6 изображен общий вид размещения рабочего колеса на платформах под углом α=120° с выбранными характеристическими точками, а на фиг.7,8 и 9 показаны схемы поворота рабочего колеса на угол 120° в различных положениях одноименных характеристических точек и на фиг.10 условно показано положение центра масс рабочего колеса, радиус и величина дисбаланса относительно осей X и Y.
Комплект для ориентированного балансирования рабочего колеса гидравлической турбины включает платформы 1 с силоизмерительными датчиками 2 и 3, видеокамеру 4 верхнего обзора и систему измерения и обработки их результатов, включающую преобразователи сигналов (на фиг. не показаны) каждого силоизмерительного датчика 2 и 3, подключенные к контроллеру 5, соединенному с компьютером 6. Платформы 1 выполнены квадратной формы с угловыми скосами 7, преимущественно под углом 45° и применительно к этой форме выбраны соответствующие схемы размещения на их рабочих поверхностях 8 силоизмерительных датчиков 2 малого веса (3 т) и датчиков 3 большого веса (15 т). Размещение силоизмерительных датчиков 2 и 3 сориентировано по осям Х и Y относительно угловых стыков 9 скосов 7 и каждый их вид графически расположен в вершинах своего квадрата 10.
В технических средствах, используемых для балансировки, в том числе и для платформ 1 применяются схемы размещения силоизмерительных датчиков 2 и 3, приведенные на фиг.4.
Схема расположения силоизмерительных датчиков 2 на малом диапазоне измерения с наибольшим пределом измерения (НПИ) 3 т имеет наклон к оси Y, а схема расположения силоизмерительных датчиков 3 большого диапазона измерения с НПИ 15 т наоборот отклонена от оси Y (фиг.4).
Таким образом, силоизмерительные датчики 2 и 3 группируют на платформе 1 по диапазону измерения массы колеса, графически располагая их для удобства применения по номиналу измерения в вершинах квадратов 10, смещенных относительно друг друга. Конструкция самой платформы 1 включает нижнее основание 11, на котором установлены датчики 2 и 3, механизм регулирования опоры 12 и закрывающее их верхнее основание 13. Регулируя механизм опоры 12 датчиков 2 и 3, выравнивают платформу в горизонтальный уровень для любого диапазона измерения веса рабочего колеса гидравлической турбины (фиг.3).
Для ориентированной установки платформы 1 относительно рабочего колеса на ее рабочей поверхности 8 верхнего основания 13 жестко координатно установлены два упора 14 и подпружиненный визирный керн 15, образующие в точках касания боковой поверхности 16 и обода 17 рабочего колеса реперные точки a, b, c и f отсчета координат месторасположения силоизмерительных датчиков 2 и 3. Упоры 14, выполненные в виде призм, и визирный керн 15 неподвижно связаны между собой планкой 18.
На рабочей поверхности 8 всех платформ 1 проведены визирные линии 19, 20 и 21, и на боковой поверхности 16 обода 17 также выполнена разметка этих линий, которая наносится в виде вертикальных рисок 19, 20 и 21, размещенных равноудаленно друг от друга на угол α=120°.
Для обеспечения равномерной нагрузки датчиков 2 и 3 рабочая поверхность 8 каждой платформы 1 снабжена силовводящим узлом 22, выполненным в виде упора полусферической формы, установленным точно в центр платформы.
Каждая платформа 1 юстируется таким образом, чтобы размеры между реперными точками a, b, c и f, образуемыми концами упоров 14 и подпружиненного керна 15, были постоянными и равными для всех платформ 1, а выдвижной визирный керн 15 располагался по любой линии визирования, нанесенной на боковой поверхности обода и рабочей поверхности 8 верхнего основания 13. Разметка и установка упоров 14 проводится относительно датчиков 2 и 3 на всех платформах 1 одинаково, образуя единую систему координат относительно осей X и Y.
В платформах 1 для работы на первом или втором диапазонах используют соответственно группу датчиков 2 или 3. Настройка на диапазон (15 или 50 т) осуществляется путем выведения из соприкосновения верхних опор механизма регулирования 12 одних датчиков и заменой их другими, при этом обеспечивается одинаковый сигнал по каждому датчику.
Конструкция платформ 1 такова, что каждый из датчиков 2 или 3, установленный на нижнем основании 11, подключен к отдельному нормирующему преобразователю (на фиг. не показаны), а выходы всех преобразователей по последовательному интерфейсу соединены единой информационной шиной с контроллером 5. Таким образом, при приложении нагрузки к платформе по выходному коду G, на каждом из четырех датчиков 2 или 3 диапазона может быть определен радиус-вектор приложения нагрузки.
Видеокамера 4 верхнего обзора, размещенная консольно с возможностью поворота на стойке 23, подключена к компьютеру 6 и предназначена для фиксирования положения рабочего колеса, установленного на позиции балансировки с последующим введением его изображения на дисплей упомянутого компьютера 6.
Для транспортировки и установки на позицию балансировки рабочего колеса, а позже его поворота при взвешивании оно снабжено временно используемым приспособлением 24.
Для исключения влияния неправильного выставления верхних узлов 25 и 26 силоизмерительных датчиков 2 и 3, негоризонтальности платформ, завышенности платформ относительно друг друга, а также влияния несплошностей рабочих колес гидротурбин был применен метод суперпозиции. Метод суперпозиции заключается в том, что общий результат воздействия на систему многих факторов равен сумме результатов воздействия каждого фактора (сайт Интернета «bip-ip.com/pnntsip-superpozitii»). Применительно к предлагаемому способу балансировки рабочего колеса гидротурбины суть заключается в следующем: на визирных линиях 19, 20 и 21 обода 17 выбирают три характеристические точки A, B и C, соответствующие проекциям центров силовводящего узла 22 весоизмерительных трех платформ 1 (фиг.6, 7, 8 и 9). При таком подходе выполняют три измерения при повороте рабочего колеса на 120°. Так как характеристические точки смещаются вместе с поворотом рабочего колеса, то каждая точка А, В и С будет взвешена на каждой из трех платформ, также установленных под углом α=120° друг к другу.
Характеристические точки A, B и C выбраны на ободе 17 равноудаленно от геометрического центра рабочего колеса и совмещение с центром силовводящих узлов 22 всех трех платформ 1, в силу чего опорная реакция FA, FB и FC каждой платформы будет находиться в их центре и равна весу колеса GA, GB и GC, приходящегося на каждую платформу в этих же точках, а именно FA=GA; FB=GB и FC=GC.
А так как измерения веса рабочего колеса проводят в трех позициях (1, 2, 3), показанных на фиг.7, 8 и 9 при неподвижных платформах 1, то и реакция опор, а следовательно, и вес в каждой точке каждой платформы трижды будет менять свое значение, т.е.
GA1=G11GB1=G21GC1=G31} – первое измерениеGA1=G12GB1=G22GC1=G32} – второе измерение (1)GA1=G13GB1=G23GC1=G33} – третье измерение
где FA1, FA2 и FA3 – реакция опоры в характеристической точке A на трех позициях 1, 2 и 3 измерения рабочего колеса. То же самое в точках B и C.
И, следовательно, среднее значение по каждой характеристической точке составит:
G¯A=(G11+G22+G33)/3=∑13GAij/3,G¯B=(G21+G32+G13)/3=∑13GAij/3, (2)G¯C=(G31+G12+G23)/3=∑13GAij/3,
где i – номер платформы, j – номер измерения, ∑13Gi/3 – арифметически усредненное значение нагрузки в точках A, B и C рабочего колеса, измеренное в трех позициях.
Способ статической балансировки рабочего колеса гидравлической турбины осуществляется следующим образом.
Установку платформ 1 под рабочее колесо, находящееся в подвешенном состоянии, осуществляют задвижением до касания неподвижными упорами 14 и визирным керном 15 боковой поверхности 16 обода 17. При этом соблюдают однозначное позиционирование платформ 1 относительно центра вращения рабочего колеса. Платформы 1 устанавливают визирной линией 19 по разметочной риске также 19, нанесенной на внешнем ободе 17 рабочего колеса и точно позиционируют упорами 14 и визирным керном 15, образуя реперные точки a, b, c и f отсчета координат месторасположения силоизмерительных датчиков 2 и 3. При этом все силоизмерительные датчики 2 или 3, а соответственно и рабочие поверхности 8 платформ 1 выставляют в один уровень горизонта, после чего производят нагружение платформ 1 балансируемым колесом, фиксируют его положение видеокамерой 4 верхнего обзора и вводят изображение в компьютер 6 системы измерения и обработки результатов.
При нагружении платформ 1 рабочим колесом сигнал от каждого датчика 2 или 3 поступает на контроллер 5 и подается в компьютер 6, определяя автоматически координаты каждого датчика и приходящуюся нагрузку на каждую платформу 1. Ввиду того, что каждая из платформ 1 имеет по четыре опрашиваемых датчика на каждом диапазоне измерения, то это позволяет определить координаты приложения сил на платформу в целом без значительных погрешностей, а следовательно, и достаточно точно определить центр масс и вектор приложения сил всей платформы 1.
При балансировке рабочего колеса гидравлической турбины используются только три платформы 1.
Практическое применение способа показало, что наиболее целесообразно весоизмерение рабочих колес гидравлических турбин с использованием трех платформ 1, так как наиболее устойчивое положение нижней плоскости колеса геометрически определяется тремя точками.
Исходными для расчетов будут значения средних нагрузок, определяемых по каждой характеристической точке в соответствии с приведенными формулами (1, 2).
Положение центра масс в целом рабочего колеса определяют по формулам:
Xр.к=∑13Xji⋅G¯ji∑13G¯ji=G¯A⋅XA+G¯B⋅XA+G¯C⋅XC∑13G¯ji (3)
Yр.к=∑13Yji⋅G¯ji∑13G¯ji=G¯A⋅YA+G¯B⋅YA+G¯C⋅YC∑13G¯ji, (4)
где Xр.к – координата центра масс рабочего колеса по оси X;
Yр.к – координата центра масс рабочего колеса по оси Y;
G¯A, G¯B и G¯C – значение средней нагрузки, определяемой по каждой характеристической точке;
XA, XB и XC – координаты характеристических точек относительно оси X;
YA, YB и YC – координаты характеристических точек относительно оси Y;
∑13G¯ji – общий вес рабочего колеса;
∑13Xji⋅G¯ji – статический момент рабочего колеса относительно оси X;
∑13Yji⋅G¯ji – статический момент рабочего колеса относительно оси Y.
Для повышения точности вычисления на все силоизмерительные датчики, например 2, одной платформы нагрузка передается через полусферической формы силовводящий узел 22, расположенный в центре каждой платформы, центр которого совпадает с характеристическими точками A, B и C обода 17 после поворота каждой из них на 120°.
После проведенного первого взвешивания рабочего колеса весом 15 т на позиции 1 (фиг.7), его результат в каждой характеристической точке A, B и C, находящейся на каждой платформе 1 и общий вес заносятся измерительной системой в таблицу компьютера 6. Затем осуществляют поворот рабочего колеса по часовой стрелке относительно неподвижных платформ 1 на угол α=120°, при этом риска 19 с точкой A перемещается на позицию 2 и соответственно остальные точки B и C также перемещаются на новые позиции 3 и 1, и повторно проводят измерения веса, приходящегося на каждую точку A, B и C, и общий вес всего рабочего колеса, результаты величин которых также заносятся в компьютер 6 (фиг.8). После последнего, третьего поворота колеса риска 19 с точкой A окажется на третьей позиции, измеренные результаты с которой также поступят в компьютер 6 и заносятся в таблицу (фиг.11). После проведенных этих трех измерений на позициях 1, 2 и 3 в характеристических точках A, B и C, компьютер программно просчитывает в соответствии с формулами (1) и (2) среднеарифметическое значение нагрузки, приходящейся на каждую характеристическую точку рабочего колеса в целом.
Все полученные результаты трехкратного взвешивания рабочего колеса гидравлической турбины весом 15 т сведены в таблицу, отображенную на фиг.11.
Как следует из таблицы, каждое взвешивание рабочего колеса показывает в каждой характеристической точке наличие различной нагрузки. Наибольшая нагрузка в каждой позиции измерения складывается в точке A, в то же время в точках B и C наблюдается примерное весовое равенство. Это свидетельствует о наличии в зоне точки A сплошного участка рабочего колеса и созданного мнимого дисбаланса. Вместе с тем, общий усредненный вес рабочего колеса ∑GABC всех точек на всех трех позициях измерения составляет 14998 кг, и усредненный вес, приходящийся на каждую характеристическую точку A, B и C в сумме, также составляет 14997 кг, что подтверждает высокую точность балансировки предлагаемого способа. Таким образом, трехкратное изменение позиции взвешивания рабочего колеса относительно платформ 1 обеспечивает, во-первых, устранение мнимого дисбаланса, образующегося за счет несплошностей рабочего колеса, а во-вторых, исключает влияние неправильного выставления верхних узлов 25 и 26 силоизмерительных датчиков 2 и 3 платформ 1, негоризонтальности и завышенности их относительно друг друга.
При необходимости измерения рабочих колес с более высоким весом, например 50 или 100 тонн, силоизмерительные датчики 2 с НПИ, равным 3 т, выводятся механизмом регулирования 12 из зоны его контакта с плитой 13, а в работу вводятся датчики 3 с НПИ, равным 15 т. После проведения измерительных операций по определению веса все дальнейшие действия способа связаны с работой системы измерений и обработки их результатов.
На изображение корпуса рабочего колеса на мониторе компьютера 6, полученное с помощью видеокамеры 4 верхнего обзора, установленной на консольной стойке 21, индицируется отметка координаты центра масс корпуса рабочего колеса и радиус-вектор
R∂=Xрк2+Yрк2, (7)
связывающий центр корпуса рабочего колеса и его центр масс. Радиус r, на котором может быть установлен балансировочный груз, задается конструктивно. На схеме условно показано положение центра масс рабочего колеса, величина и радиус его дисбаланса относительно осей X и Y с тремя платформами (фиг.10). В соответствии со схемой радиус дисбаланса определяют по формуле:
R∂=Xрк2+Yрк2
Соответственно, момент, возникающий за счет несовпадения центра масс и оси вращения колеса, составит:
M=R∂⋅GРКср., (8)
где GРКср.=GAср+GBср+GCср−G0
где – R∂ – радиус вектор смещения осей вращения и центра масс,
GAср, GBср, GCср – усредненный вес рабочего колеса, приходящийся на каждую из платформ 1;
G0 – вес приспособления 24.
Для выполнения балансировки точно накладывают балансировочный груз, масса которого определяется из уравнения:
Gб⋅r=R∂⋅GРКср., откуда Gб=R∂⋅GРКср.r, (9)
где Gб – балансировочный груз;
r – радиус колеса;
R∂ – радиус дисбаланса;
GРКср. – вес колеса.
Таким образом, в процессе проведения балансировки рабочего колеса система измерения и обработки результатов программно автоматически индицирует на мониторе компьютера 6 положение центра масс относительно оси его вращения, а также определяет значение Xр.к, Yр.к. и R, а при найденном R точно устанавливает вес и место размещения балансировочного груза, что способствует увеличению производительности измерений неуравновешенности гидравлической турбины.
Предложенный способ обеспечивает высокую точность балансировки рабочего колеса, так как имеет низкую степень погрешности измерений и высокий порог чувствительности по моменту, которые обеспечиваются конструктивным построением платформы 1 в целом, а также точной установкой силоизмерительных датчиков 2 и 3 и упоров-призм 14 на ее рабочей поверхности 8 и ее невертикальностью.
Так для рабочего колеса диаметром 15 м погрешность предложенного способа балансировки по осям X и Y составит до 3,0 мм, а его расчетная чувствительность по моменту балансировки будет находиться в пределах до 180-230 кг·см для имеющейся точности платформ 1.
Предложенный способ позволяет повысить точность балансировки рабочих колес гидравлических турбин, расширить диапазон их балансировки до 150 т за счет применения усовершенствованных платформ с приложением усилий при нагрузке на силовводящий узел, размещенный в центре каждой платформы, и использования средств программного измерения и оценки результатов, а также применения трехкратного измерения веса рабочего колеса с использованием метода суперпозиции.
В настоящее время усовершенствованные платформы изготовлены в производстве, проведены их испытания на взвешивании макетного образца рабочего колеса турбины, получены положительные результаты, подтверждающие достижение технического результата, т.е. повышение точности измерения способа балансировки, проведены испытания на балансировке рабочего колеса турбины «Волжская 21» весом ~80 т, по результатам испытаний оборудование введено в промышленную эксплуатацию.
1. Способ балансировки рабочего колеса гидравлической турбины, характеризующийся центрированием колеса с установлением точек отсчета координат местонахождения силоизмерительных датчиков, размещенных на поверхности платформ, используемых для взвешивания рабочего колеса, при этом обеспечивают приложение нагрузки к центру каждой платформы с помощью силовводящего узла для каждого диапазона веса рабочего колеса, после этого выбирают по методу суперпозиции на поверхности колеса характеристические точки, соответствующие проекциям центров весоизмерительных платформ и осуществляют поворот рабочего колеса по часовой стрелке относительно упомянутых платформ на заданный угол, а затем выполняют после каждого его поворота измерение веса на каждой платформе с каждой выбранной одноименной характеристической точкой с последующим арифметическим усреднением результатов измерений по всем платформам в каждой одноименной характеристической точке и общего веса рабочего колеса также в каждой одноименной характеристической точке, после чего определяют известным образом расчетным путем с использованием системы измерений и обработки результатов дисбаланс и точно устанавливают балансировочные грузы.
2. Способ по п.1, характеризующийся тем, что систему измерений и обработки результатов образуют из преобразователей сигналов по количеству силоизмерительных датчиков, подключенных к контроллеру, соединенному с компьютером.
3. Способ по п.1, характеризующийся тем, что количество характеристических точек выбирают равным количеству весоизмерительных платформ.
4. Способ по п.1, характеризующийся тем, что угол установки весоизмерительных платформ и угол поворота характеристических точек, выбранных на рабочем колесе, принимают равным 120°, а количество платформ равным трем.
5. Способ по п.1, характеризующийся тем, что центрирование рабочего колеса гидравлической турбины проводят по боковой поверхности внешней стенки обода с помощью подпружиненного визирного керна и упоров в виде призм, жестко установленных на рабочей поверхности платформ с силоизмерительными датчиками.
6. Способ по п.1, характеризующийся тем, что силовводящий узел выполняют в виде полусферической формы упора, установленного точно в центре платформы.
7. Способ по п.1, характеризующийся тем, что отцентрированное рабочее колесо гидротурбины фиксируют видеокамерой и вводят его изображение в компьютер системы измерения и обработки результатов и после определения значений вектора и центра масс всего колеса накладывают их на компьютерное изображение.
findpatent.ru
Статическая и динамическая балансировка дисков роторов турбин
Замена дефектных деталей ротора турбины, а также сборка, сопровождающаяся обычно пригонкой деталей, могут быть причиной появления одной или нескольких неуравновешенных масс. В зависимости от расположения этих масс неуравновешенность может быть статической или динамической.
Ротор, неуравновешенные массы которого приводятся к одной массе, создающей центробежную силу при его вращении, называется статически неуравновешенным. Ротор, неуравновешенные массы которого при вращении создают две центробежные силы, противоположно направленные и не лежащие в одной плоскости, перпендикулярной к оси ротора, считается динамически неуравновешенным. В этом случае уравновешивание ротора может быть осуществлено только динамической балансировкой.
Статическая балансировка производится на балансировочном приспособлении (рис. 97), состоящем из жестких опор 4 с укрепленными на них призмами-ножами 3, расположенными в одной горизонтальной плоскости, строго по уровню или ватерпасу. Поверхность призм закалена и шлифована. Статическая балансировка диска основана на его свойстве поворачиваться под действием момента неуравновешенной силы и приходить в состояние покоя при расположении тяжелого места в наинизшем положении.
Рис. 97. Приспособление для статической балансировки дисков.
При балансировке диск 1 насаживают на специальную оправку 2 строго перпендикулярно к ее оси и вместе с оправкой устанавливают на призмы 3 опор 4 приспособления, прокатывая диск сначала в одну, а затем в другую сторону. При наличии неуравновешенности более тяжелая часть диска окажется внизу. Затем на противоположной стороне диска прикрепляют груз (между лопатками) и вновь прокатывают диск по призмам, подбирая груз по массе таким, чтобы диск устанавливался в любом положении при прокатывании его по призмам; это указывает на то, что центр тяжести диска совместно с добавленным грузом переместился в его геометрический центр.
Закончив балансировку, уравновешивающий груз взвешивают и, сняв с утяжеленной стороны диска соответствующее количество металла, взвешивают его. Массу и место снимаемого металла определяют из отношения gl—pr, где g — масса навешиваемого груза; l — плечо навешиваемого груза; р — масса металла, подлежащего снятию; г — расстояние до места, где будет сниматься металл. Поскольку l всегда больше г (так как неуравновешенный груз подвешивают между лопатками, а снимают металл у обода диска), то масса снимаемого металла практически больше массы подвешенного неуравновешенного груза. Сняв необходимое количество металла, вновь проверяют уравновешенность диска. Статическая балансировка считается выполненной, если оставшаяся после балансировки неуравновешенность диска создает неуравновешенную центробежную силу не более 4—5% массы диска. При подвешивании такого груза к диску в вертикальной плоскости, не проходящей через центр диска, последний будет страгиваться с места. Чтобы облегчить определение утяжеленной части диска, намечают ряд точек, обычно восемь, деля окружность диска на восемь равных частей (1—8 на рис. 97).
Из известных методов динамической балансировки роторов турбин наибольшее распространение получил метод «обхода грузом». Балансировка по этому методу включает два этапа: определение положения уравновешивающего груза и определение массы уравновешивающего груза.
Динамическую балансировку производят на специальных балансировочных станках (рис. 98). Ротор 5 турбины устанавливают на подшипники 2 раздвижных стоек 4 станка. Каждый подшипник соединен со станиной станка пружиной 9, расклиненной клиньями 10. Толщину пружин выбирают в зависимости от массы ротора. Каждый из подшипников может быть либо застопорен устройством 1, либо освобожден, и тогда он совершает колебательное движение. Ротор вращается электродвигателем 7 через быстродействующую магнитную муфту 6.
Рис. 98. Станок для динамической балансировки роторов.
Колебание подшипников записывается самопишущим прибором 8 на барабане 3 или определяется индикатором.
Во время балансировки с помощью электродвигателя вращают ротор, поочередно открывая подшипники и определяя, при какой частоте вращения наблюдается максимальная амплитуда колебаний системы ротора и опор. Балансировку начинают с того конца ротора, который имеет наибольшую неуравновешенность (наибольшую амплитуду колебаний), например в плоскости I—I. Крайний диск в этой плоскости делят по окружности на восемь равных частей. Затем пробный груз последовательно устанавливают между лопатками в каждую из восьми точек диска, вращая в каждом случае диски и записывая амплитуды колебаний. Очевидно, что чем ближе пробный груз расположен по окружности к неуравновешенной массе, тем больше амплитуда колебаний. По полученным амплитудам колебаний на развертке окружности строят кривую (синусоиду), по которой определяют место, где необходимо укрепить уравновешивающий груз.
Затем переходят ко второму этапу работы. Уменьшая или увеличивая массу уравновешивающего груза (в одной и той же точке), находят наименьшую амплитуду колебания подшипника и временно закрепляют найденный уравновешивающий груз в данной точке, после чего приступают к балансировке второй стороны ротора в плоскости II—II таким же путем, т. е. закрепив опору (подшипник) в плоскости I—I, при открытом подшипнике в сечении II—II балансируют эту сторону ротора. После балансировки обеих сторон специальным расчетом, предусмотренным инструкцией по балансировке, определяют массы уравновешивающих грузов на противоположные опоры с учетом их взаимного влияния. Заканчивают балансировку ротора контрольной проверкой, для чего освобождают подшипники от стопоров, сообщают ротору критическую частоту вращения и проверяют амплитуду колебаний обоих подшипников. Зная расположение грузов и их массу, изготовляют постоянные грузы и закрепляют их на дисках или снимают металл в утяжеленных местах, если масса неуравновешенного груза (дебаланс) невелика.
www.stroitelstvo-new.ru