Контроль трубопроводов, диагностика и ультразвуковой контроль сварных соединений трубопроводов
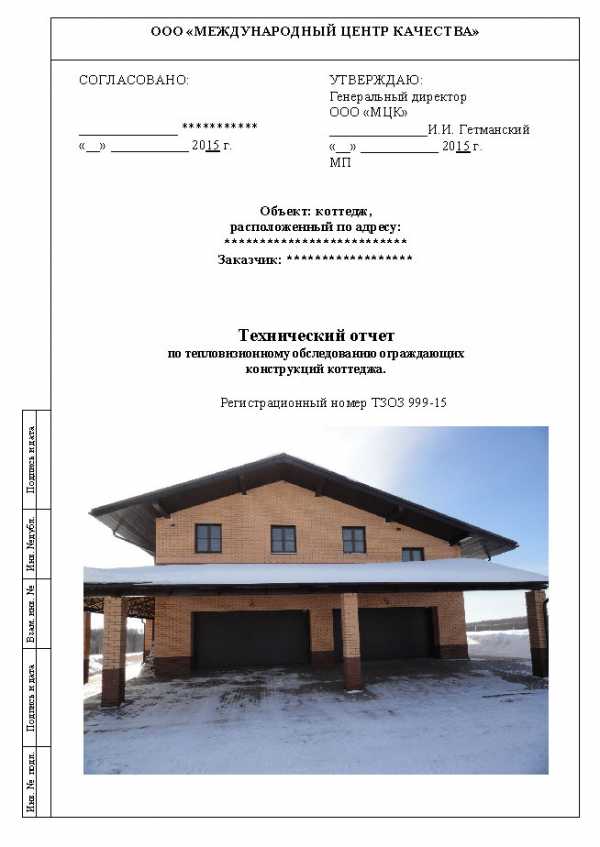
Пример технического отчета тепловизионного обследования.
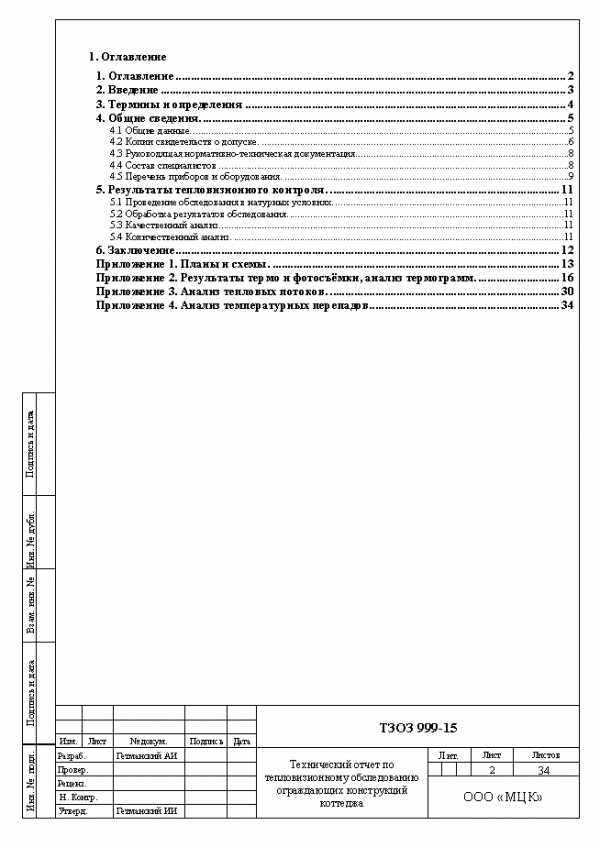
Структура технического отчета.
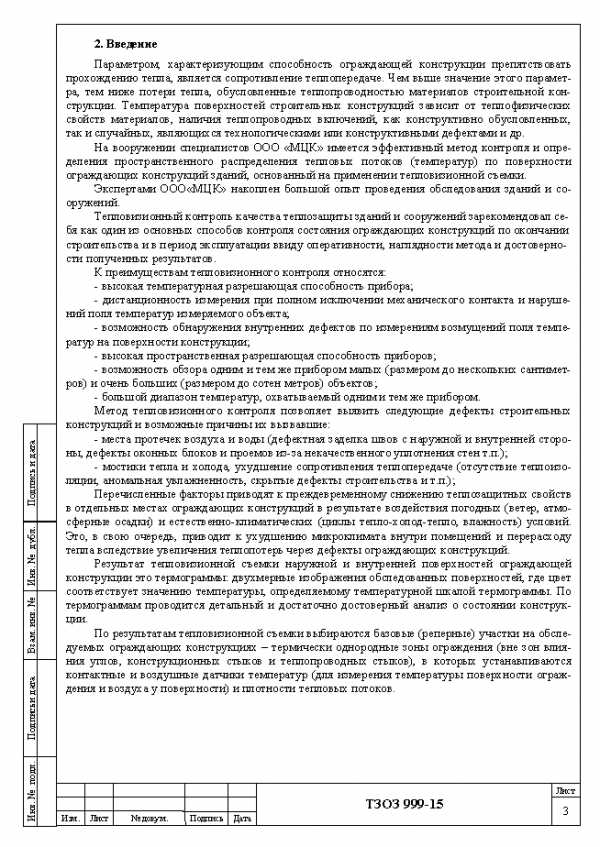
Общие положения технического отчета.
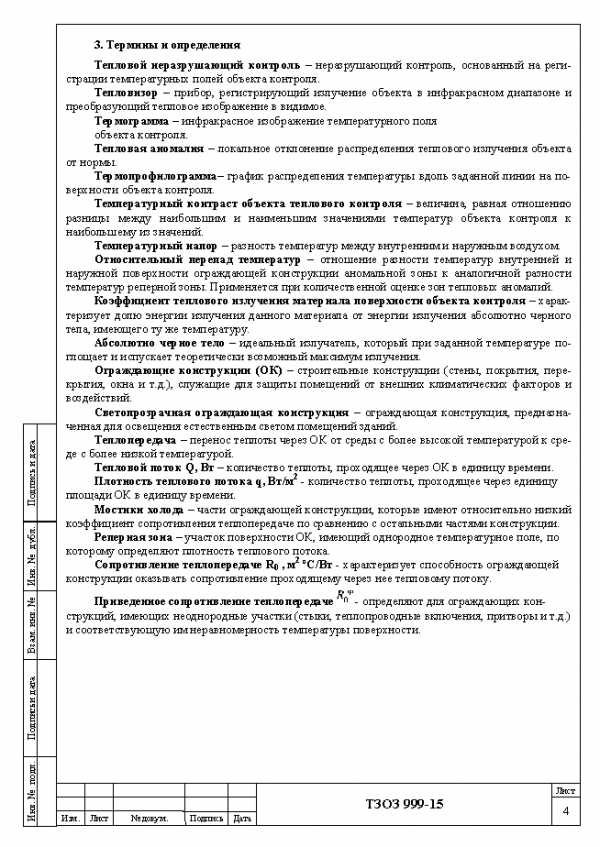
Термины и определения.
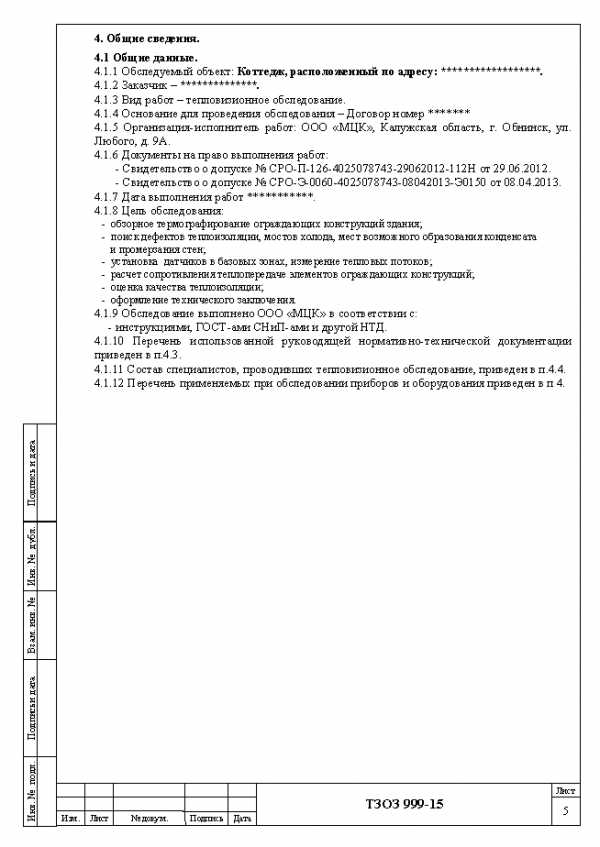
Общие сведения.

Допуск СРО на обследование зданий.
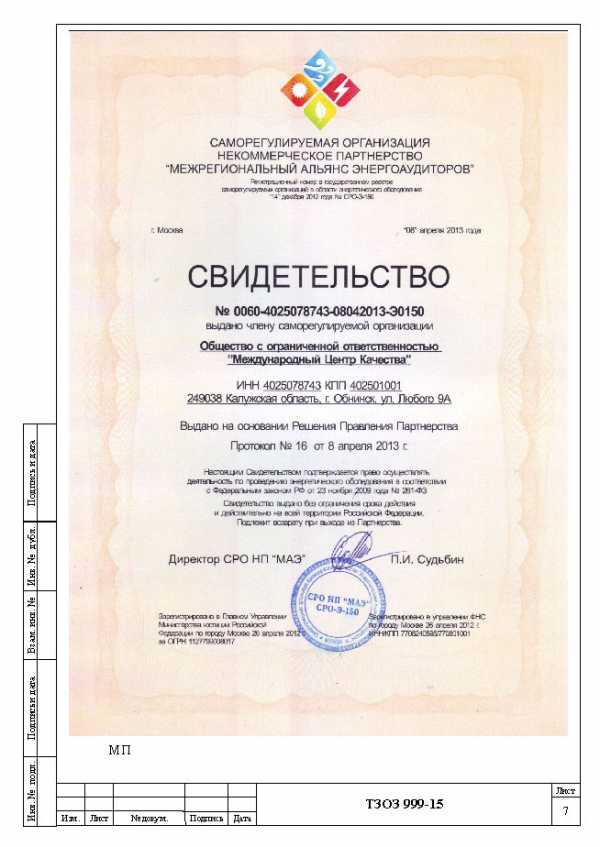
Допуск СРО энергоаудит.
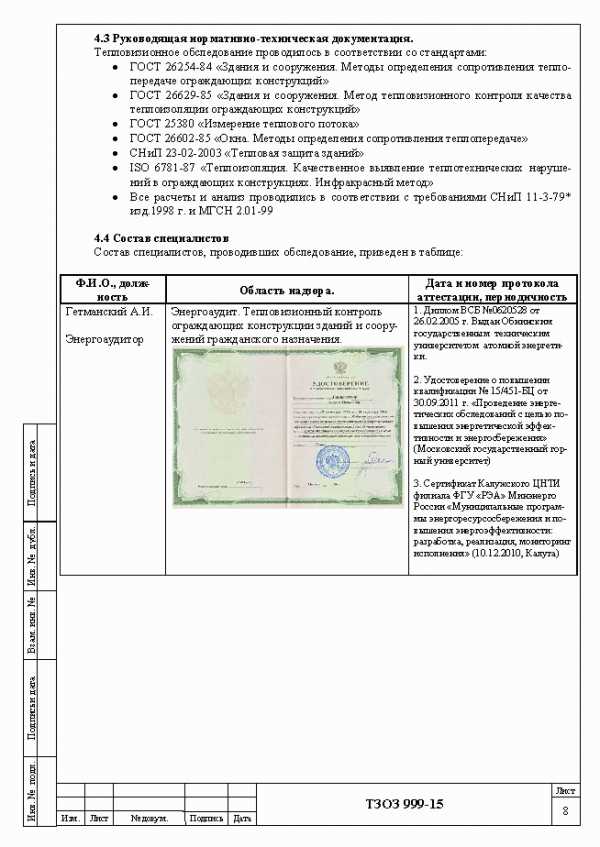
Нормативно-техническая документация.
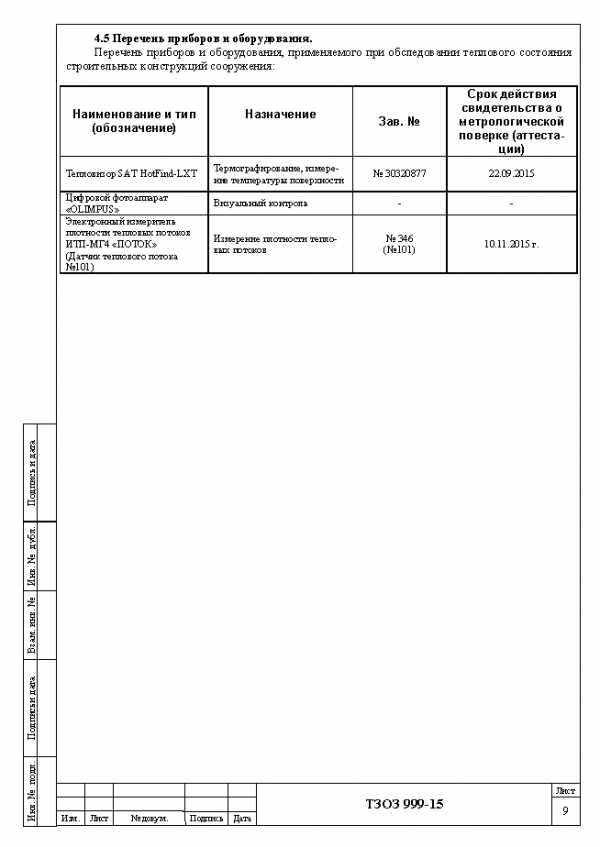
Используемое оборудование тепловизионного контроля.
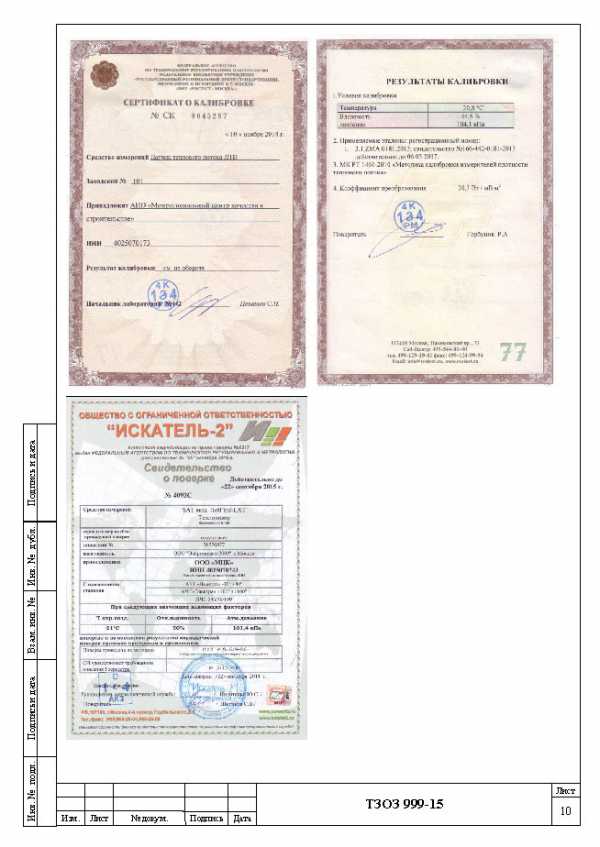
Данные о поверке средств измерения.
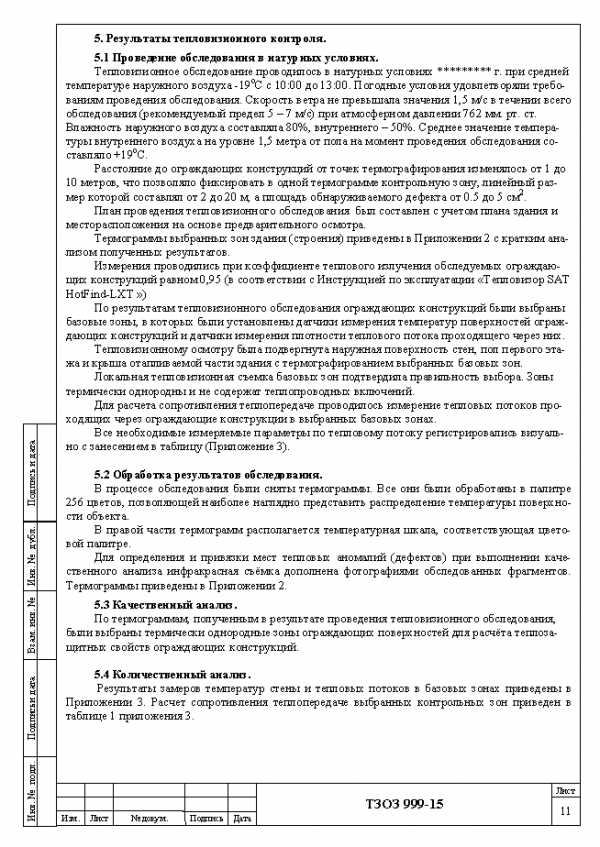
Результаты тепловизионного контроля.
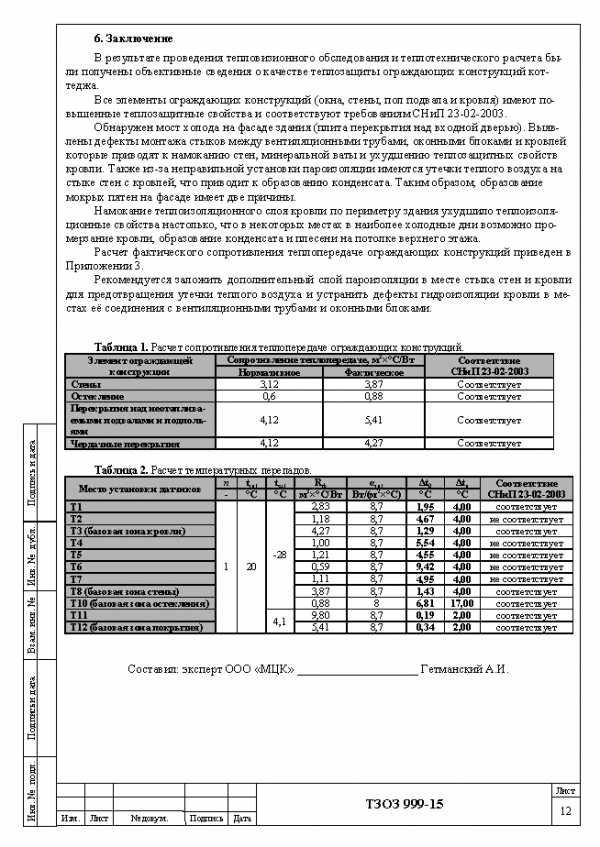
Экспертное заключение.
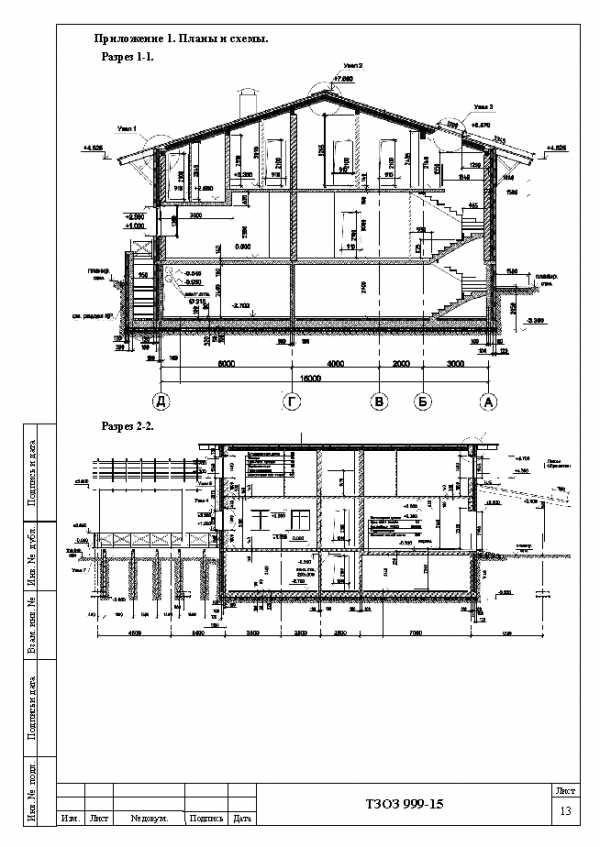
Приложение 1. Планы и схемы.
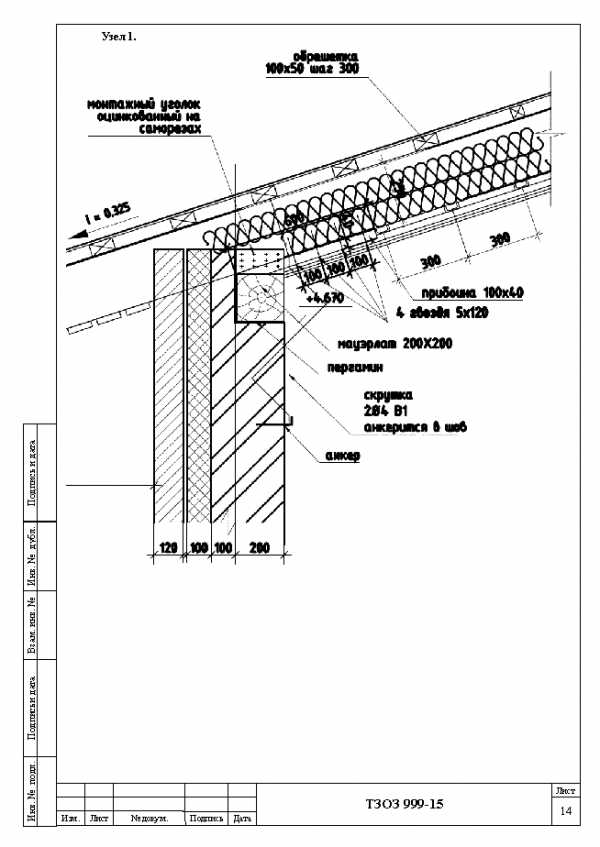
Схема узла примыкания крыши к стене.
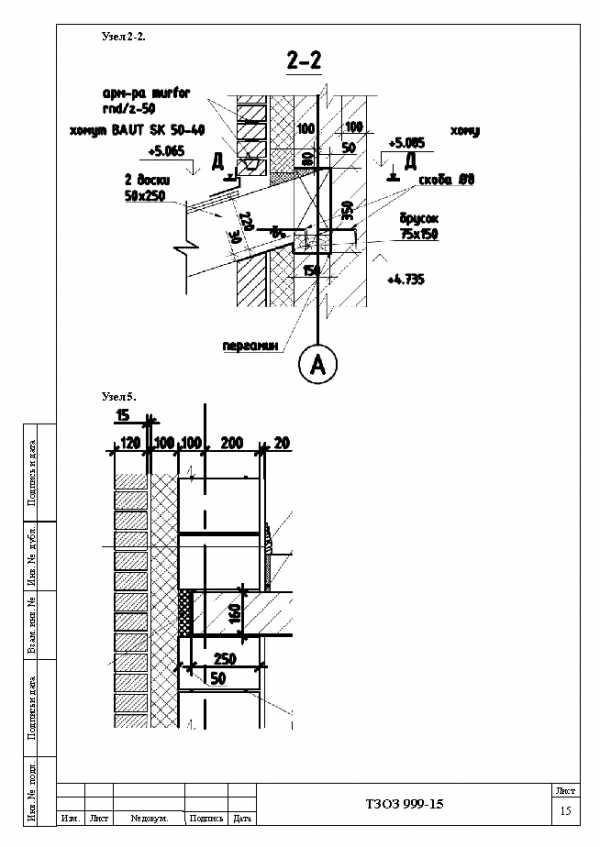
Схемы обследованных узлов и соединений.
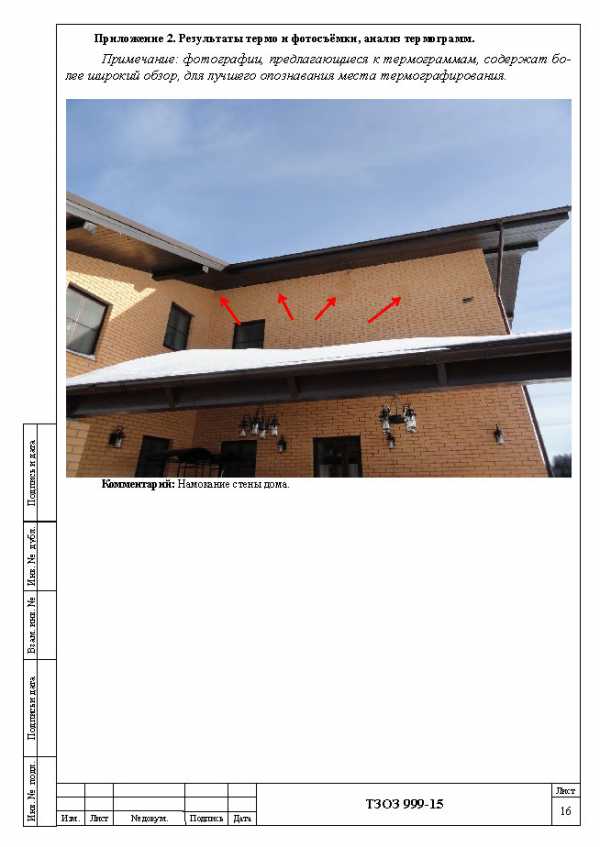
Образование конденсата на стенах дома.
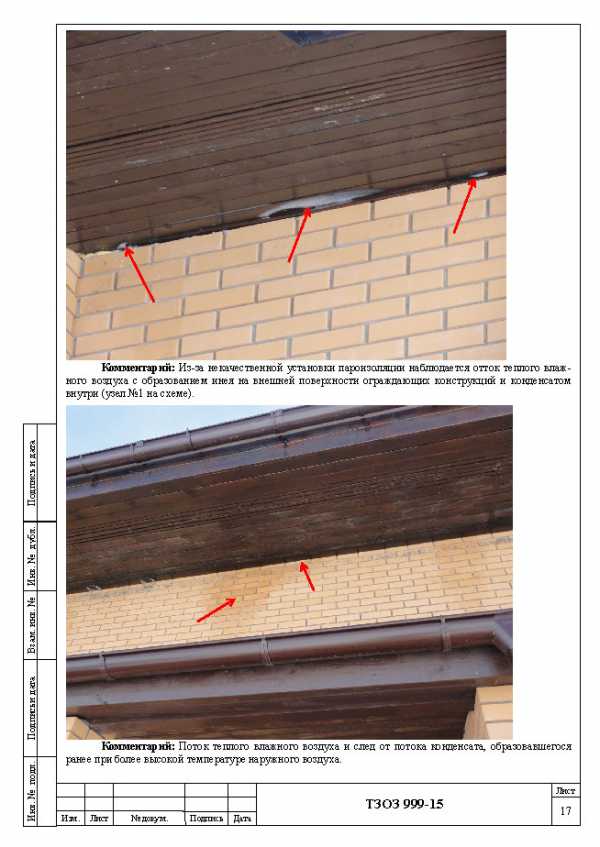
Конденсат на крыше и стенах дома.
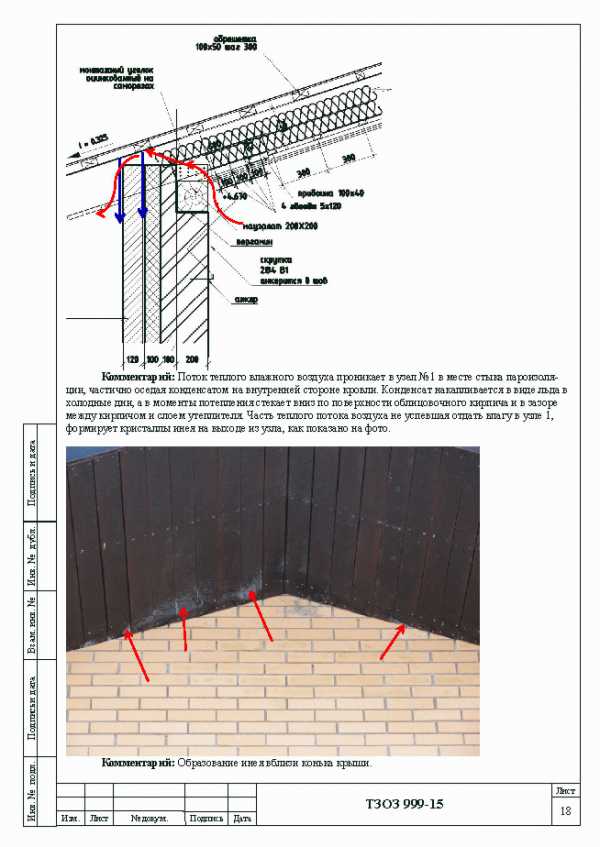
Причина конденсата. Вот почему образуется конденсат на окнах, крыше и стенах.
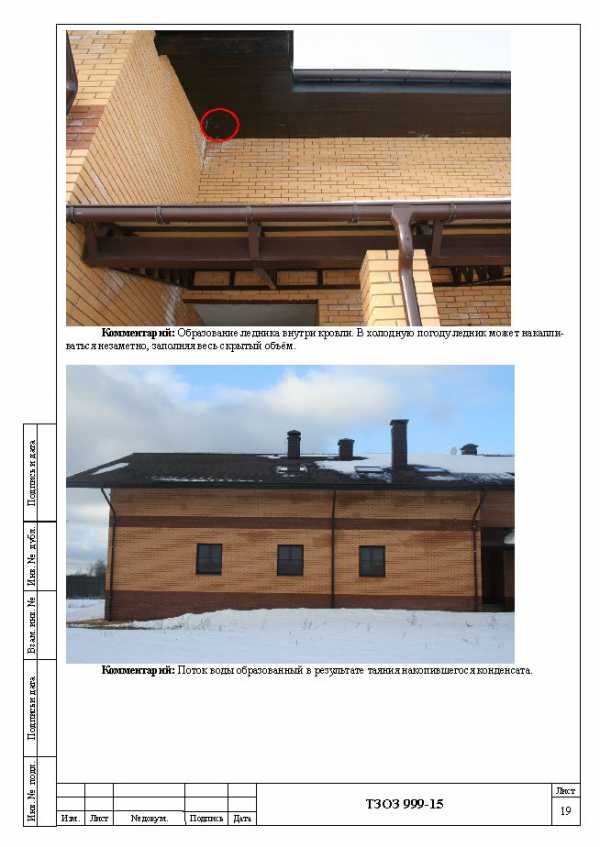
Промерзание стен дома.
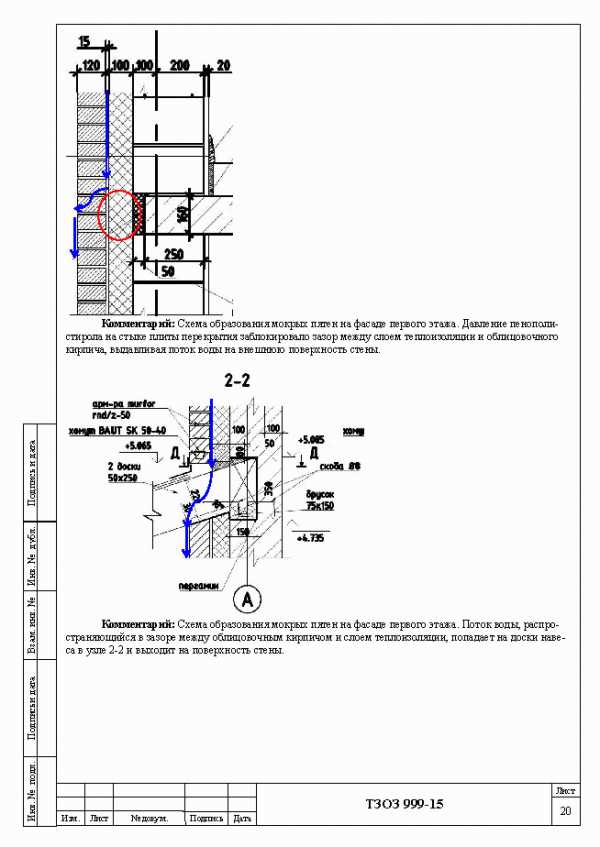
Причина конденсата. Вот почему собирается конденсат на стенах.
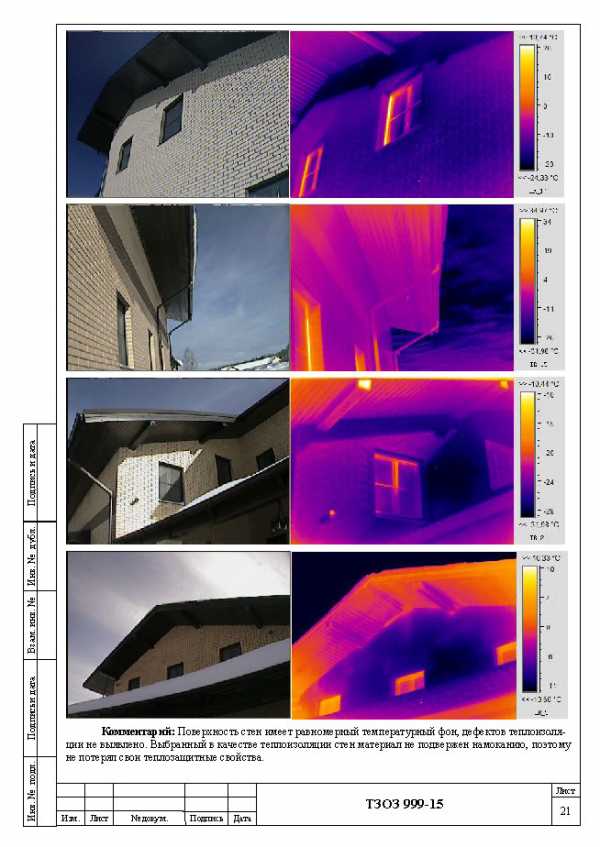
Тепловизионное обследование дома.
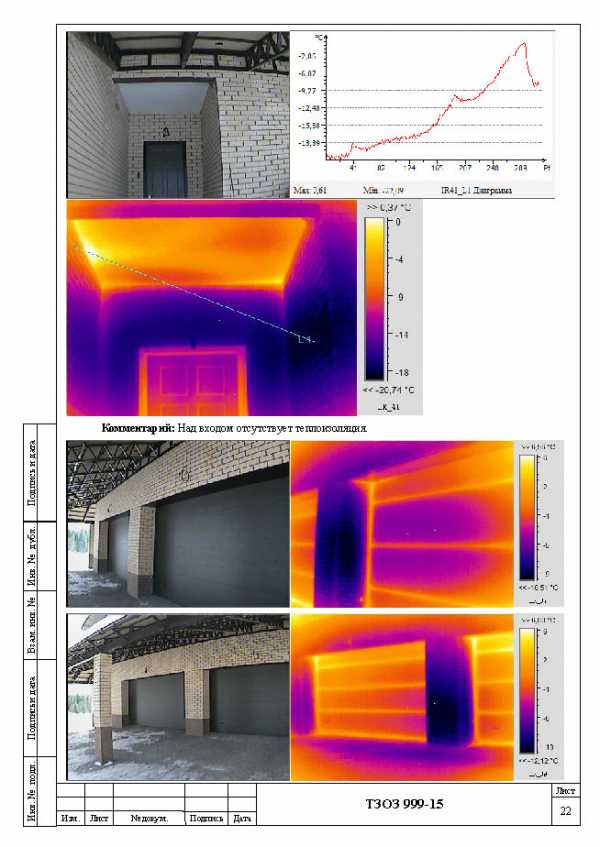
Обследование тепловизором ворот и дверей.
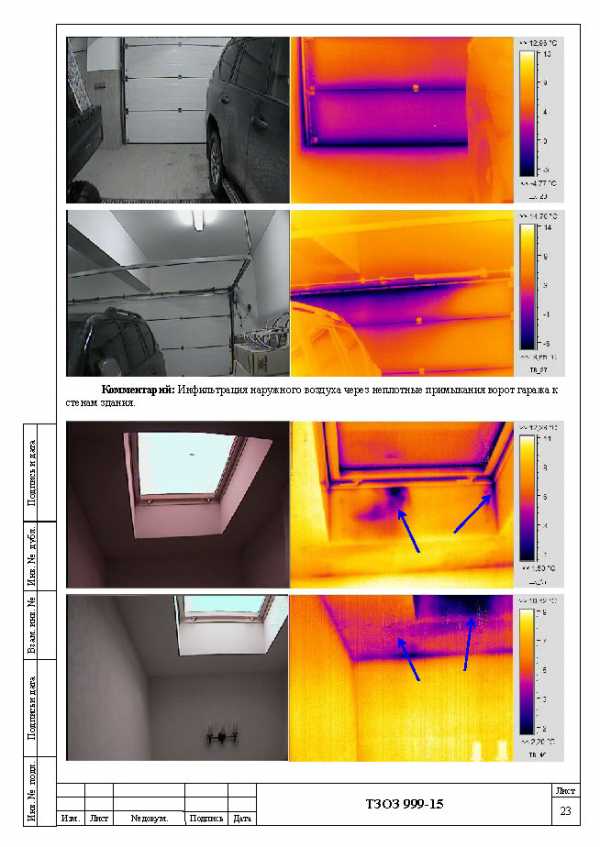
Съемка тепловизором частного дома.
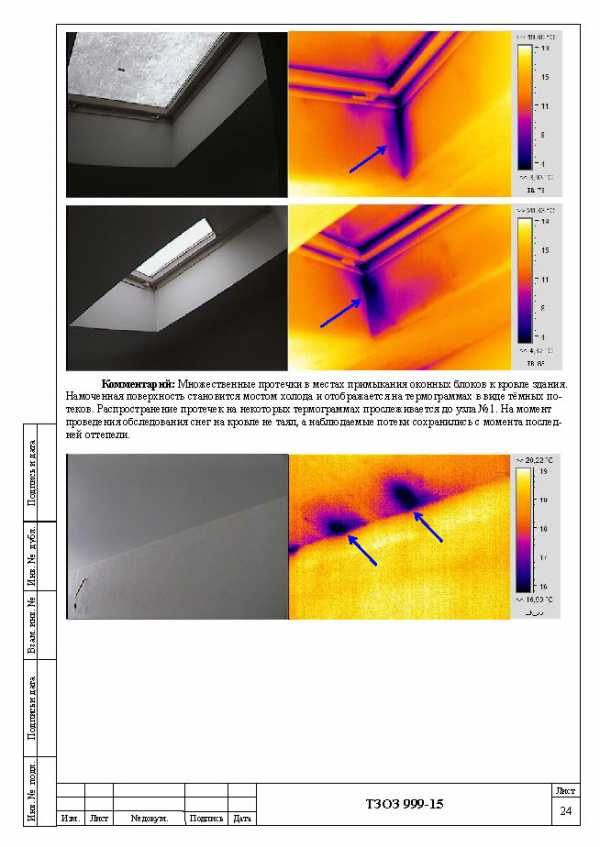
Обследование тепловизором жилого дома.
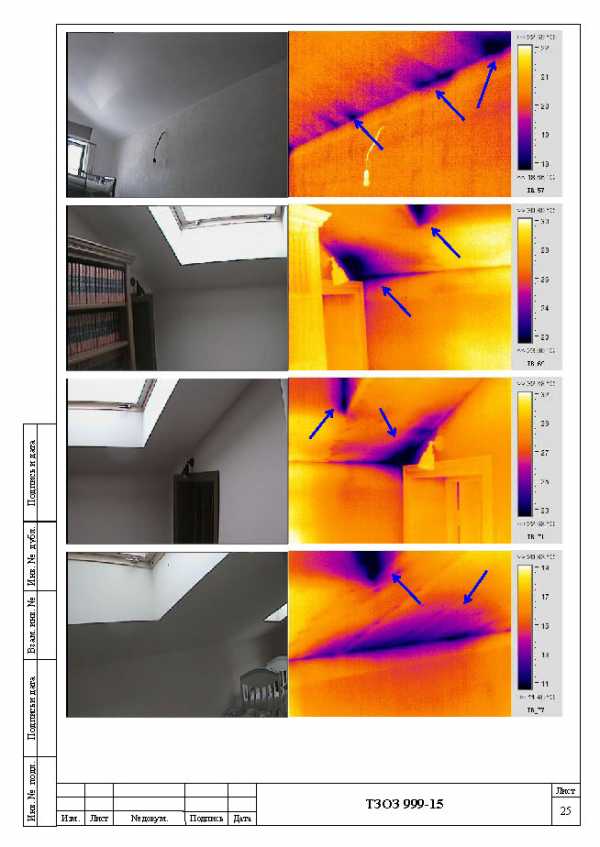
Обследование тепловизором коттеджа.
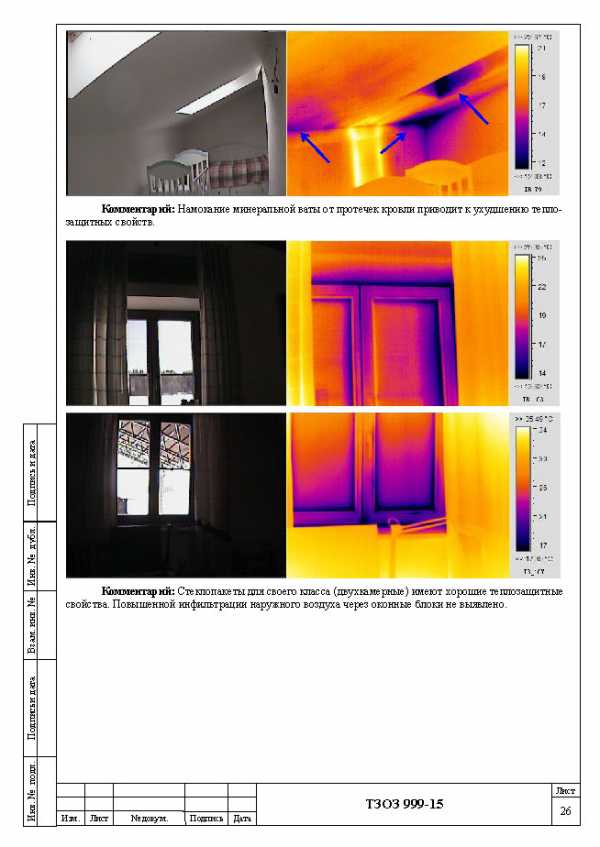
Обследование дома тепловизором.
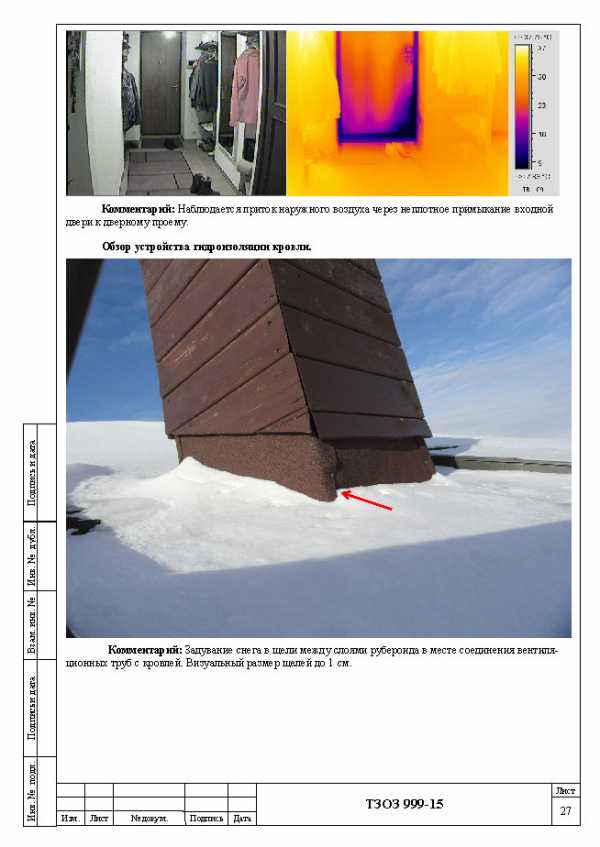
Тепловизионное обследование коттеджа.
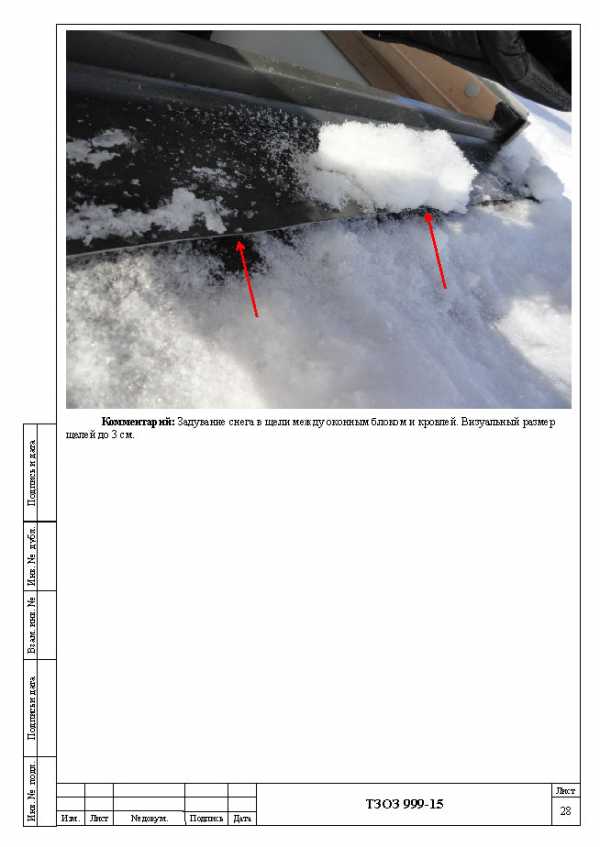
Тепловизионное обследование дома.
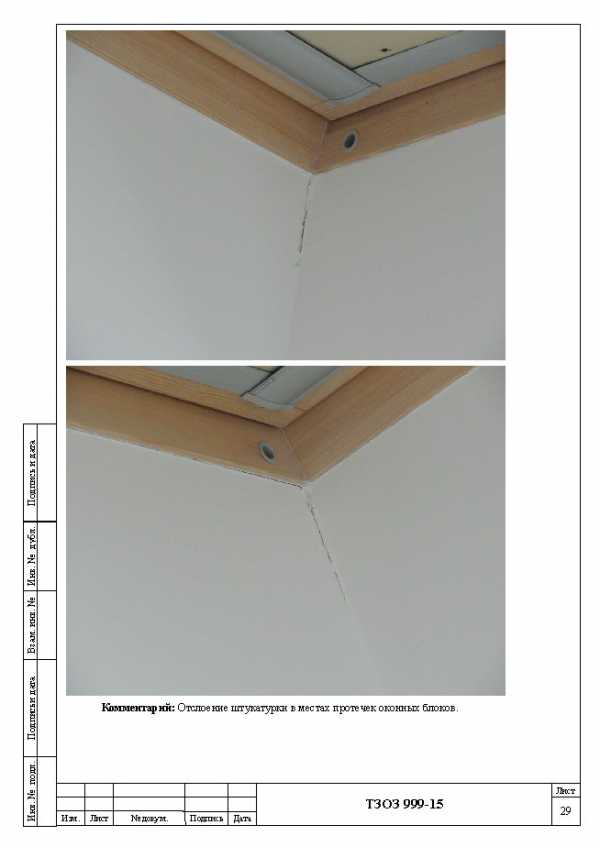
Обследование дома тепловизором.
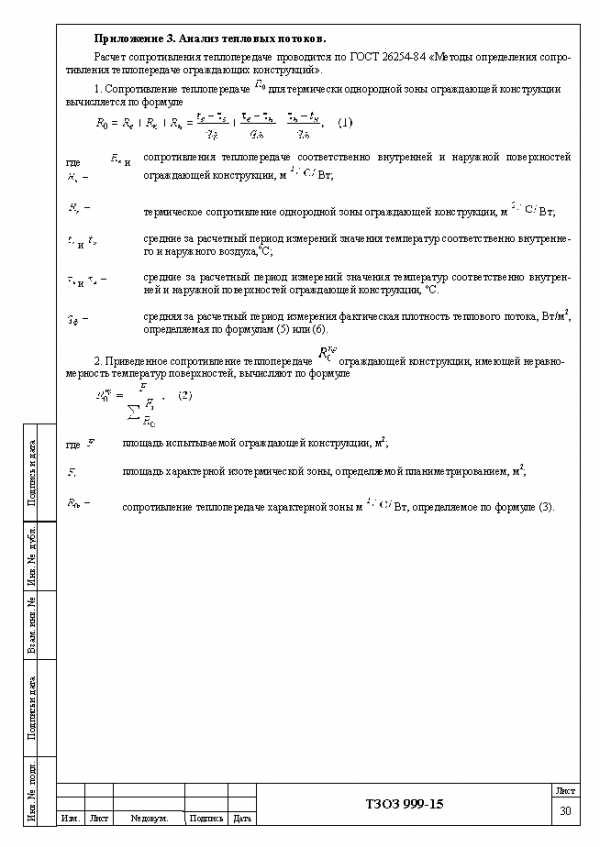
Анализ тепловых потоков.
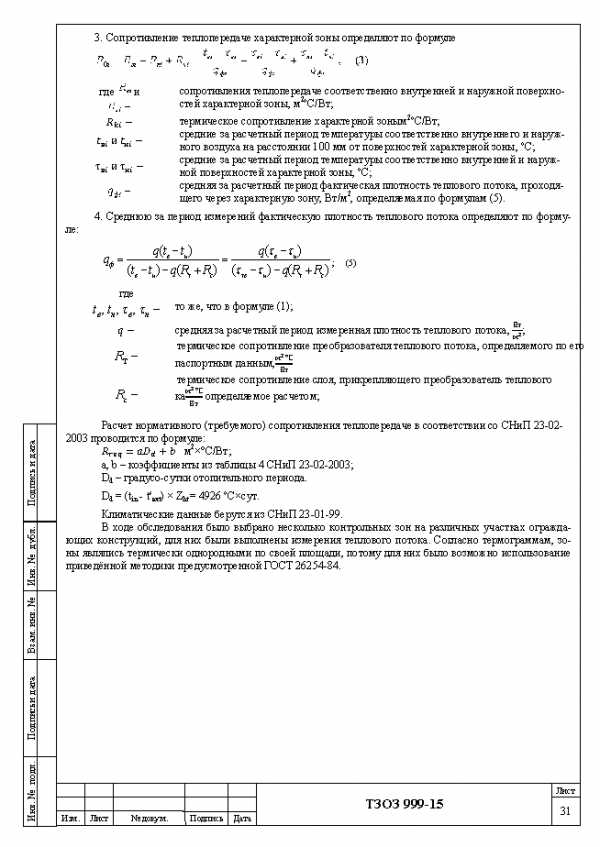
Расчет сопротивления теплопередаче.
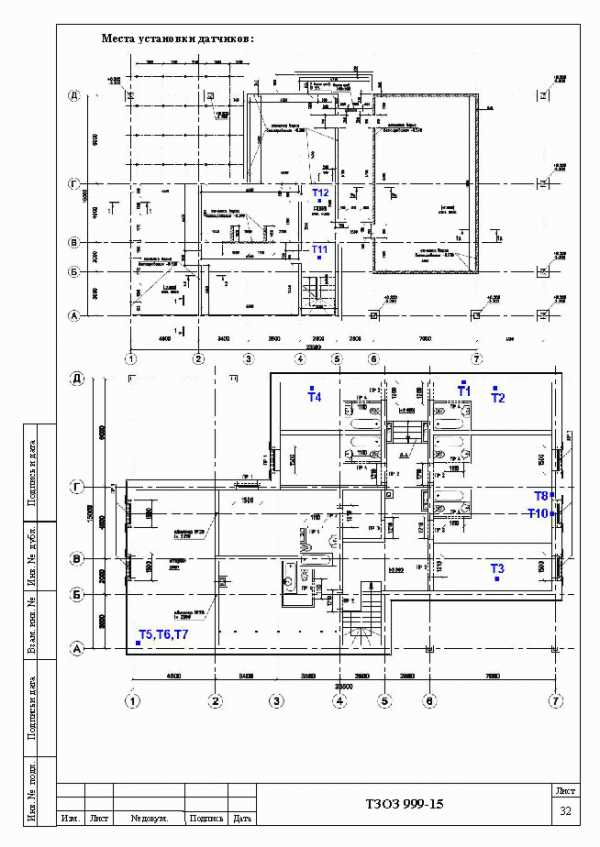
Места измерения тепловых потоков.
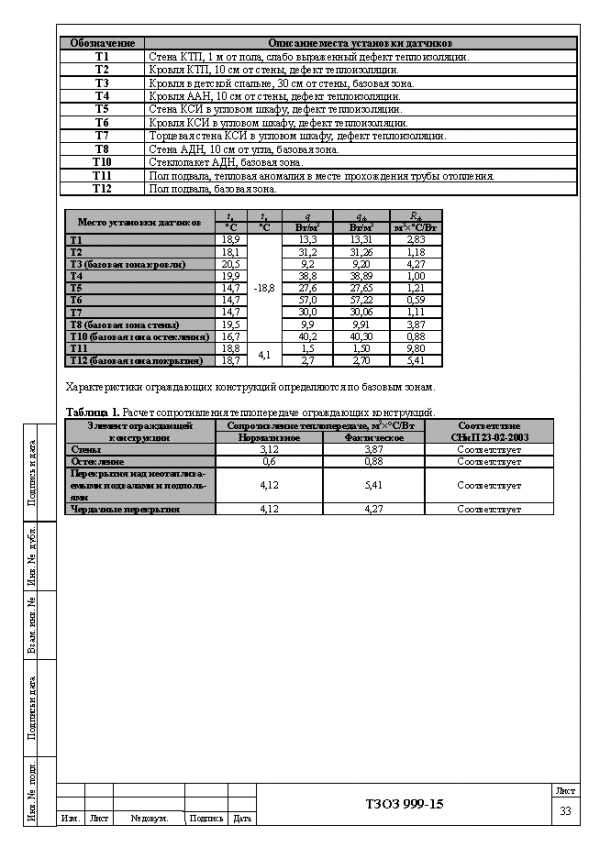
Результаты тепловизионного обследования.
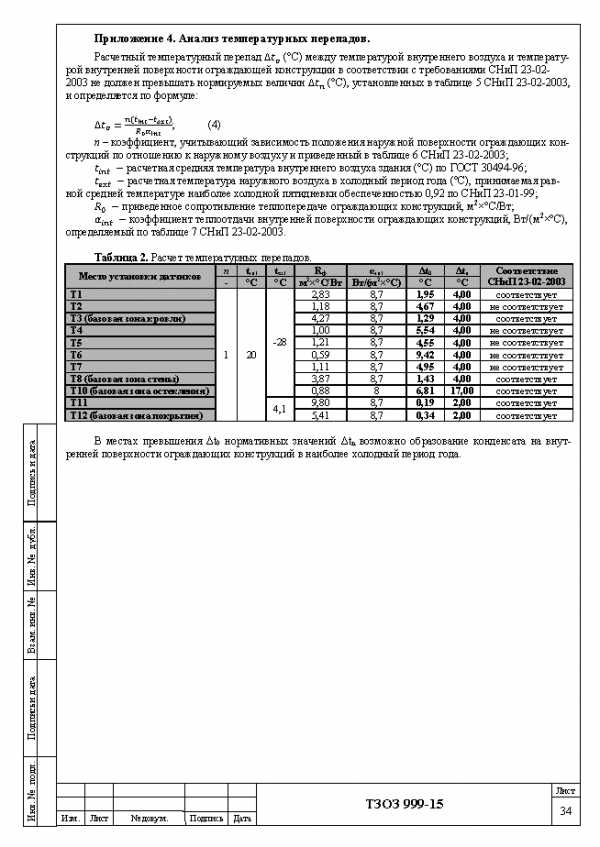
Анализ температурных перепадов.
www.mosexp.ru
Обзор методов дефектоскопии при обследовании трубопроводов
В статье рассмотрены современные методы неразрушающего контроля при обследовании участков трубопроводов и соединительных деталей, находящихся в эксплуатации. Описаны области применения приборов, которые используются для контроля, их принципы работы. Анализируются их достоинства и ограничения области применения. Определены оптимальные методы выявления дефектов, намечены критерии улучшения работы приборов.
Ключевые слова: контроль труб, дефектоскопы, обследование труб, неразрушающий контроль, наружные сканеры.
В условиях эксплуатации на протяжении длительного времени трубопроводы подвергаются различным внешним и внутренним воздействиям, в результате чего происходит деградация материала, коррозионные повреждения, возникают и развиваются трещины усталости на поверхностях труб и другие виды дефектов. Несмотря на то, что проектирование трубопроводов по современным кодам и технология изготовления и монтажа должны обеспечить реализацию назначенного ресурса, исключить возможность возникновения таких дефектов не удается. Чтобы избежать серьезных последствий подрастания дефектов, проводят различные обследования, применяя методы неразрушающего контроля. Неразрушающий контроль — контроль надежности основных рабочих свойств и параметров объекта, не требующий выведения объекта из эксплуатации, либо его демонтажа [1].
Современные методы и средства неразрушающего контроля [17], используемые для диагностики трубопроводов, получили широкое развитие и распространение. Наибольшее применение получили такие методы, как магнитные (магнитной анизотропии, магнитной памяти металла, магнитной проницаемости), акустические (импульсные ультразвуковые, волн Лэмба, фазовые, акустической эмиссии), электрические и оптические (визуальные — эндоскопические, лазерные, голографические). Такие методы применяются для выявления различных дефектов: нарушения герметичности, контроля напряженного состояния, контроля качества и состояния сварных соединений, контроля протечек и других параметров, ответственных за эксплуатационную надежность трубопроводов. При этом программы, методы и средства контроля трубопроводов различного назначения (теплопроводов, газопроводов, нефтепроводов, продуктопроводов, водопроводов) незначительно отличается друг от друга [5].
Актуальность данной темы объясняется тем, что в наше время имеется значительное число трубопроводов в эксплуатации и процессе производства; повреждения и разрушение компонентов которых может приводить к серьезным экономическим потерям и пагубным воздействиям на природу [19]. Существенно, что трубопроводы включают много соединительных деталей, как металлических, так и неметаллических, имеющих сложные геометрические формы (узлы), доступ к некоторым частям которых может быть ограничен. В таких случаях методы и технические средства неразрушающего контроля являются оптимальным и максимально удобным решением для проведения обследования определенных районов трубопроводов, без выведения объекта из эксплуатации, а также обследования труднодоступных участков для выявления дефектов.
Дефектоскопия как средство выявления признаков деградации материала трубопроводов и предупреждения аварийных ситуаций [18] естественно находится в поле внимания инженерного и научного сообщества. Постоянно развиваются методы определения размеров, ориентации дефектов, совершенствуется оборудование, проводятся исследования и испытания на выявление характеристик моделей дефектоскопов, а также проводится анализа для последующего улучшения работы средств дефектоскопии.
Вопросам дефектоскопии материалов и конструкций уделяется все большее внимание как у нас в стране, так и за рубежом, о чем свидетельствует непрерывный рост числа учебных центров, задачей которых является подготовка и квалификация специалистов для работы в области разработки методов дефектоскопии и их применения [5].
В связи с актуальностью темы неразрушающего контроля растет число публикаций, в которых исследуются взаимодействия дефектоскопов с трубопроводами. Результат диагностики подобных исследований трубопроводов показал, что нормативная база и приборная часть требуют дальнейшего совершенствования с учетом особенностей системы трубопроводов [2, 3].
История самого старого метода контроля показывает наглядный переход от сложного процесса реализации контроля, зависящего от человеческого фактора, к автоматизированным и экологически чистым методам в настоящее время [6].
В настоящее время обследования методами неразрушающего контроля следует производить в соответствии с [13–15], что позволит существенно повысить показатель надежности при эксплуатации [9].
Зарубежные источники, в частности [20–22], рассматривают возможности применения методов неразрушающего контроля для повышения уровня точности результатов.
Особенности критериев по выбору дефектоскопа
Принципы работы дефектоскопов различны, но при этом существует ряд параметров, по которым можно объективно дать оценку оборудованию по проведению диагностики методом неразрушающего контроля [10].
При выборе дефектоскопа следует учитывать:
- Разрешение дефектоскопа. Точность определения размеров(расположения) дефекта.
- Скорость диагностики. Как правило, чем быстрее идёт диагностика, тем ниже точность определения дефекта.
- Способ крепления прибора.
- Уровень защиты прибора от внешних воздействий. К внешним воздействиям можно отнести влагу, давление, осадки и др.
- Температурный режим. Проводя сканирование при критических температурах, прибор может показывать не точные измерения или выйти из строя.
 Анализ методов дефектоскопии трубопроводов
Сканеры дефектоскопы [23] используют для обследования трубопроводов. Дефектоскоп- прибор для нахождения дефектов в объектах из различных металлических и неметаллических материалов методом неразрушающего контроля. К дефектам относятся появление коррозии, развитие трещин, нарушение целостности структуры и др.
В данном обзоре рассмотрим следующие дефектоскопы:
Вихретоковые
Ультразвуковые
Магнитно-порошковые
Капиллярные
Вихретоковые дефектоскопы.
В основе метода вихретоковой дефектоскопии лежит измерение вихревых токов, возникающих возле подповерхностных дефектов в магнитном поле. При возникновении таких токов на исследуемом участке фиксируются показания электромагнитного поля вихревых токов, образующихся при нахождении дефекта. В результате обработки параметров, имеющих отклонения, можно получить информацию о внутренних дефектах (рисунок 1) [8].
Рис. 1. Принцип работы вихретокового дефектоскопа
Достоинства:
Метод позволяет быстро провести диагностику
Результаты контроля с минимальной погрешностью
Сравнительно невысокая стоимость
Высокая чувствительность
Недостатки:
Глубина исследования до 2мм
Контроль может осуществляться на определённых материалах объекта
Надежность оборудования среднее
Ультразвуковой дефектоскоп
В ультразвуковых дефектоскопах используются эхо-метод и теневой методы контроля. Эхо-метод основан на подаче импульсов и измерении эхо-сигналов (рисунок 2). Принцип действия заключается в отправке ультразвукового сигнала в виде импульса от дефектоскопа к объекту исследования, при этом фиксируется интервал времени прихода эхосигналов, отраженных от дефектов. Метод позволяет обнаруживать поверхностные и глубинные дефекты с различной ориентировкой [7].
Рис. 2. Обнаружение скрытого дефекта с помощью ультразвукового дефектоскопа (эхо-метод)
Рис. 3. Обнаружение скрытого дефекта с помощью ультразвукового дефектоскопа
При теневом методе используют отражатели, установленные напротив друг друга (источник (А) и приемник (В)). Если известно расстояние от А до В и измерено время прохождения волн от А к В, то в результате расчетов можно получить распределение скорости распространения волны на определенном участке объекта исследования(рисунок 3). Таким образом можно обследовать участки на наличие дефектов [12].
Достоинства:
Контроль может осуществляться практически из любых материалов
Широкая распространённость метода
Недостатки:
Высокие требования к состоянию поверхности исследуемого тела (тип, габариты, форма)
Стоимость сравнительно высокая
Время контроля от среднего до длительного
Надежность оборудования среднее
Магнитно-порошковая дефектоскопия
Метод основан на выявлении рассеяния магнитного поля над дефектами (рисунок 4). Этот метод является самым наглядным, т. к. принцип обследования заключается в нанесении магнитного порошка на исследуемый участок, в результате чего при действии магнитного поля частицы намагничиваются и соединяются. Визуально можно наблюдать скопления порошка в зонах трещин. Данный метод позволяет контролировать различные по форме детали, сварные швы, внутренние поверхности отверстий [11].
Рис. 4. Магнитно-порошковый дефектоскоп: 1 – выключатель, 2 – сердечник, 3 – клеммовый щиток, 4 – корпус, 5 – трехжильный кабель, 6, 7 – намагничивающая и дополнительная катушки
Достоинства:
Эффективное и быстрое нахождение поверхностных дефектов
Визуально наглядные результаты
Низкая стоимость
Высокая надежность оборудования
Недостатки:
Трудности, возникающие при размагничивании больших деталей
Недоступность контроля в стыках или узлах, не прибегая к разборке
Невозможность контроля деталей из пластмассы, цветных металлов и некоторых видов сталей.
Ограниченная глубина
Капиллярный дефектоскоп
Метод капиллярной дефектоскопии [24] позволяет обнаруживать невооружённым глазом тонкие поверхностные трещины и несплошности материала. Полости поверхностных трещин заполняют специальными индикаторными веществами (пенетрантами), проникающими в них под действием сил капиллярности. На очищенную от избытка пенетранта поверхность наносят тонкий порошок белого проявителя (окись магния, тальк и т. п.), обладающего сорбционными свойствами, за счёт чего частицы пенетранта извлекаются из полости трещины на поверхность, обрисовывают контуры трещины и ярко светятся в ультрафиолетовых лучах.
Достоинства:
Высокая надежность оборудования
Время контроля среднее
Недостатки:
Нахождение исключительно дефектов, выходящих на поверхность
 Результаты обзора
Резюмируя достоинства, недостатки и принципы действия различных методов [16], можно сделать следующие выводы:
Эффективность выявления коррозионных повреждений (наружных и внутренних) с помощью ультразвуковых дефектоскопов может быть повышена в результате дополнительной обработки результатов дефектоскопии.
Для обследования трубопроводов оптимальными по своим характеристикам и широкому распространению являются ультразвуковые и вихретоковые дефектоскопы.
С внедрением новых моделей дефектоскопов производительность увеличивается, но требуются квалифицированные и подготовленные специалисты для работы с более современной техникой.
Требования в нормативных документов к капиллярному контролю принципиальных различий не имеет, важна чувствительность.
Особое внимание стоит уделять материалу исследуемой поверхности, т. к. от этого зависит точность диагностики и минимальная погрешность.
Адаптация средств вихретокового контроля к электромагнитным свойствам поверхности может значительно увеличить достоверность контроля и уменьшить присутствие человеческого фактора.
 Заключение
В результате проведенного обзора видно, что необходимо проводить дальнейшие исследования для усовершенствования оборудования. Также новые разработки могут существенно повысить надежность диагностики и выявлять проблему контроля состояния труб в отрасли международного уровня.
Своевременное и достоверное определение размеров и конфигурации дефектов исключительно важно для оценок остаточного ресурса компонентов трубопроводов, для планирования и выбора технологии восстановления поврежденных участков, для назначения сроков проведения инспекций.
Литература:
- Афанасьев В. Б., Чернова Н. В. Современные методы неразрушающего контроля // Успехи современного естествознания. — 2011. — № 7 — С. 73–74
- Шмаков В. А., Смирнов Ю. Н., Гиззатуллин Р. Р. Планирование ремонта магистральных трубопроводов по результатам внутритрубной диагностики // Роль науки в развитии топливно-энергетического комплекса. Матер. научн.-практ. конф. 24 октября 2007 г. − Уфа, 2007. — С. 90–92.
- Зубаилов Г. И., Гумеров К. М., Гиззатуллин Р. Р. Ударная вязкость металла и прочность трубопровода // Проблемы и методы обеспечения надежности и безопасности систем транспорта. Матер. научн.-практ. конф. 22 мая 2007 г. — Уфа, 2007. — С. 169–171.
- Поезжаева Е. В. Разработка робота для контроля трубопроводов / Е. В. Поезжаева, А. Г. Федотов, П. В. Заглядов // Молодой ученый. — 2015. — № 16. — С. 218–222.
- Потапов, И. А. Акустические методы и средства неразрушающего контроля и дистанционной диагностики трубопроводов [Текст]: автореф. дис. канд. техн. наук 05.02.11/ Потапов Иван Анатольевич. — Санкт-Петербург, 2007. — С. 26–30.
- Сайфутдинов С. М. Капиллярный контроль: история и современное состояние. М., 2008.
- Жумаев К. К. Выявление внутренних и наружных дефектов трубопроводов ультразвуковыми дефектоскопами [Текст] / К. К. Жумаев, Н. О. Каландаров // Молодой ученый. — 2014. — № 16. — С. 67–68.
- Зацепин Н. Н. Исследование магнитного поля вихревых токов над поверхностными дефектами. Дефектоскопия, 1969, № 4, с. 104–112.
- Р Газпром 2–2.3–620–2011. Методика расчета показателей надежности при эксплуатации объектов линейной части. М., 2011.
- Чистяков В. В., Молотков С. Л. Сравнительный анализ технических возможностей ультразвуковых дефектоскопов общего назначения. В мире неразрушающего контроля. 2002 № 2 с. 40–44.
- Григорьев П. А., Фридман JI.A., Халилеев П. А. Намагничивающая система дефектоскопа для контроля труб подземных магистральных трубопроводов.- Дефектоскопия. 1976, № 4, с.7–17.
- Гурвич А. К., Ермолов И. Н. Ультразвуковой контроль сварных швов.-Киев: Техшка,-1972.
- СНиП III-18–75. Металлические конструкции. М., 1976.
- ГОСТ 23118- 99. Конструкции стальные строительные. Общие технические условия. М., 2001.
- Пособие по методам контроля качества сварных соединений металлических конструкций и трубопроводов, выполняемых в строительстве (к СНиП III-18–75)/ ЦНИИПроектстальконструкция им. Мельникова. –М.: Стройиздат, 1988.
- ГОСТ 18353–79. Контроль неразрушающий. Классификация видов и методов. М., 2004.
- Клюев В. В. Неразрушающий контроль и диагностика. Справочник. -2003.- С. 10–15.
- Щербинский В. Г. Методы дефектоскопии сварных соединений. -1987.- С. 57–64
- Дмитриева В.Д, Мишукова Б. Г. Эксплуатация систем водоснабжения, канализации и газоснабжения. -1988. — С. 124
- Kline R. A., Hsiao C. P., Fidaali M. A. Nondestructive evolution of adhesively bonded joints//Trans.ASME: J.Eng. Mater and Technol. 1986. — 108. — N 3. s. 214–217.
- Pollock A. A. Nondestructive Testing. 1969, — 9. — s. 178.
- Defect Detection in Stainless Stel Uranus 45 FiG-Welded Joints // Materials Evaluation. 1987, -45, N 3, s. 348–352.
- Васильев Н. Н., Исаакян Н. О., Смолянский В. А. Дефектоскоп // Технический Железнодорожный словарь. М., Государственное транспортное железнодорожное издательство.1951.
- Филинов М. В. Капиллярный контроль. –М.: Машиностроение. -2004. С. 736.
moluch.ru
ВИДЫ ДЕФЕКТОВ, НЕРАЗРУШАЮЩИЙ КОНТРОЛЬ И ДИАГНОСТИКА ОБОРУДОВАНИЯ И ТРУБОПРОВОДОВ
Для обеспечения надежной работы машин большое значение имеет периодический контроль их состояния при эксплуатационном обслуживании.
Для определения степени износа и обнаружения появившихся в процессе изготовления или эксплуатации дефектов деталей производятся различные технические измерения.
Дефект — это отдельное несоответствие того или иного изделия или детали установленным требованиям. Дефекты бывают явными и скрытыми, критическими и некритическими. При наличии критического дефекта использование детали по назначению невозможно.
По происхождению дефекты бывают производственными и эксплуатационными.
К производственным дефектамотносятся: усадочные раковины — полости, образующиеся при остывании металла; неметаллические включения, попадающие в металл извне; неравномерность химического состава металла в отливках; волосные трещины, образующиеся внутри толстого проката; закалочные трещины — разрывы металла в процессе закалки. Сюда же можно отнести трещины в зоне сварного шва; непровары —отсутствие сплавления между основным и наплавленным металлом, а также между отдельными слоями при многослойной сварке.
К эксплуатационным дефектамотносятся: трещины усталости —разрывы в детали вследствие длительного действия высоких переменных напряжений, которые возникают в местах концентрации напряжений. Ширина раскрытия трещин усталости не превышает нескольких микрометров. К эксплуатационным дефектам также можно отнести:
• коррозионные поражения металла в результате химического и электрохимического воздействия, масштаб которых зависит от агрессивности среды. Коррозия может быть сплошной, точечной,ячейковой;
• трещины ползучести, которые возникают в металлах по границам зерен при высоких температурах;
• термические трещины, возникающие при резкой смене температур, при недостаточной смазке и заеданиях поверхностей трущихся деталей;
• трещины-надрывы, возникающие при перегрузке деталей при работе в нерасчетном режиме.
Дефекты геометрии трубы могут быть как производственными, так и эксплуатационными: вмятина; гофр — чередующиеся поперечные выпуклости и вогнутости стенки трубы, приводящие к излому оси трубы. Эрозия, вмятина в прокате, риска, расслоение, утонение стенки трубы.
Эксплуатация трубопровода при наличии опасных дефектов допускается при введении ограничений на режимы перекачки.
Причинами дефектов и разрушения валов могут быть причины металлургического характера, когда имеются дефекты в заготовках: поверхностные и внутренние трещины, расслоения и разрывы вследствие механических и термических напряжений, возникающих при изготовлении прутков.
Наиболее опасными с точки зрения возникновения усталостных трещин являются сечения, в которых изменяется диаметр вала (галтельные переходы) и шпоночные пазы в местах посадки рабочего колеса на вал и под муфтой. Разрушение вала может произойти под рабочим колесом под действием циклических нагрузок. Местом зарождения трещин являются шпоночные канавки, где условия работы материала наиболее тяжелые.
Кроме перечисленных дефектов существуют следующие отклонения формы отдельных деталей от проектной: овальность, конусность, бочкообразность, изогнутость, неплоскостность. Существуют также отклонения относительного расположения отдельных деталей в собранном узле: перекос осей и непараллельность, торцевое биение, несоосность, радиальное биение, несимметричность.
Объективная информация о техническом состоянии механизмов получается с помощью средств технической диагностики—информационно-измерительного комплекса, позволяющего анализировать и накапливать информацию. В основу количественной оценки технического состояния положен диагностический параметр. В качестве параметров могут использоваться: мощность навалу; давление; температура; параметры вибрации и т. д.
При диагностировании оборудования и трубопроводов используют следующие важные понятия.
Работоспособность — состояние механизма или иного объекта, при котором он способен выполнять свои функции.
Отказ — событие, заключающееся в нарушении работоспособности механизма или иного объекта (понятие вероятностное).
Неисправность — состояние объекта, при котором он не соответствует одному из требований техдокументации.
Безотказность—свойство объекта непрерывно сохранять работоспособность в течение некоторого периода времени (времени наработки).
Долговечность — свойство механизма сохранять работоспособность до наступления предельного состояния при установленной системе технического обслуживания и ремонта (ТОР).
Срок службы — это все календарное время эксплуатации оборудования (например, насоса) до предельного износа.
Надежность— это свойство объекта выполнять заданные функции. Это главный качественный показатель объекта. Основной показатель надежности — вероятность безотказной работы, которую называют функцией надежности.
В разные периоды эксплуатации насосов частота (интенсивность) отказов разная (рис.1). Здесь три периода: I — приработки; II— нормальной эксплуатации; III— старения.
Природа высокой интенсивности отказов (период!) заключается в неидеальности изготовления деталей и незамеченных дефектах.
Рис.1.Типичный график интенсивности отказов механизмов в процессе эксплуатации
Период внезапных отказов II неустраним, их интенсивность невелика до тех пор, пока износ деталей не достигает некоторой величины — после чего наступает период старения III.
Для оценки параметров надежности насоса необходимо выбрать элемент, лимитирующий надежность. Для насосов такими элементами являются торцовые уплотнения (средняя наработка 3500 ч), щелевые уплотнения (6300 ч), подшипники (12000 ч), валы (60000 ч). Главный резерв повышения параметров надежности насоса—повышение качества торцовых уплотнений.
Межремонтный ресурс насосного оборудования колеблется в пределах 4000—8000 ч. Около 30% всех отказов падают на торцовые уплотнения валов, 15%—-на подшипники, 9% — на маслосистему. Повышенная вибрация вызывает до 10% отказов. По вине персонала — до 12%.
Основной причиной снижения КПД насосов (до 3%) является износ щелевого уплотнения и рост перетока нефти из полости нагнетания во всасывающий патрубок.
Пагубно на состоянии насосов сказывается вибрация, при которых детали испытывают знакопеременные нагрузки и быстро разрушаются. В первую очередь разрушаются подшипники и соединительные муфты. Вибрация ослабляет крепление узлов к фундаменту и узлов между собой.
Не существует машин с идеальным качеством изготовления, поэтому невозможно ликвидировать все процессы, вызывающие вибрацию насосов. Центр масс ротора никогда не совпадает с осью вращения вала. Сила механического дебаланса является основным источником появления вынужденных гармоник вибрации роторных машин. Рост амплитуд отдельных гармоник вибрации используется в качестве диагностического признака наличия дефектов. В 90% случаев аварийной остановки насоса этому предшествует резкое увеличение амплитуды вибраций.
Диагностический метод эксплуатации оборудования сводится к сопоставлению диагностического параметра с допустимым значением. Вибрационная диагностика основана на использовании среднеквадратичного значения виброскорости (мм/с), например, крышки или корпуса подшипника.
Неразрушающий контроль (НК) позволяет обнаружить дефекты и проверить качество деталей без нарушения их пригодности к использованию по назначению. Перечислим несколько существующих методов неразрушающего контроля.
Визуально-оптический метод позволяет выявить относительно крупные трещины, механические повреждения, остаточную деформацию.
Капиллярный метод основан на увеличении контраста между дефектами и бездефектным материалом с помощью специальных проникающих жидкостей.
Ультразвуковой контроль позволяет определить координаты и площадь дефекта. Шуп должен плотно прилегать к поверхности изделия.
Магнитная дефектоскопия основана на том, что дефекты изделий вызывают искажения магнитного поля, наведенного в изделии.
Гамма-дефектоскопия позволяет выявить скрытые дефекты с помощью портативных и маневренных приборов.
Важнейшими характеристиками методов неразрушающего контроля являются чувствительность и производительность. Чувствительность определяется наименьшими размерами выявляемого дефекта. Вышеперечисленные методы позволяют обнаружить трещины раскрытием более 0,001 мм.
Гаммаграфический метод фиксирует трещины, глубина которых составляет 5% от толщины детали.
Неразрушающий контроль валов насосов и электродвигателей проводится с применением визуального, ультразвукового и магнитопорошкового методов при входном контроле, так и при эксплуатации и ремонте. При этом выявляются поверхностные и внутренние трещиноподобные дефекты, раковины и другие нарушения сплошности материала. НК проводится через каждые 10—16 тыс. ч наработки вала в зависимости от мощности и количества пусков насоса.
При выполнении послестроительной дефектоскопии производится проверка:
• внутренней геометрии труб и состояние стенок после укладки и засыпки трубопровода;
• сплошности изоляционного покрытия после его засыпки методом катодной поляризации.
Внутренняя геометрия (вмятины и изгибы) проверяется пропуском калибровочного устройства (снаряда-профилемера) в потоке воды или воздуха. Пропуск осуществляется по технологии пропуска очистного устройства.
Внутритрубная дефектоскопия проводится с целью обнаружения трещин и других дефектов в стенках труб и сварных соединениях. Она проводится в потоке воздуха, природного газа или воды. Режим работы компрессорной или насосной станции должен быть согласован со скоростью перемещения снаряда (обычно используется скорость около 1,0 м/с). Приуве- личении скорости дефектоскопа он дает искаженные данные.
Обнаружение дефектов тела трубы осуществляется внутритрубной инспекцией с помощью снарядов-профилемеров и снарядов-дефектоскопов. Обобщенно их называю внутритрубными инспекционными снарядами (ВИС).
ВИС — это интеллектуальные инспекционные поршни, имеющие стальной корпус и полиуретановые диски. Внутри-трубные инспекционные снаряды имеют опорные ролики и средства обнаружения типа «трансмиттер». Известны случаи преодоления поршнями расстояний свыше 850 км без установки промежуточных камер пуска-приема.
Снаряд-профилемер — это электронно-механический снаряд, оснащенный рычажными датчиками, которые измеряют проходное сечение, положение сварных швов, овальностей, вмятин и гофров. Искривление оси трубопровода фиксируется индикатором поворота по взаимному положению осей двух секций профилемера. Пройденное снарядом расстояние определяется с помощью измерительных колес. Привязка обнаруженных дефектов к определенным сечениям трассы осуществляется с помощью специальных маркеров.
Для внутренней дефектоскопии применяются ультразвуковые и магнитные снаряды-дефектоскопы (табл. 1). Компьютеризированное диагностическое устройство использует метод регистрации отраженных импульсных ультразвуковых сигналов от внутренней и внешней поверхностей трубы. При этом датчик погружен в поток нефти. Толщина стенки определяется по времени запаздывания второго сигнала. Кроме того, сигнал отражается от несплошностей в металле трубы.
Таблица 1. Технические характеристики магнитных снарядов-дефектоскопов при диаметре трубопровода 1220 мм.
Наименование параметров | Значение параметра |
Скорость продвижения по трубе | до 5 м/с |
Максимальная длина обследуемого участка трубопровода | 500 км |
Минимальный проходимый радиус кривизны | 3D |
Точность локации дефектов с использованием маркеров через 2 км: по длине трубопровода | 0,5 м |
Толщина стенок трубопровода: минимальная максимальная | 11 мм 20 мм |
Максимальное давление в трубопроводе | 8 МПа |
Масса прибора | 3500 кг |
Перекачиваемая среда | Газ, газовый конденсат, нефть, вода |
Длина дефектоскопа | 2500 мм |
Время непрерывной работы | 90 часов |
Для более полного обследования необходимо комплексное диагностирование, основанное на различных физических явлениях, потому что внутритрубные измерительные снаряды не выявляют напряженное состояние трубы.
С технической точки зрения техническая диагностика трубопроводов включает в себя следующие действия:
• обнаружение дефектов на трубопроводе;
• проверку изменения проектного положения трубопровода, его деформаций и напряженного состояния;
• оценку коррозионного состояния и защищенности трубопроводов от коррозии;
• контроль технологических параметров транспорта продукта;
• интегральную оценку работоспособности трубопроводов, прогнозирование сроков службы и остаточного ресурса трубопровода.
Система комплексной диагностики линейной части трубопроводов базируется на использовании следующих методов контроля:
• статистических методов оценки эксплуатационных свойств элементов антикоррозийной защиты и интенсивности отказов;
• диагностики состояния металла труб с помощью внутритрубных инспекционных приборов, а также металлографических методов оценки;
• диагностики электрохимической и биологической активности среды на потенциально опасных участках трассы;
• контрольной шурфовки и периодических гидравлических переиспытаний потенциально опасных участков трубопровода.
Выбор интервала времени между измерениями диагностического параметра зависит от его чувствительности к изменению состояния объекта и от степени развития дефекта. Так процесс разрушения подшипника качения от начала появления дефекта занимает 2—3 месяца.
Дополнительный дефектоскопический контроль включает идентификацию дефекта, обнаруженного инспекционным снарядом. Идентификация дефекта заключается в определении типа, границ и размеров дефекта. Контроль проводится персоналом, прошедшим обучение и аттестацию по методам неразрушающего контроля.
megaobuchalka.ru
Контроль труб и сварных соединений ультразвуковым методом
Для промышленных инженерных коммуникаций введен ряд стандартов, подразумевающих довольно жесткую проверку соединений. Эти методики переносятся на системы, находящиеся в частном владении. Применение методов позволяет избежать аварийных ситуаций и провести наружный и скрытый монтаж с требуемым уровнем качества.
Входной контроль
Входной контроль труб проводится для всех типов материалов, включая металлопластиковые, полиэтиленовые и полипропиленовые после покупки изделий.
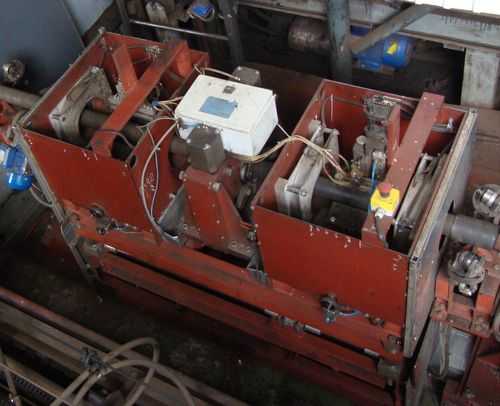
Входной контроль труб
Упоминаемые стандарты подразумевают проверку труб, независимо от материала, из которого они изготовлены. Входной контроллинг подразумевает правила проверки получаемой партии. Проверка сварных соединений проводится в рамках приемки работ по монтажу коммуникаций. Описываемые способы обязательны к применению строительно-монтажными организациями при сдаче жилых, коммерческих и промышленных объектов с системами водоснабжения и отопления. Похожие способы применяются, где необходим контроль качества труб в коммуникациях промышленного типа, действующих в составе оборудования.
Последовательность проведения и методики
Приемка продукции после поставки является важным процессом, впоследствии гарантирующим отсутствие нерациональных затрат на замену трубной продукции и аварий. Тщательной проверке подлежит, как количество продукции, так и ее особенности. Количественная проверка позволяет учитывать весь расход продукции и избежать лишних затрат, связанных с завышенными нормами и нерациональным использованием. Нельзя упускать и влияние человеческого фактора.
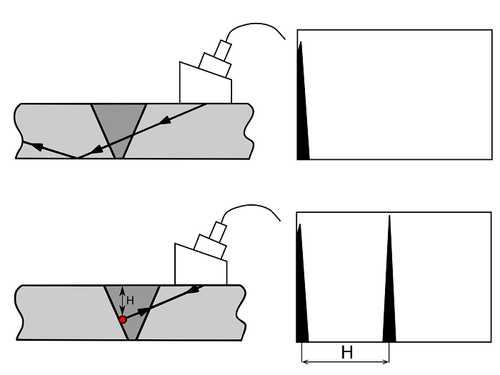
Схема работы ультразвука
Работы проводятся в соответствии с разделом № 9 стандарта СП 42-101-96.
Последовательность входных мероприятий следующая:
- Проверка сертификата и соответствия маркировки;
- Выборочные испытания образцов проводятся при сомнениях в качестве. Исследуется величина предела текучести при растяжении и удлинении при механическом разрыве;
- Даже при отсутствии сомнений в поставке отбирается небольшое количество образцов для испытаний, в пределах 0,25-2% партии, но не менее 5 шт. При использовании продукции в бухтах, отрезают 2 м;
- Проводится осмотр поверхности;
- Осматривается на предмет вздутий и трещин;
- Измеряют типовые размеры толщин и стенок микрометром или штангенциркулем.
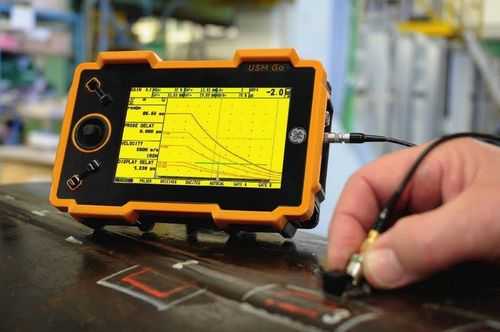
Ультразвуковая проверка труб
При официальной проверке коммерческой или государственной организацией по факту проведения процедуры составляется протокол.
Неразрушающий контроль – особенности
Неразрушающие способы используются в функционирующих системах инженерных коммуникации. Особенное внимание уделяется реальному состоянию металла и сварным соединениям. Безопасность эксплуатации определяется качеством сварки швов. При длительной эксплуатации исследуется степень повреждения конструкции между соединениями. Они могут быть повреждены ржавчиной, что приводит к истончению стенок, а засорение полости может привести к повышению давления и прорыву трубопровода.
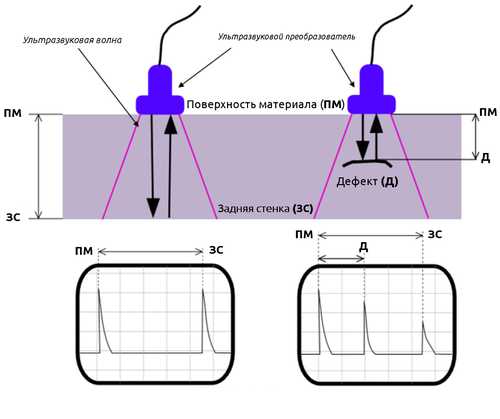
Обнаружение дефекта трубы
Для этих целей предложено специализированное оборудование – дефектоскопы (например, ультразвуковые), которые могут применяться для проведения работ в частных и коммерческих целях.
В исследованиях трубопроводов применяют методы контроля труб:
- Вихретоковые – основаны на измерении вихревых токов в дефектах. Способ обладает довольно высокой точностью, позволяет исследовать поверхность на глубину 2 мм и установить возможные места прорывов;
- Ультразвуковые – используются эхо- и теневые сигналы, позволяющие установить наличие дефектов. Довольно дорогостоящий и требовательный метод;
- Капиллярные – предназначены для визуального обнаружения дефектов, прежде всего, мелких трещин и расколов, которые могут образовывать течь. Используют порошок, который активизируют с помощью проявителя. Используется не только на металлических, но и полиэтиленовых трубах;
- Магнито-порошковые – связаны с рассеиванием магнитного поля над имеющимися дефектами. Используется магнитный порошок или раствор (например, testex), оценивается визуально. Применяется, прежде всего, для проверки сварки.
-
Дефекты сварных швов
С помощью данного оборудование отслеживается развитие трещин или нарушение целостности. Причем основным достоинством является определение скрытых дефектов. Очевидно, что каждый из этих методов показывает высокую эффективность на определенных видах повреждений. Вихретоковый дефектоскоп в какой-то степени является универсальным и оптимальным по стоимости.
Ультразвуковой контроль труб – более дорогое удовольствие и требовательно, но очень популярно среди специалистов благодаря сформировавшемуся стереотипу. Многие сантехники используют капиллярный и магнитопорошковый метод, который применим для всех видов трубной продукции, включая полиэтиленовые и полипропиленовые. Среди специалистов популярно средство Testex для проверки герметичности сварки.
Заключение
Из предложенных способов неразрушающего контроля все 4 варианта успешно используются на практике, но не обладают абсолютной универсальностью. Система контроля труб включает в себя все виды дефектоскопов для проведения работ. Некоторой степенью универсальности обладает ультразвуковой способ, а также методика, основанная на вихревых токах. Причем вихревой вариант оборудования обходится значительно дешевле.
trubygid.ru
СУЩЕСТВУЮЩИЕ ПРОБЛЕМЫ И ПУТИ ИХ РЕШЕНИЯ – Эгида
НЕРАЗРУШАЮЩИЙ КОНТРОЛЬ МАГИСТРАЛЬНЫХ ТРУБОПРОВОДОВ: СУЩЕСТВУЮЩИЕ ПРОБЛЕМЫ И ПУТИ ИХ РЕШЕНИЯ
А.Н. Мисейко
Статья представляет собой обзор актуальных проблем, возникающих при проведении НК на стадиях изготовления, монтажа и эксплуатации магистральных трубопроводов. Особое внимание уделено задачам, стоящим перед НК в процессе эксплуатации магистральных трубопроводов и путям их решения. На сегодняшний день сеть магистральных трубопроводов покрывает 35% территории России, на которой проживает около 60% населения, пересекая автомобильные и железные дороги, водоемы и лесные массивы, иногда проходя в непосредственной близости от населенных пунктов [1]. Поскольку транспортируемыми средами в большинстве случаев являются углеводородное сырье и продукты его переработки, обладающие пожаро- и взрывоопасностью, вопросам обеспечения надежности и безопасности магистральных трубопроводов придается огромное значение.
Надежность и безопасность магистральных трубопроводов определяются их техническим состоянием, которое, в свою очередь, напрямую зависит от наличия и степени опасности дефектов в основном металле труб и сварных соединениях. Эти дефекты в зависимости от условий их возникновения можно разделить на три группы:
- Дефекты, допущенные при изготовлении элементов трубопроводов на трубопрокатных заводах;
- Дефекты, допущенные при выполнении строительно-монтажных работ на трассе;
- Дефекты, возникшие в процессе эксплуатации от воздействия различных факторов (коррозионной агрессивности транспортируемой и окружающей сред, силовых и температурных нагрузок, деформационного старения сталей и т.д.).
Для выявления вышеуказанных дефектов используются различные методы и средства неразрушающего контроля (НК), применение которых на стадиях изготовления, монтажа и эксплуатации магистральных трубопроводов имеет свои особенности. Исходя из типа и параметров дефектов, характерных для каждой стадии, устанавливаются требования к выбору методов и средств НК.
Рассматривая вопросы проведения НК на стадиях изготовления и монтажа, следует отметить, что сами процессы изготовления и монтажа хорошо изучены и отлажены, происходят в известных условиях с использованием идентичных материалов [2, 3]. Поэтому процедура НК может быть включена в общий производственный цикл и выполняться в поточном режиме. Главными проблемами НК на указанных стадиях являются повышение достоверности результатов контроля и согласование процесса НК с ритмичностью основных производственных процессов. Свободный доступ к поверхности контролируемых элементов и относительная стабильность условий контроля позволяют использовать весьма широкий спектр методов и автоматизировать многие операции НК, что обеспечивает соответственно высокую достоверность полученных результатов и большую производительность контроля. Дальнейшие пути повышения эффективности НК при изготовлении и монтаже магистральных трубопроводов связаны с увеличением числа дублирующих методов и многократностью контроля, а также полной автоматизацией всей процедуры НК, включая оценку его результатов.
В отличие от предыдущих стадий при проведении НК в процессе эксплуатации магистральных трубопроводов возникают более сложные проблемы, которые содержат как техническую, так и организационную составляющие.
Технические проблемы обусловлены, в основном, влиянием условий эксплуатации магистральных трубопроводов на достоверность и производительность НК, ограниченными возможностями самих методов НК для выявления дефектов, а также несовершенством существующих критериев оценки результатов контроля. В зависимости от способа обследования трубопроводов указанные факторы могут иметь разную значимость.
На сегодняшний день существует два способа обследования магистральных трубопроводов: изнутри (с помощью внутритрубных инспекционных снарядов) и снаружи (при подземной прокладке – путем экскавации трубопровода). Каждый из этих способов имеет свои достоинства и недостатки. Безусловным достоинством внутритрубного обследования является возможность 100%-го контроля трубопровода по всей протяженности. К числу недостатков этого способа можно отнести необходимость специальной подготовки трубопровода к пропуску внутритрубных инспекционных снарядов (ВИС), а именно – сооружение камер пуска-приема ВИС, очистка внутренней полости от отложений (для нефтепроводов), устранение недопустимых сужений проходного сечения и крутых поворотов, препятствующих прохождению ВИС. Кроме того, число методов НК, применяемых при внутритрубном способе обследования, сильно ограничено (на жидкостных трубопроводах используются ультразвуковой и магнитный методы, а на газопроводах – только магнитный), их чувствительность и точность ниже по сравнению с аналогичными параметрами в стационарных условиях, а результаты контроля в ряде случаев (при наличии сварных соединений на подкладных кольцах и неметаллических вкладышах) неоднозначны. К тому же стоимость внутритрубного обследования довольно высока (для уточнения координат и размеров дефектов необходимо осуществить несколько прогонов ВИС), а степень опасности выявленных дефектов определяется на основании сложных расчетов, требующих большого количества данных [4].
При проведении обследования магистральных трубопроводов снаружи спектр применяемых методов НК намного шире и, кроме ультразвукового и магнитного, могут быть использованы радиационный, капиллярный, вихретоковый и ряд других методов. Их применение регламентируется нормативно-техническими документами основных российских операторов трубопроводного транспорта – ОАО «АК «Транснефть» [5] и ОАО «Газпром» [6]. К числу достоинств данного способа обследования магистральных трубопроводов можно отнести использование наружных средств НК с более высокой чувствительностью и точностью чем у ВИС, а также возможность применения большего количества методов, что позволяет существенно повысить достоверность контроля. Однако наружный способ обследования имеет серьезные недостатки: большинство применяемых методов НК требует значительного объема подготовительных работ (экскавация, снятие изоляции, зачистка контролируемой поверхности), обладают низкой производительностью, а на результаты контроля оказывают сильное влияние свойства материала трубопровода, состояние поверхности, ориентация и расположение выявляемых дефектов. При этом ключевым показателем опасности дефекта является его площадь или объем без учета динамики дальнейшего развития [5-7].
Таким образом, решение вышеперечисленных технических проблем заключается в разработке и внедрении таких методов и средств НК, которые бы обладали высокой чувствительностью и точностью при выявлении большого класса дефектов вне зависимости от условий эксплуатации магистральных трубопроводов, обеспечивали высокую достоверность и производительность контроля при минимальном объеме подготовительных работ, а также позволяли адекватно оценивать степень опасности дефектов. Анализируя сегодняшнее состояние рынка разработки средств НК магистральных трубопроводов в процессе эксплуатации, можно сделать вывод о том, что появление технологий и приборов, полностью удовлетворяющих всем сформулированным требованиям, в ближайшее время маловероятно. Создание их представляет собой сложную задачу. Тем не менее, разработки в подобном направлении ведутся и со временем такие технологии и приборы появятся.
ООО «Интерюнис», имея большой опыт проведения НК магистральных трубопроводов и обладая уникальными научно-техническими разработками в области приборостроения, ведет активную работу по созданию и внедрению новых технологий и средств НК, обеспечивающих решение ранее упомянутых задач. В качестве основного физического метода НК, на базе которого выполняется разработка, выступает метод акустической эмиссии (АЭ). Он обладает высокой чувствительностью к наиболее опасным (развивающимся) дефектам, обеспечивает интегральную оценку технического состояния протяженных участков трубопроводов и учитывает динамику развития дефектов при оценке их степени опасности. ООО «Интерюнис» широко применяет собственные разработки в практике проведения НК магистральных трубопроводов. В частности, на основе исследований по распространению в трубопроводах волн Лэмба разработан и используется метод интегрального измерения толщины на протяженных участках, а также метод определения координат источников акустической эмиссии (АЭ) за пределами локационных групп (по сигналам АЭ, пришедшим всего лишь на один датчик). Для реализации комплекса описанных методов создано интеллектуальное программное обеспечение A-Line OSC Processing, доказавшее свою эффективность. Осуществляется разработка алгоритмов беспороговой регистрации сигналов АЭ, что позволит уверенно выделять «полезные» сигналы и проводить АЭ-контроль в условиях сильных технологических шумов и неблагоприятных погодных условиях. Разработаны и проходят апробацию алгоритмы автокалибровки и авторасстановки датчиков АЭ, применение которых соответственно повышает надежность контроля и увеличивает точность локализации источников АЭ. В настоящий момент завершается работа над созданием 2-х канальной компактной диагностической системы, обеспечивающей выполнение в полевых условиях целого спектра измерений (толщины, напряжений и деформаций, параметров АЭ, вибрации и т.п.), обладающей высокими метрологическими и техническими характеристиками, простой и удобной в использовании.
Однако, как уже было упомянуто выше, кроме технических проблем в сфере услуг по НК магистральных трубопроводов имеются и организационные проблемы. Они обусловлены, в первую очередь, сложившейся за последние годы негативной тенденцией увеличения числа недобросовестных поставщиков услуг – организаций, выполняющих работы по НК с низким качеством. Этот факт спровоцирован, по большей части, трубопроводными компаниями, для которых главным критерием в выборе подрядной организации по НК является низкая стоимость оказываемых ею услуг. Ситуация осложняется еще и тем, что сами эксплуатирующие компании в целях максимально возможной экономии бюджета устанавливают расценки на проведение НК ниже минимально приемлемой рыночной цены, при этом формально заявляя высокие требования к качеству выполняемых работ. В этих условиях проигрывают крупные компетентные организации, которые вынуждены отказываться от проведения ряда работ, поскольку количество и компетентность специалистов, наличие и содержание приборного парка заведомо определяют более высокую ценовую категорию. Таким образом, тендер на проведение работ может быть выигран фирмами-«однодневками» и фирмами, у которых зачастую нет необходимого оборудования и квалифицированных сотрудников, что соответственно отрицательно сказывается на качестве контроля.
К числу организационных проблем можно отнести и проблемы связанные с недостатком нормативно-технических документов, устанавливающих современные подходы к проведению НК в процессе эксплуатации трубопроводов. В частности, полностью отсутствуют документы, регламентирующие применение систем мониторинга на потенциально опасных участках магистральных трубопроводов и оценку состояния трубопроводов по результатам мониторинга. Зачастую нормативно-технические и руководящие документы содержат стереотипные подходы и не учитывают современный опыт проведения НК, что искусственно снижает эффективность и производительность ряда методов.
Для решения обозначенных организационных проблем представляется необходимым продолжить совершенствование законодательства в части проведения тендеров и торгов, полнее задействовать механизмы саморегулирования в рамках Федерального закона №315-ФЗ [8], а также сделать доступной и объективной процедуру формирования минимальной рыночной цены на услуги по НК. Путем взаимодействия саморегулируемых организаций и ассоциаций экспертов с трубопроводными компаниями следует изменить критерии выбора подрядных организаций, основываясь не только на стоимости услуг, но и на опыте подобных работ, количестве высококвалифицированных специалистов, наличии и состоянии приборного парка, принимая во внимание наличие и актуальность научно-технических и методических разработок, наличие и уровень внутренних стандартов и регламентов организации, членство в союзах и ассоциациях, отзывы специализированных предприятий. В части разработки актуальной нормативно- технической и методической документации необходимо активнее работать с научно- производственными союзами и ассоциациями, привлекая к разработке и рассмотрению документации широкий круг профильных организаций.
ООО «Интерюнис» занимает активную позицию в решении перечисленных организационных проблем, являясь одним из членов Научно-производственного союза «РИСКОМ», который объединяет ведущие российские организации в области НК, технической диагностики и экспертизы. Под эгидой НПС «РИСКОМ» осуществляется разработка актуальных нормативно-технических документов. В настоящий момент проводится работа по созданию стандарта организации, регламентирующего выбор методов и средств НК для мониторинга опасных производственных объектов, в том числе магистральных трубопроводов. ООО «Интерюнис» ведется также разработка методик, учитывающих современные требования к проведению НК [9].
В заключение, следует отметить, что хотя решение организационных и технических проблем представляется весьма сложным процессом, эта цель все же является достижимой и для этого существуют все предпосылки.
Литература
- Безопасность России. Правовые, социально-экономические и научно-технические аспекты. Безопасность трубопроводного транспорта / И.И. Мазур, О.М. Иванцов и др. – М.: МГФ «Знание», 2002. – 629 с.
- СНиП III-42-80* Магистральные трубопроводы. Правила производства и приемки работ. – М.: ГУП ЦПП, 2001. – 75 с.
- ВСН 012-88 Строительство магистральных и промысловых трубопроводов. Контроль качества и приемка работ. Части 1, 2. – М.: Миннефтегазстрой, 1990. – 103 с.
- ОСТ 23.040.00-КТН-574-06 Стандарт отрасли. Нефтепроводы магистральные. Определение прочности и долговечности труб и сварных соединений с дефектами. – М.: ОАО «АК «Транснефть», 2006. – 107 с.
- РД 19.100.00-КТН-001-10 Неразрушающий контроль сварных соединений при строительстве и ремонте магистральных трубопроводов. – М.: ОАО «АК «Транснефть», 2009. – 145 с.
- СТО Газпром 2-2.4-083-2006 Инструкция по неразрушающим методам контроля качества сварных соединений при строительстве и ремонте промысловых и магистральных газопроводов. – М.: ООО «Научно- исследовательский институт природных газов и газовых технологий – ВНИИГАЗ», 2006. – 126 с.
- ОР-19.100.00-КТН-010-10 Порядок проведения дополнительного дефектоскопического контроля дефектов труб магистральных трубопроводов. – М.: ОАО «АК «Транснефть», 2009. – 123 с.
- Федеральный закон №315-ФЗ от 01.12.2007 г. «О саморегулируемых организациях».
- Методика акустико-эмиссионного контроля сварных соединений линейной части магистрального газопровода. Общие положения. / Согласована Управлением по технологическому и экологическому надзору по Свердловской области и ООО «Газнадзор» (исх. № 30/45-14-4б от 03.03.2005). – Екатеринбург: ИТЦ ООО «Уралтрансгаз» ОАО «Газпром», 2005. – 31 с.
aegis-rus.com
Неразрушающий контроль трубопроводов заказать | НПК Сибирь
Наша лаборатория на протяжении 10 лет занимается неразрушающими методами контроля качества сварки любых металлоконструкций. «Контроль трубопроводов», или неразрушающий контроль сварных соединений трубопроводов, является одной из услуг компании «НПК Сибирь».
Наши аттестованные специалисты проводят контроль качества сварки трубопроводов в Томске, Томской области и других регионах РФ. В нашем портфолио имеются разнообразные объекты инфраструктуры – резервуары, магистральные и технологические трубопроводы, трубопроводные пути, дюкеры и другие надземные и подземные сооружения химической, нефтегазовой промышленности.
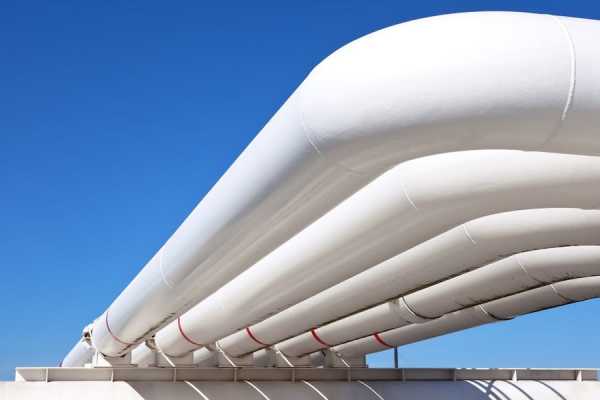
Неразрушающий контроль трубопроводов
Зачем проводить неразрушающий контроль трубопроводов
Трубопроводы выполняют важную транспортную функцию по доставке газа, нефти и разнообразного сырья. Наличие одного дефекта может остановить большое предприятие и нанесет ему огромные убытки. Чтобы этого не произошло, проверяются все компоненты: качество металла, квалификация сварщиков, правильность сварных швов.
Особое внимание уделяется контролю сварных соединений трубопроводов, герметичность которых должна быть абсолютной. Этого можно добиться благодаря полному отсутствию недопустимых дефектов.
Контроль качества сварных соединений трубопроводов
Неразрушающий контроль качества сварки трубопроводов позволяет определить любые изъяны, которые могут возникнуть. Существует несколько разновидностей:
- Наружные. Находятся на глубине не более 3 мм. К ним относится прожог, наплыв, поры (внутренние и наружные).
- Внутренние. Образовываются внутри конструкции, из-за чего их нельзя определить при визуальном осмотре. Проявляются как непровар, трещины, несплавления, поры, включения шлака и т.д.
Для выявления любых недостатков сварного шва был разработан неразрушающий контроль (НК), которой вобрал в себя разнообразные методы. Процедура проводится в соответствии с отечественными нормативными документами.
Как выявляются дефекты сварочных работ
В зависимости от оборудования, которое применяется, методы контроля сварочных работ трубопроводов разделяются на несколько видов.
Контроль трубопроводов: обнаружение внешних дефектов
- Визуальный. Проводится осмотр всей длины проваренной конструкции. Такое выявление нарушений сварного шва трубопровода проводится только для наружных изъянов.
- Магнитный. Для его проведения используется магнитный порошок. Вещество наносится на предварительно намагниченный шов. При обнаружении дефектов, суспензия обретает специальную форму повторяющую поверхностные и под поверхностные дефекты.
- Проникающими веществами. Используется специальная жидкость (пенетрат). Она наносится на контролируемые соединения и проникает во все микротрещины и заполняет поры. Далее проводится визуальный осмотр.
Глубинные дефекты обнаруживаются следующими методами контроля трубопроводов:
- Рентгенографический контроль сварки швов и сварных соединений — исследование внутренней структуры объектов, которые проецируются при помощи рентгеновских лучей на специальную плёнку или бумагу. Благодаря таким технологиям можно увидеть все дефекты в сварном шве трубопроводов.
- Ультразвуковая дефектоскопия (ультразвуковой контроль сварных соединений трубопроводов) — метод, предложенный С. Я. Соколовым в 1928 году и основанный на исследовании процесса распространения ультразвуковых колебаний с частотой 0,5 — 25 МГц в контролируемых изделиях с помощью специального оборудования — ультразвукового преобразователя и дефектоскопа. Является одним из самых распространенных методов неразрушающего контроля.
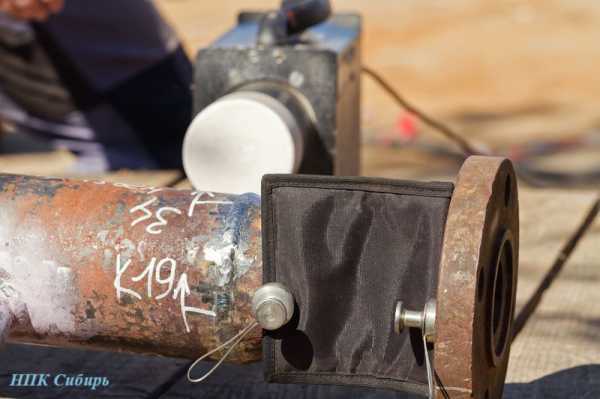
рентгенография на эллипс
Заказывайте услуги нашей компании ООО «НПК Сибирь» и гарантированно получите контроль качества сварных швов и соединений трубопроводов, проведенный на высоком уровне.
☎ (3822) 511-001
npksibir.ru
ГОСТ 25225-82 Контроль неразрушающий. Швы сварных соединений трубопроводов. Магнитографический метод
ГОСУДАРСТВЕННЫЙ СТАНДАРТ СОЮЗА ССР
КОНТРОЛЬ НЕРАЗРУШАЮЩИЙ
ШВЫ СВАРНЫХ СОЕДИНЕНИЙ
ТРУБОПРОВОДОВ
МАГНИТОГРАФИЧЕСКИЙ МЕТОД
ГОСТ 25225-82
ГОСУДАРСТВЕННЫЙ КОМИТЕТ СССР ПО СТАНДАРТАМ
Москва
РАЗРАБОТАН Министерством строительства предприятий нефтяной и газовой промышленности СССР
ИСПОЛНИТЕЛИ
Э. Е. Остров, Н. М. Егорычев, М. Х. Хусанов, В. Н. Смирнов, Г. Е. Герасимова, А. С. Борейко, Л. И. Кауфман
ВНЕСЕН Министерством строительства предприятий нефтяной и газовой промышленности СССР
Член Коллегии Г. А. Арендт
УТВЕРЖДЕН И ВВЕДЕН В ДЕЙСТВИЕ Постановлением Государственного комитета СССР по стандартам от 23 апреля 1982 г. № 1644
ГОСУДАРСТВЕННЫЙ СТАНДАРТ СОЮЗА ССР
Контроль неразрушающий ШВЫ СВАРНЫХ СОЕДИНЕНИЙ ТРУБОПРОВОДОВ Магнитографический метод Non-destructive testing. Welded joints of tubing. Magnetographic method. |
ГОСТ |
Постановлением Государственного комитета СССР по стандартам от 23 апреля 1982 г. № 1644 срок действия установлен
с 01.07.1983 г.
до 01.07.1988 г.
Настоящий стандарт устанавливает магнитографический метод неразрушающего контроля сплошности кольцевых стыковых сварных швов стальных трубопроводов различного диаметра с толщиной стенки от 2 до 25 мм, выполненных сваркой плавлением.
Магнитографический метод может применяться для контроля сварных соединений других конструкций цилиндрической формы.
Стандарт не распространяется на контроль угловых, нахлесточных и тавровых соединений и швов, выполненных методами контактной сварки.
Необходимость проведения магнитографического контроля, объем контроля и нормы допустимых дефектов устанавливаются в технической документации на контроль стыковых швов трубопроводов.
Термины, применяемые в стандарте, и их определения приведены в справочном приложении 1.
1. ОСНОВНЫЕ ПОЛОЖЕНИЯ
1.1. Магнитографический метод контроля служит для выявления в стыковых сварных швах трубопроводов из низко- и среднелегированных и углеродистых ферромагнитных сталей наружных и внутренних трещин, непроваров, ц
files.stroyinf.ru